Fiabilité et économie des processus
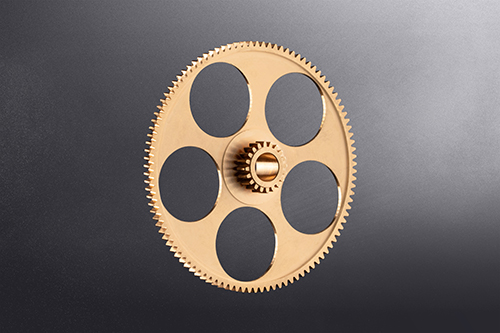
« En passant au taillage d'engrenages et en investissant dans un centre de tournage/fraisage d'INDEX, nous avons atteint une sécurité de processus maximale », déclare Erwin Wagner. Wagner est responsable de la planification des outils chez SAM GmbH à Bad Tölz. L'entreprise est considérée comme un spécialiste du développement et de la production de composants de haute qualité pour la construction aéronautique. Depuis près de 40 ans, SAM fait confiance aux outils de précision de Paul Horn GmbH pour l'usinage de composants difficiles. Outre les solutions d'outils pour le tournage de gorges, le tournage intérieur et le brochage d'engrenages, l'usine bavaroise s'est également lancée dans la production d'un procédé d'écroûtage d'engrenages.
SAM est reconnu dans l'industrie aérospatiale comme un spécialiste du développement et de la production d'actionneurs, ainsi que d'autres composants. Les actionneurs contrôlent les vannes utilisées pour la régulation de la température et dans les systèmes d'oxygène, d'air, de carburant et d'eau. SAM fabrique des actionneurs à simple et double effet ainsi que des actionneurs modulants. Les actionneurs à double motorisation sont utilisés, par exemple, pour fermer les vannes de débit de carburant lorsqu'une sécurité maximale est requise. Un élément central de chaque actionneur est un engrenage en alliage de bronze mesurant environ 60 mm de diamètre.
« Nous avons principalement externalisé la production de l'engrenage », explique M. Wagner. La demande pour ces composants délicats s'élève à plus de 20 000 pièces par an. « Afin d'accroître la flexibilité et l'indépendance des chaînes d'approvisionnement, nous avons décidé de produire les engrenages en interne », explique Herbert Krischkowski, responsable des projets spéciaux chez SAM. Pour produire l'engrenage extérieur avec un module de 0,5, le seul procédé disponible avec notre parc de machines existant était le brochage de l'engrenage avec une unité de façonnage. "Pour nos grandes quantités, ce processus n'aurait pas été aussi rapide que la production externe. D'une part, le temps de production aurait été trop long et, d'autre part, les coûts de maintenance d'une unité de façonnage auraient encore augmenté le coût des composants", explique M. Krischkowski. M. Wagner ajoute : "Les unités de poussée doivent être entretenues au moins tous les six mois en fonctionnement continu. On se situe ici dans une fourchette de coûts à quatre chiffres."
Investissement dans un nouveau centre de tournage/fraisage
SAM est toujours réceptif aux technologies nouvelles et plus économiques. C'est ainsi qu'il a été décidé d'investir dans un nouveau centre de tournage/fraisage pour produire les dents d'engrenage par le procédé d'écroûtage. « Nous n'avions pas de tour avec broche de fraisage dans notre usine », explique M. Wagner. Lors de la recherche d'une machine appropriée, deux candidats ont rapidement été retenus. "Nous avons opté pour l'INDEX G220. La flexibilité du centre de tournage-fraisage, les conseils et le service d'INDEX nous ont totalement convaincus", déclare Krischkowski. Les Bavarois ont acheté le cycle d'écrêtage et l'outil d'écrêtage avec la machine. La conception de l'outil a été réalisée par le département des équipements d'origine de HORN et Michael Götze, le représentant commercial responsable de SAM.
