Eine lange Partnerschaft
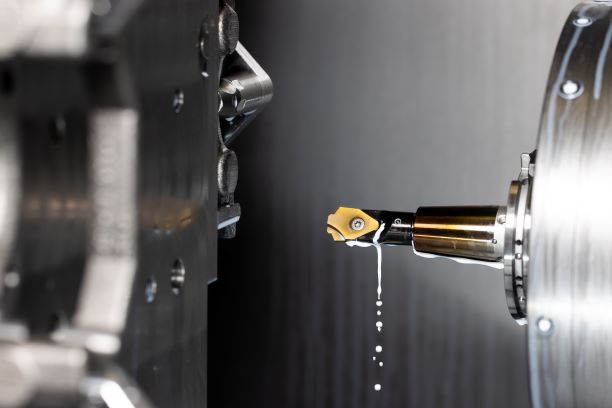
„Unsere Qualität zahlt Dich aus.“ So lautet das interne Firmenmotto der Knott GmbH aus dem bayrischen Eggstätt. Dieses Motto lebt der Inhaber und Geschäftsführer Valentin Knott seinen Mitarbeitern täglich vor. Seit über 40 Jahren lenkt er das Unternehmen, welches sich auf die Entwicklung und Fertigung im Bereich der Bremsen- und Trailertechnik spezialisiert hat. „Kurz nach meinem Start hier im Unternehmen begann auch die Partnerschaft mit der Paul Horn GmbH als Werkzeuglieferant“, so Knott. Seither kommen in seiner Fertigung zahlreiche Systeme des Tübinger Werkzeugspezialisten zum Einsatz. Auch für neue Werkzeug- und Maschinentechnologien hat man bei Knott immer ein offenes Ohr. „Wir suchen ständig nach noch neuen Maschinen- und Werkzeuglösungen, um unsere Prozesse noch produktiver zu gestalten“, erzählt der Leiter der mechanischen Fertigung Andreas Neubauer.
„Mein Vater gründete das Unternehmen im Jahr 1937. Seit der Gründung entwickelte sich das Unternehmen Knott vom Zulieferer für Getriebe zu einem weltweit führenden Hersteller der Bremsen- und Trailertechnik“, erzählt Knott. Die Qualität spielt im Unternehmen eine große Rolle. Neben vollautomatisierten Fertigungszellen arbeitet man bei Knott auch noch handwerklich. Aktuell arbeiten weltweit rund 2.500 Menschen bei Knott. Im Geschäftsbereich der Bremsentechnik produziert das Unternehmen Trommelbremsen, Scheibenbremsen, nasse Vollscheibenbremsen sowie Elektromagnetbremsen. Diese Systeme kommen unter anderen bei Fahrzeugen aus der Landwirtschaft, Bau- und Miningindustrie, Militärtechnik und bei Flurförderfahrzeugen zum Einsatz. Bei der Trailertechnik liefert Knott das Fahrgestell, die Achsen und Anbauteile mit weiterem Zubehör an seine Kunden. Die Knott-Trailertechnik rollt beispielsweise als Wohnwagen, Pferdeanhänger, Bootsanhänger sowie als klassischer Transporttrailer über die Straßen.
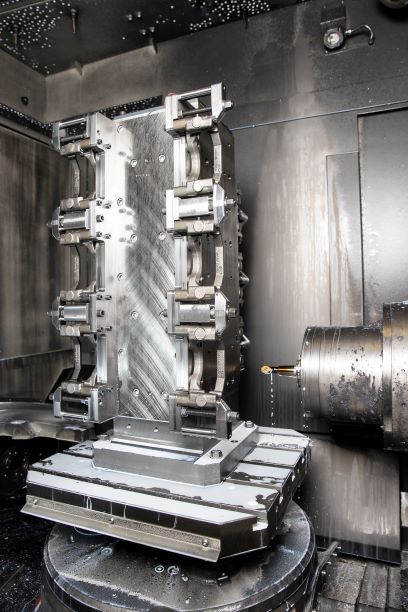
Optimierungspotenzial
„Der kontinuierliche Verbesserungsprozess spielt in unserer Fertigung eine tragende Rolle. Wir suchen beinahe täglich nach den Stellschrauben, wie wir unsere Fertigungsprozesse weiter optimieren können“, so Neubauer. Die Fertigung der Aufnahmebohrungen an einem Bremsträger war eine dieser Stellschrauben, an der Neubauer drehen wollte. Der Träger aus Sphäroguss kommt in Bremsensystemen von Bau- und Landwirtschaftsmaschinen zum Einsatz. Von diesem Trägertyp fertigt Knott rund 10.000 Stück pro Jahr. Die Bohrung mit Senkung und die Fase/Senkung fertigte man in drei Arbeitsgängen: Vorbohren, Aufbohren und Senken. „Diese drei Arbeitsschritte wollten wir zu einem Arbeitsgang zusammenfassen“, erzählt Neubauer.
