A Long Partnership
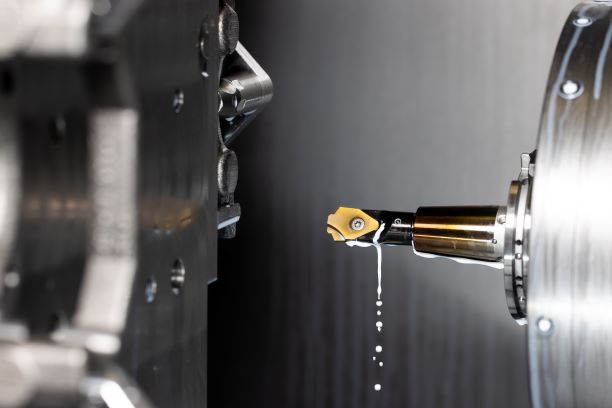
"Our quality pays off." This is the company motto of Knott GmbH from Eggstätt in Bavaria. The owner and managing director Valentin Knott and his employees live by this motto every day. For more than 40 years he has managed the company, which specialises in development and production in the field of brake and trailer technology. "Shortly after I started here at the company, I began my partnership with Paul Horn GmbH as a tool supplier," says Knott. Since then, numerous systems from the Tübingen-based tool specialist have been used in his production. Knott is always open to new tool and machine technologies. "We are constantly looking for new solutions to make our processes even more productive," says Andreas Neubauer, head of mechanical production.
"My father founded the company in 1937 and since then we have developed from a supplier of gearboxes to a leading global manufacturer of brake and trailer products," says Knott. Quality is of major importance in the company. In addition to operating fully automated production cells, Knott also still uses hand craftsmanship. Currently, about 2,500 people work for Knott worldwide. In the field of brake technology, the company produces drum, disc, wet disc and electromagnetic brakes. The systems are found in vehicles used in the agricultural, construction and mining industries, the military and in industrial trucks. In trailer technology, Knott supplies the chassis, axles, add-on parts and additional accessories to its customers. They are used in caravans, horse trailers, boat trailers and classic transport trailers.
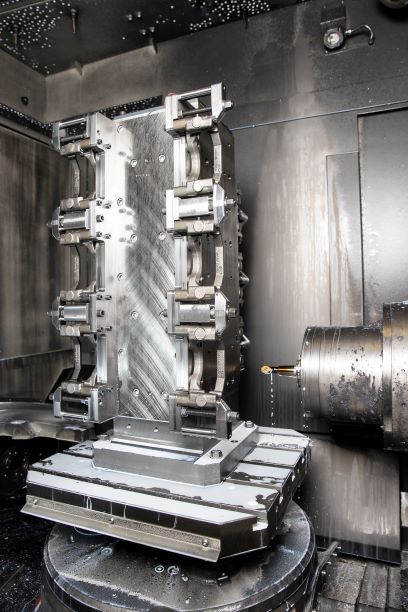
Optimisation potential
"Continuous improvement plays a key role in our production. Almost every day we strive to further optimise our manufacturing processes," says Neubauer. The machining of mounting holes on a brake carrier was one aspect of production that Neubauer wanted to improve. The carrier, made from nodular cast iron, is found in the braking systems of construction and agricultural machinery. Knott produces about 10,000 of this type of carrier per year. The bore with countersink and the chamfer/countersink were machined in three operations: pre-drilling, boring and countersinking. "We wanted to combine these three steps into one operation," says Neubauer.
With this requirement, the head of mechanical production turned to Michael Götze, the HORN sales representative responsible for Knott. He suggested producing the bore in one operation with the HORN D117 form drilling system. "In
addition to form turning operations, HORN's 117 insert system is well suited to form drilling," Götze explains. Once in possession of the profile of the bore to be produced, the Horn engineers in Tübingen set to work designing the appropriate tooling solution. The first tests at Knott were immediately successful and so Neubauer converted production of the brake carrier to the Horn solution. "The entire implementation took five to six weeks, including enquiry, technical consultancy, drawing approval, production and implementation in our production. We are very satisfied with this quick turnaround," Neubauer tells us.