La décision d'investir dans une nouvelle machine équipée d'outils d'écrêtage HORN s'est rapidement révélée être la bonne. « Nous économisons maintenant plusieurs euros par composant en les produisant en interne », déclare M. Krischkowski. L'outil d'écrêtage n'est pas de conception monobloc, mais un système à tête remplaçable avec une interface de haute précision. Au cours du processus, les dents de l'engrenage sont produites avec quatre coups d'outil. Celles-ci sont divisées en trois courses d'ébauche et une course de finition avec une vitesse d'avance réduite. Le temps de cycle pour l'écroutage des engrenages est d'environ 20 secondes. Outre le temps de production réduit, les responsables ont été particulièrement impressionnés par la qualité des dents d'engrenage. "Nous avons fait valider nos résultats de mesure par un prestataire de services externe. Il a été stupéfait par la précision et a déclaré qu'il produisait normalement ses calibres maîtres à ce niveau de qualité", explique M. Wagner en plaisantant.
Le système d'engrenage HORN comprend des outils de forme cylindrique ou conique pour des modules de 0,5 à 2. La variante monobloc en carbure monobloc est disponible avec un diamètre allant jusqu'à 20 mm (0,787") et dans un design mince. Ils sont utilisés pour les petits modules et les petits composants, de préférence lorsqu'un arbre mince est nécessaire en raison du risque de collision. Les nuances et les revêtements adaptés à l'application permettent d'obtenir une qualité de surface élevée sur la pièce à usiner. Pour les diamètres d'outil supérieurs à 20 mm (0,787"), on utilise des outils d'écrêtage dotés d'un système de tête interchangeable. L'interface précise permet de changer facilement la tête de coupe dans la machine sans retirer le support. Le support en carbure garantit une rigidité, une résistance à l'usure et une précision élevées. Pour les modules plus importants, HORN mise sur l'utilisation d'un porte-outil avec des plaquettes indexables. En particulier avec le type d'outil WSR, HORN offre la possibilité de placer l'alimentation interne en liquide de refroidissement devant ou derrière la plaquette. Cela signifie que, selon l'application, des trous borgnes, des trous débouchants ou des trous étagés peuvent être usinés avec un refroidissement approprié.
Autres systèmes HORN utilisés
D'autres systèmes HORN sont utilisés pour l'engrenage en bronze. Par exemple, une plaquette de type S117 prend en charge le brochage des dents extérieures sur la face du composant. "Ici, l'utilisation de l'écroûtage n'était pas possible car le jeu nécessaire à l'extrémité des dents n'était pas présent. Nous avons donc opté pour le brochage de la denture à l'aide d'un outil spécial", explique Michael Götze, représentant de HORN sur le terrain. Dans ce processus, le diamètre de la pointe et la contre-dépouille à l'extrémité de l'engrenage sont pré-tournés. La contre-dépouille permet de dégager l'outil de brochage. La plaquette de brochage est rectifiée avec précision pour obtenir une forme spéciale et comporte deux dents. La première dent sert de pré-coupe et le profil de la deuxième dent est identique au profil nominal de l'engrenage requis. Lors de l'utilisation, l'outil broche une dent finie à la fois dans des mouvements axiaux avec une avance de 0,1 mm (0,004") par course. Ensuite, la broche principale s'indexe d'une dent et le processus de brochage recommence jusqu'à ce que toutes les dents de l'engrenage soient usinées. Le temps de production des dents d'engrenage est d'environ une minute.
SAM s'appuie également sur la gamme d'outils HORN pour les opérations de tournage complexes. Deux mini-outils différents sont utilisés pour produire l'engrenage. Le premier outil, d'une largeur de coupe d'un millimètre (0.039"), tourne la contre-dépouille sur les petites dents de l'engrenage. Le deuxième outil Mini tourne une rainure axiale sur le dos du composant. « La particularité de la rainure est la tolérance serrée sur seulement deux millimètres (0,079 »). L'outil doit offrir une grande précision et une grande fiabilité du processus", explique M. Wagner. Un outil Supermini est utilisé pour percer l'intérieur du trou central.
Les ingénieurs de SAM utilisent les solutions d'outillage HORN depuis près de 40 ans. « Le projet utilisant notre nouveau centre de tournage/fraisage a été une réussite totale. La mise en œuvre conjointe par INDEX et HORN nous a convaincus. Les solutions d'outillage HORN et le service toujours assuré nous ont une fois de plus démontré pourquoi nous faisons confiance aux outils de Tübingen depuis des décennies », déclare Wagner.