HORN Supermini: Interview mit Matthias Rommel
Matthias Rommel, geboren am 28. September 1969 in Mössingen, trat zum 1. November 2018 in die Paul Horn GmbH als Geschäftsführer für die Bereiche Produktion und Technik ein. Sein Maschinenbaustudium mit der Fachrichtung Fertigungstechnik absolvierte er in Stuttgart. Berufliche Erfahrung sammelte er über 25 Jahre lang in führenden und geschäftsführenden Positionen in der Werkzeugbranche. Vor dem Wechsel zu HORN leitete Rommel als verantwortlicher Geschäftsleiter die Sparte Lineartechnik eines deutschen Weltkonzerns.
Was waren die Ziele bei der Entwicklung des neuen HORN Superminis mit gesinterter Spanformgeometrie?
Das wichtigste Ziel war: Wie bekommt man wirtschaftlich das Thema Späne bei der Innenbearbeitung von langspanenden Werkstoffen in den Griff? Da hierfür ein bedeutender Anteil unserer Präzisionswerkzeuge zum Einsatz kommt, lautete ein weiteres Ziel, mit der Lösung unser Kernsortiment zu stärken. Die Lösung sollte als Standard verfügbar gemacht werden und mit den bestehenden Haltersystemen kompatibel sein. All diese Ziele haben wir erreicht.
Was genau waren bisher die Probleme?
Ein Problem bei langspanenden Werkstoffen war bisher die Bildung von Wirrspänen, die am Bauteil kritisch sind und den Werkzeughalter samt Schneidplatte umwickelt haben. Darüber hinaus bilden sich im Bauteil selbst unter Umständen Spänenester. Das bedeutet zusätzlichen Aufwand – in der Regel menschlichen Aufwand und einen nicht zu unterschätzenden Zeitverlust.
Wie sieht das neue Ergebnis aus?
Die gesinterte Spanformgeometrie im neuen Supermini sorgt neben einer sehr guten Spankontrolle je nach Werkstoff auch für einen kontrollierten Spanbruch sowie für kurze Späne. Auch die Kühlung wurde hierbei optimiert. Das Ergebnis beeindruckt mich jedes Mal aufs Neue: Keine Spänenester. Keine Wirrspäne. Keine Unterbrechung aufgrund umwickelter Werkzeughalter. Das spart wertvolle Zeit und reduziert unnötigen Aufwand wegen manueller Spanbeseitigung.
Wie aufwändig war die Entwicklung bis zum ersten funktionsfähigen Werkzeug?
Wir haben bereits vor einiger Zeit in die entsprechenden Technologien investiert, die uns zu diesem Meilenstein befähigt haben. Darüber hinaus ist es wichtig, auch über die notwendige Kompetenz zu verfügen. Trotz der richtigen Infrastruktur hat es mehr als vier Jahre gedauert, bis wir ein optimales Ergebnis erreichen konnten.
Was sind die Vorteile im Vergleich zu gelaserten Lösungen?
Aus Herstellersicht ist das Lasern von Spanformgeometrien relativ kostenintensiv und daher nur bedingt geeignet, um diese Werkzeuge in größeren Stückzahlen bereitzustellen. Daher findet diese Art vor allem ihren Einsatz bei Nischenanwendungen. Durch den neuen Supermini sind wir in der Lage, Werkzeuge für ein breites Anwendungsspektrum und in großer Stückzahl zur Verfügung zu stellen – und das Ganze wirtschaftlich.
Wie geht es weiter?
Aktuell bieten wir eine universelle Geometrie in drei unterschiedlichen Größen an. Weitere Geometrien und Abmessungen folgen in absehbaren Zeitabständen. Wir bauen unseren Technologievorsprung weiter aus und bieten unseren Kunden damit Lösungen, um einfach, unkompliziert und wirtschaftlich die Probleme am Shopfloor anzugehen.
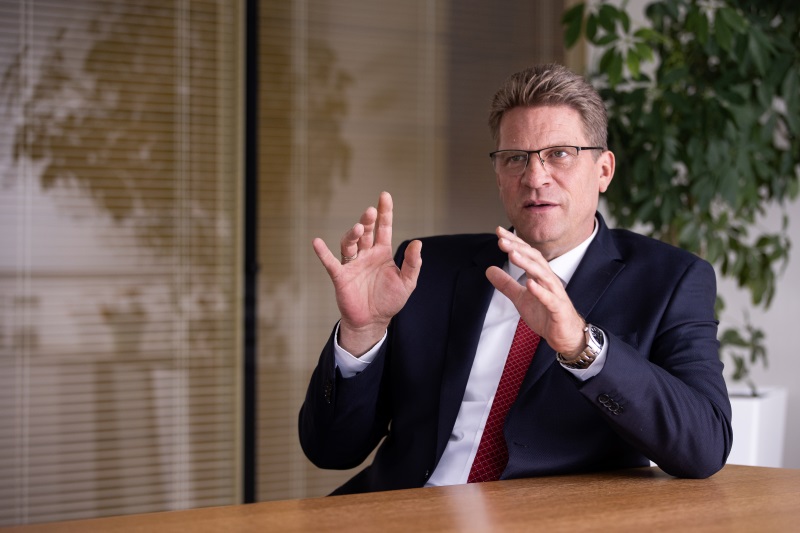