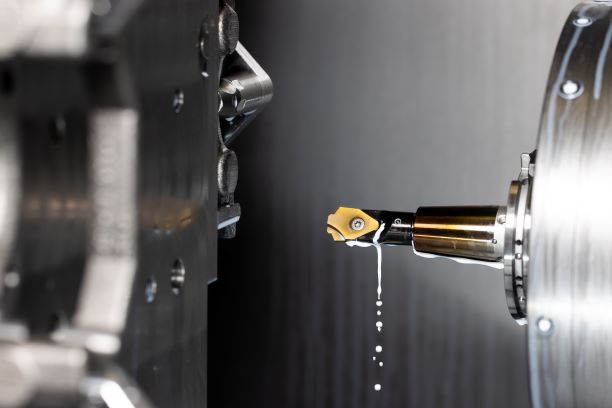
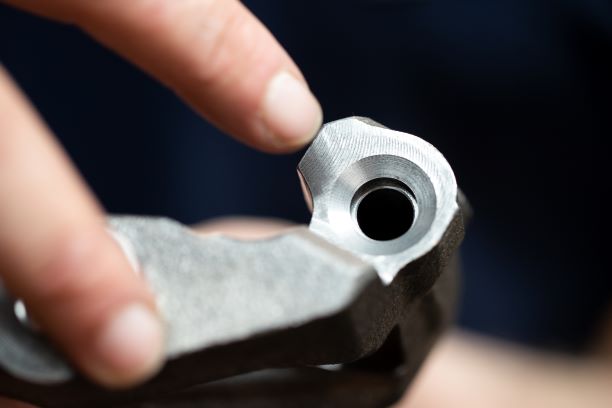
Considerable time saving
The D117 form tool drills the hole profile in one operation. The cutting speed is vc = 120 m/min (393.7 ft/min), with a feed rate of f = 0.25 mm/rev (0.010"/rev). In addition to the fewer tool changes on the machine, the cycle time was shortened by 30 seconds. With a quantity of 10,000 pieces, this results in an annual saving of around 83 hours. Furthermore, tool life increased compared to the tool systems previously used. "We cannot yet determine the exact tool life because the first insert is still in operation after 1,000 bores," says Neubauer. A Mazak FH 6800 is used for production. It is a horizontal, high-speed machining centre that, due to its design, has very high torsional rigidity for excellent machining accuracy in heavy-duty cutting.
The profile tools of the D117 drilling system enable economical advantages in series production as well as a reduction in tool costs for drilling across a large range of diameters. With the tool system, HORN produces the profiled inserts according to customer requirements for use on turning and milling centres. The precision ground insert seat of system 117 guarantees high concentricity and axial run-out accuracy as well as changeover accuracy in the micron range. The precision-ground cutting edges enable high manufacturing precision to tolerances down to 0.02 mm as well as excellent surface finish. Cost savings are generated by recoating only the insert, lower tooling costs and reduced machine downtime due to quick insert changeover. Cooling of the contact zone and efficient removal of the chips are ensured by the internal coolant supply through the round shank to both inserts.
The Knott factories mainly use machining centres from the Japanese machine manufacturer Mazak. "We have good contacts with Mazak in Japan," says Knott. Around 150 machining centres are installed at the various locations. In Eggstätt alone there are 50 Mazak machines. "We are convinced of their performance, precision and durability," says Knott. However, the manufacturer does not limit itself to just one machine tool supplier. Only recently, for example, a fully automated production cell from the Italian machine manufacturer Famar was put into operation in Eggstätt. "We use this cell for double-spindle machining of our brake calipers," says Neubauer.
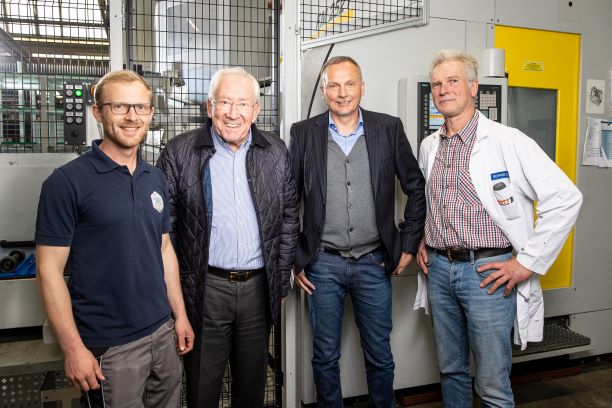
One of the longest standing Horn customers
After more than 40 years of cooperation, the Knott company is one of the longest-standing HORN customers. Numerous tool systems from HORN contribute to the high quality of Knott products. In addition to the new drilling tools, Knott relies on systems for grooving, milling and reaming from Paul Horn GmbH. "We are glad to have such a long-standing tooling partner at our side that supports us in our daily work and regularly provides us with new and even more productive tooling solutions," concludes Knott.