HORN Supermini: Interview with Matthias Rommel
Matthias Rommel, who was born on 28th September 1969 in Mössingen, joined Paul Horn GmbH on 1st November 2018 as Managing Director for Production and Technology. He completed his degree in mechanical engineering, specialising in production technology, in Stuttgart. He gained over 25 years of professional experience in leadership and executive positions in the tool industry. Before moving to HORN, Rommel was managing director of the linear technology division of a German global corporation.
What were the goals in the development of the new HORN Superminis with sintered chip breaking geometry?
The most important objective was: How can the issue of swarf generation during boring of long-chipping materials be brought under control economically? As a significant proportion of our precision tools are used for this purpose, another goal was to strengthen our core range with the solution, which had to be offered as standard and be compatible with existing tool holder systems. We have achieved all of these goals.
What exactly have been the problems so far?
One problem with long-chipping materials is the formation of tangled swarf, which can wrap around the component, tool holder and insert and risks damage. In addition, bird‘s nests can form inside the component itself. This means additional effort –
usually human effort and wasted time that should not be underestimated.
What does the new process look like?
The sintered chip breaking geometry of the new Supermini not only ensures very good chip control, depending on the material, but also controlled chip breakage and short chips. Cooling has also been optimised. The result impresses me every time: No bird‘s nests. No stringy swarf. No interruptions due to entangled tool holders. This saves valuable time and reduces unnecessary effort for manual swarf removal.
How time-consuming was the development of the first functional tool?
Some time ago, we invested in the relevant technologies that have enabled us to reach this milestone. It is also important to have the necessary expertise. Despite having the right infrastructure, it took us more than four years to achieve an optimal result.
What are the advantages compared to lasered solutions?
From the manufacturer‘s point of view, laser cutting of chip breaker geometries is relatively cost-intensive and therefore only suitable to a limited extent for providing tools in large quantities. This type of tool is therefore mainly used for niche applications. With the new Supermini, we are able to provide tools for a wide range of applications and in large quantities –
all economically.
What happens next?
We currently offer a universal geometry in three different sizes. Further geometries and dimensions will follow in the foreseeable future. We are continuing to extend our technological lead and offer our customers solutions to tackle problems on the shop floor in a simple and economical way.
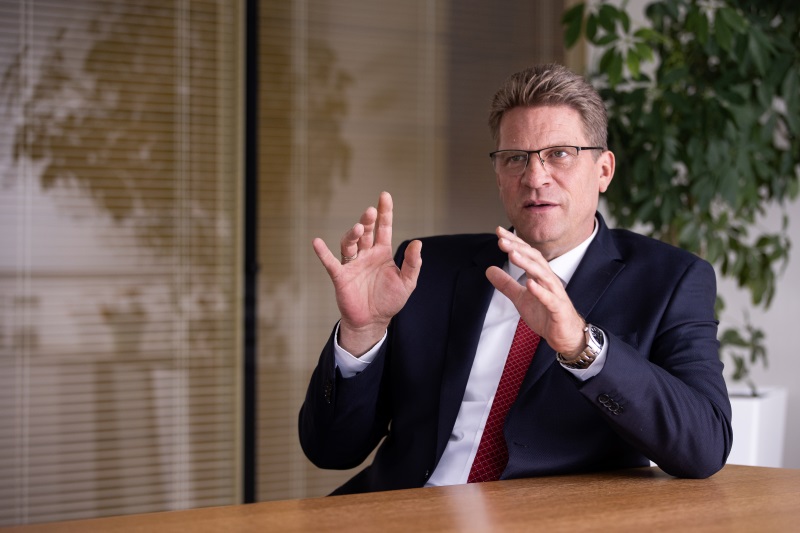