Mit dieser Anforderung wandte sich der Leiter der mechanischen Fertigung an den für Knott zuständigen Horn-Außendienstmitarbeiter Michael Götze. Er schlug vor, die Bohrung in einem Arbeitsgang mit dem Horn-Formbohrsystem D117 zur fertigen. „Das Horn-Schneidplattensystem 117 eignet sich neben Form-Stechdrehoperationen auch sehr gut zum Formbohren“, erklärt Götze. Mit dem Profil der zu fertigenden Bohrung machten sich die Horn-Konstrukteure in Tübingen an die Arbeit und konstruierten die passende Werkzeuglösung. Die ersten Versuche bei Knott waren gleich erfolgreich und so stellte Neubauer die Fertigungspläne des Bremsträgers auf die Horn-Lösung um. „Die gesamte Umsetzung dauerte fünf bis sechs Wochen. Diese Zeit beinhaltet die technische Klärung, Anfrage, Zeichnung, Freigabe, Produktion und den Einsatz in unserer Fertigung. Wir sind mit dieser schnellen Umsetzung unserer Anfrage sehr zufrieden“, erzählt Neubauer.
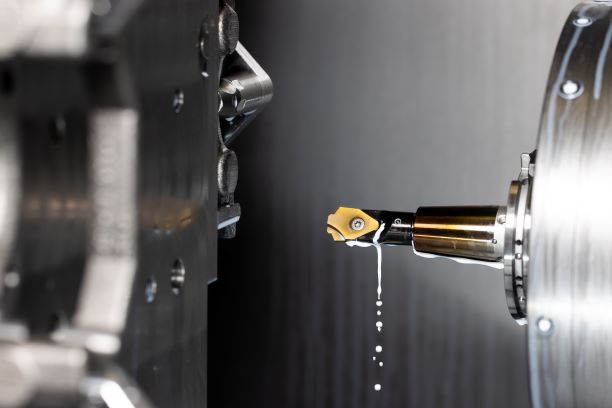
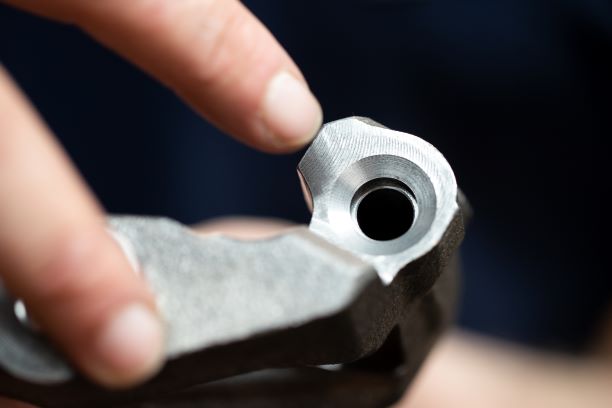
Hohe Zeiteinsparung
Im Einsatz bohrt das D117-Formbohrwerkzeug das Bohrungsprofil jetzt in einem Arbeitsgang. Die Schnittgeschwindigkeit liegt bei vc = 120 m/min, bei einem Vorschub von f = 0,25 mm/U. Neben den gesparten Werkzeugwechseln der Maschine verbesserte sich die Bearbeitungszeit um 30 Sekunden. Dies ergibt bei einer Stückzahl von 10.000 Stück eine jährliche Einsparung von rund 83 Stunden. Des Weiteren erhöhte sich auch die Standzeit im Vergleich zu den vorher eingesetzten Werkzeugsystemen. „Die genaue Standzeit können wir noch nicht festlegen, da die erste Schneidplatte nach 1.000 gefertigten Bohrungen immer noch im Einsatz ist“, so Neubauer. Zum Einsatz kommt bei der Fertigung eine Mazak F6800. Die FH-6800 von Mazak ist ein horizontales Hochgeschwindigkeits-Bearbeitungszentrum, das konstruktionsbedingt mit einer sehr hohen Verwindungssteifigkeit für höchste Bearbeitungsgenauigkeit in der Schwerzerspanung überzeugt.
