Process reliability and economy
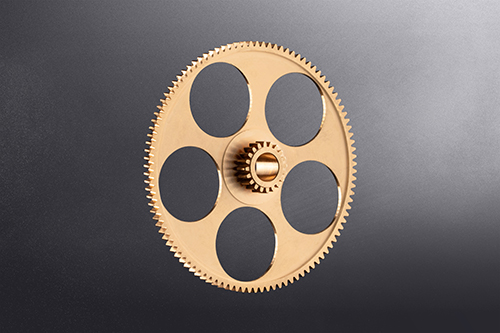
"By switching to gear skiving and investing in a turning/milling centre from INDEX, we have achieved maximum process reliability," says Erwin Wagner. Wagner is responsible for tool scheduling at SAM GmbH in Bad Tölz. The company is considered a specialist in the development and production of high-quality components for aircraft construction. For almost 40 years, SAM has relied on precision tools from Paul Horn GmbH for machining challenging components. In addition to tool solutions for groove turning, internal turning and gear broaching, the gear skiving process has now also found its way into production at the Bavarian factory.
SAM is recognised in the aerospace industry as a specialist in the development and production of actuators, as well as other components. The actuators control valves used for temperature regulation and in oxygen, air, fuel and water systems. SAM manufactures single- and double-acting as well as modulating actuators. The dual motorised actuators are used, for example, to shut off fuel flow valves where maximum fail-safety is required. A central component of each actuator is a bronze alloy gear measuring around 60 mm (2.362") in diameter.
"We mainly outsourced production of the gear," says Wagner. The demand for the delicate components is over 20,000 pieces per year. "In order to achieve greater flexibility and independence of supply chains, we decided to implement the production of the gears in-house," explains Herbert Krischkowski, the person responsible for special projects at SAM. To produce the external gear with a module of 0.5, the only process available with our existing machinery was gear broaching with a shaping unit. "For our large quantities, this process would not have been as expedient as external production. On one hand, the production time would have been too long and on the other, the maintenance costs of a shaping unit would have driven up the cost of the components even further," explains Krischkowski. Wagner adds: "The pusher units have to be serviced at least every six months during continuous operation. Here you are in the mid four-figure region in terms of cost."
Investment in new turning/milling centre
SAM is always receptive to new and more economical technologies. To this end, the decision was made to invest in a new turning/milling centre to produce the gear teeth using the gear skiving process. "We did not have a lathe with a milling spindle in our factory," says Wagner. In the search for a suitable machine, two candidates were quickly shortlisted. "We decided to choose the INDEX G220. The flexibility of the turning-milling centre, the advice and the service from INDEX completely convinced us," says Krischkowski. The Bavarians bought the skiving cycle and the skiving tool with the machine. The tool design was carried out by HORN's original equipment department and Michael Götze, the sales representative responsible for SAM.
The decision to invest in a new machine with HORN skiving tools quickly turned out to be the right one. "We now save several euros per component by producing them in-house," says Krischkowski. The skiving tool is not of monobloc design, but a replaceable head system with a high-precision interface. In the process, the gear teeth are produced with four tool strokes. These are divided into three roughing strokes and one finishing stroke with a reduced feed rate. The cycle time for gear skiving is around 20 seconds. In addition to the short production time, those responsible were particularly impressed by the quality of the gear teeth. "We had our measurement results validated by an external service provider. He was amazed at the precision and said that he normally produces his master gauges to that level of quality," Wagner explains, jokingly.
The HORN gear skiving system includes tools of cylindrical or conical shape for modules from 0.5 to 2. The solid carbide monobloc variant is available with a diameter of up to 20 mm (0.787") and in a slim design. They are used for small modules and small components, preferably when a slim shaft is required due to the risk of collision. The grades and coatings matched to the application produce high surface quality on the workpiece. For tool diameters over 20 mm (0.787"), skiving tools with an interchangeable head system are used. The precise interface allows the cutting head to be easily changed in the machine without removing the holder. The carbide holder ensures high rigidity, wear resistance and precision. For larger modules, HORN relies on the use of a tool holder with indexable inserts. Especially with the WSR tool type, HORN offers the option of placing the internal coolant supply in front of or behind the insert. This means that, depending on the application, blind holes, through holes or stepped holes can be machined with appropriate cooling.
Other HORN systems in use
Other HORN systems are used for the bronze gear. For example, an insert of type S117 takes over the broaching of external teeth on the face of the component. "Here, the use of gear skiving was not possible because the required clearance at the end of the teeth was absent. So we chose the gear broaching process using a special tool" explains HORN field representative Michael Götze. In the process, the tip diameter and the undercut at the end of the gear are pre-turned. The undercut provides clearance for the broaching tool. The broaching insert is precision-ground to a special shape and has two teeth. The first tooth serves as a pre-cutter and the profile of the second tooth is the same as the nominal profile of the required gear. In use, the tool broaches one finished tooth at a time in axial movements with an infeed of 0.1 mm (0.004") per stroke. Then the main spindle indexes by one tooth and the broaching process starts again until all the gear teeth are machined. The time to produce the gear teeth is about one minute.
SAM also relies on the HORN tool portfolio for complex turning operations. Two different Mini tools are used in producing the gear. The first tool, with a cutting width of one millimetre (0.039"), turns the undercut on the small gear teeth. The second Mini turns an axial groove on the back of the component. "A special feature of the groove is the tight tolerance fit across only two millimetres (0.079"). The tool has to provide high precision and process reliability," says Wagner. A Supermini tool is used for boring the inside of the central hole.
Engineers at SAM have been taking advantage of tool solutions from HORN for around 40 years. "The project using our new turning/milling centre was a complete success. The joint implementation by INDEX and HORN convinced us. The tool solutions from HORN and the service that is always provided have shown us again why we have been relying on tools from Tübingen for decades," says Wagner.