Die profilierten Werkzeuge des Bohrsystems D177 ermöglichen wirtschaftliche Vorteile in der Serienproduktion sowie die Reduzierung der Werkzeugkosten bei Bohrungen in einem großen Durchmesserbereich. Horn bietet auf Basis des Werkzeugsystems 117 die profilierten Schneidplatten nach Kundenwunsch für den Einsatz auf Dreh- und Fräszentren. Eine hohe Rund- und Planlaufgenauigkeit sowie Wechselgenauigkeiten im μm-Bereich garantiert der Präzisionsplattensitz des Systems 117. Die präzisionsgeschliffenen Schneiden ermöglichen eine hohe Fertigungspräzision von Toleranzen bis 0,02 mm und hohe erreichbare Oberflächengüten. Die Kostenersparnis zeigt sich durch die Möglichkeit der Nachbestückung, die geringeren Werkzeugkosten sowie den reduzierten Maschinenstillstand durch den schnellen Schneidplattenwechsel. Des Weiteren wird dies deutlich durch geringere Beschichtungskosten, da nur die Schneidplatte beschichtet ist. Die Kühlung der Kontaktzone und den Abtransport der Späne sichert die innere Kühlmittelzufuhr durch den Rundschafthalter auf beide Schneiden.
Zum Einsatz kommen in den Knott-Standorten hauptsächlich Bearbeitungszentren des japanischen Maschinenbauers Mazak. „Wir haben gute Kontakte zu Mazak nach Japan“, erzählt Knott. Verteilt an den verschiedenen Standorten sind rund 150 Bearbeitungszentren installiert. Allein in Eggstätt stehen 50 Mazak-Maschinen. „Wir sind von der Leistung, Präzision und der Langlebigkeit überzeugt“, so Knott. Man beschränkt sich jedoch nicht nur auf einen Hersteller. So hat man erst kürzlich eine vollautomatisierte Fertigungszelle des italienischen Maschinenbauers Famar in Eggstätt in Betrieb genommen. „Mit dieser Zelle bearbeiten wir doppelspindlig unsere Bremssättel“, sagt Neubauer.
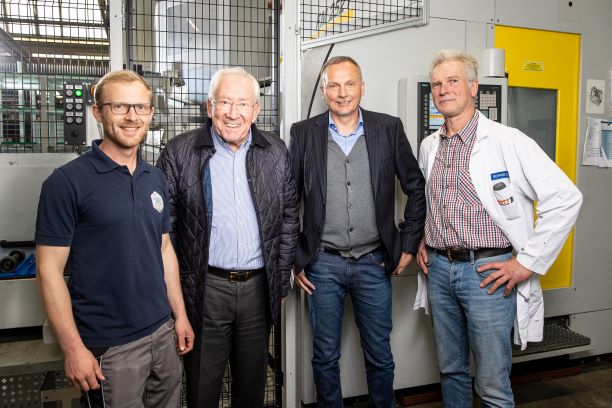
Einer der langjährigsten Horn-Kunden
Mit über 40 Jahren Zusammenarbeit ist das Unternehmen Knott einer der langjährigsten Horn-Kunden. Zahlreiche Werkzeugsysteme von Horn tragen zu der hohen Qualität der Knott-Produkte bei. Neben den neuen Bohrwerkzeugen setzt Knott auf Systeme zum Stechdrehen, Fräsen und Reiben der Paul Horn GmbH. „Wir sind froh, so einen langjährigen Werkzeugpartner an unserer Seite zu haben, der uns bei unserer täglichen Arbeit unterstützt und uns regelmäßig neue und noch produktivere Werkzeuglösungen liefert“, resümiert Knott.