Seals for the global market
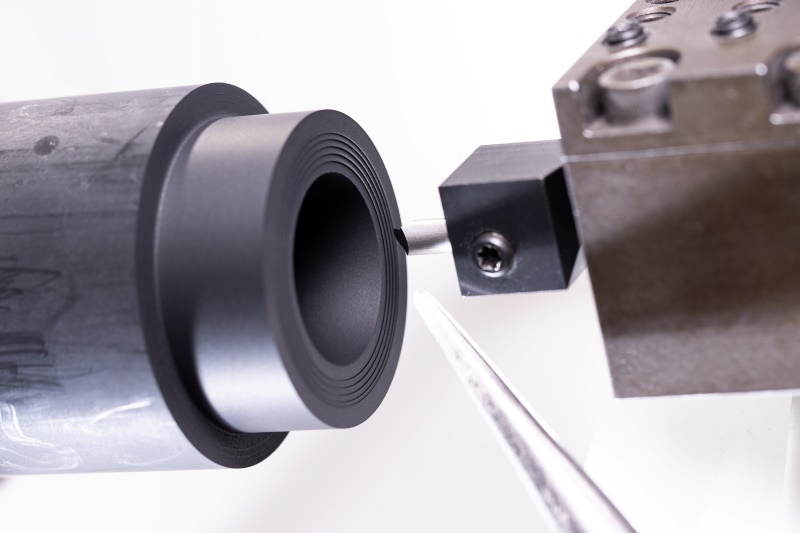
Hydraulics, gas and water. Seals are found wherever high pressures are involved or to prevent the tap at home from dripping. The inconspicuous parts are installed in a large number of devices. The Prädifa Technology Division of Parker Hannifin Corporation is a leader in the development and production of sealing solutions. The site in Boom, Belgium, specialises in seals made from machinable materials such as PTFE. The specialists rely on tool solutions from Paul Horn GmbH for machining. The Supermini and Mini systems are mainly used on the machine tools.
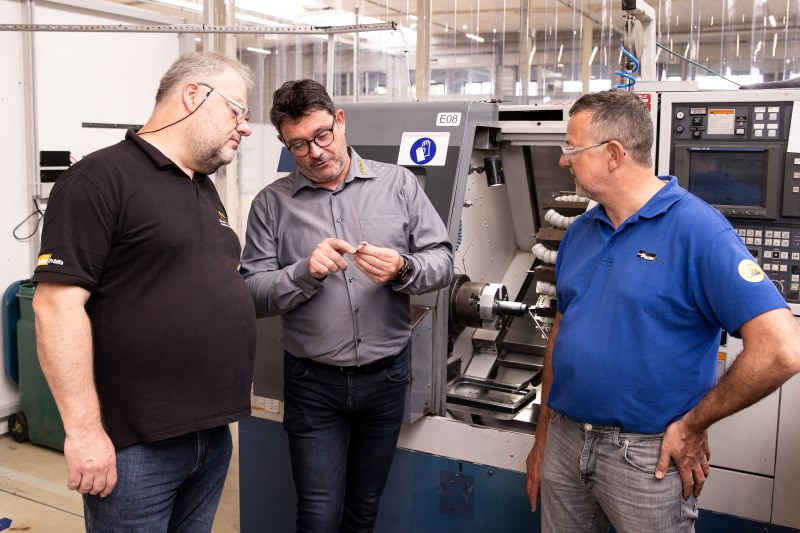
“Due to the variety of our different seals, we use special tools 90 per cent of the time. The materials and the different sealing profiles require very sharp tools with special cutting edge profiles,“ explains Peter Schockaert. He is responsible for production at Parker Prädifa, together with Johan Willems. “HORN‘s ability to design the cutting edge profiles according to our wishes and requirements is very important to us. That‘s why we‘ve been relying on the tools from Tübingen for years,“ says Willems.
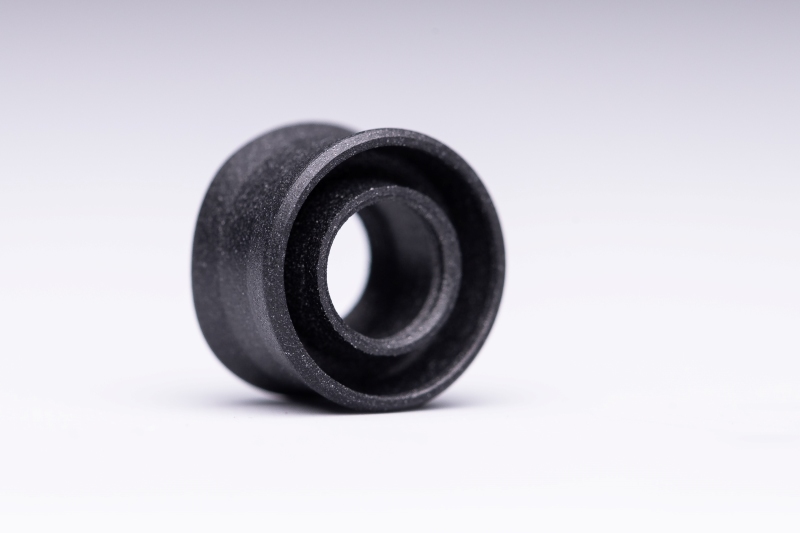
Leading supplier of polymer seals
The Parker Prädifa Technology Division‘s product portfolio includes a wide range of standard sealing elements and sealing systems, customised and application-specific seals and other technical components. Customers include companies from the aerospace, automotive, pharmaceutical, chemical, hydraulics and other industries. The company is recognised as a leading supplier of polymer sealing solutions made from a variety of sealing materials and in a wide range of sizes. This diversity also applies to the sizes of the seals, which range from a diameter of a few millimetres to the world record seal having a diameter of over four metres.
“We often just call the tools blades, as they are ground with a very sharp wedge angle,“ says Schockaert. Such a tool is used in the following application example. An axial thread has to be turned on a steering shaft seal made from a carbon fibre-Teflon material. The thread is needed to make the sealing ring axially flexible. This allows it to be slid over the shaft during subsequent assembly and remain securely attached after it is screwed on.
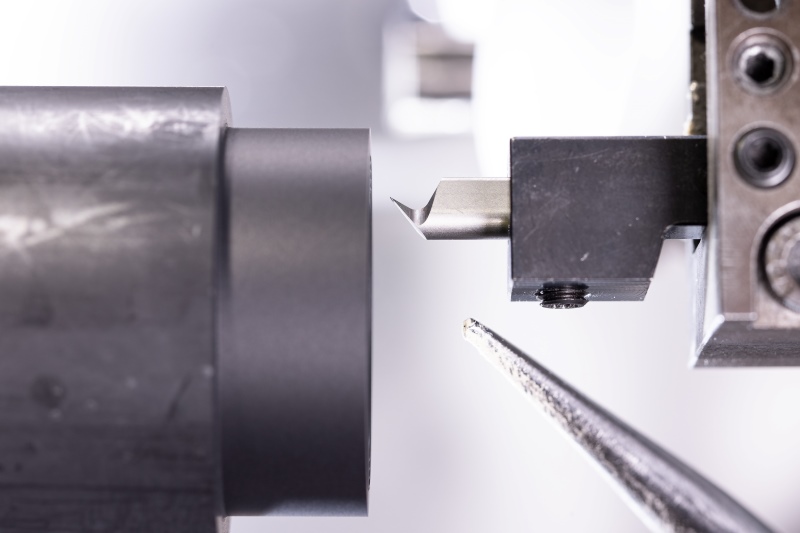
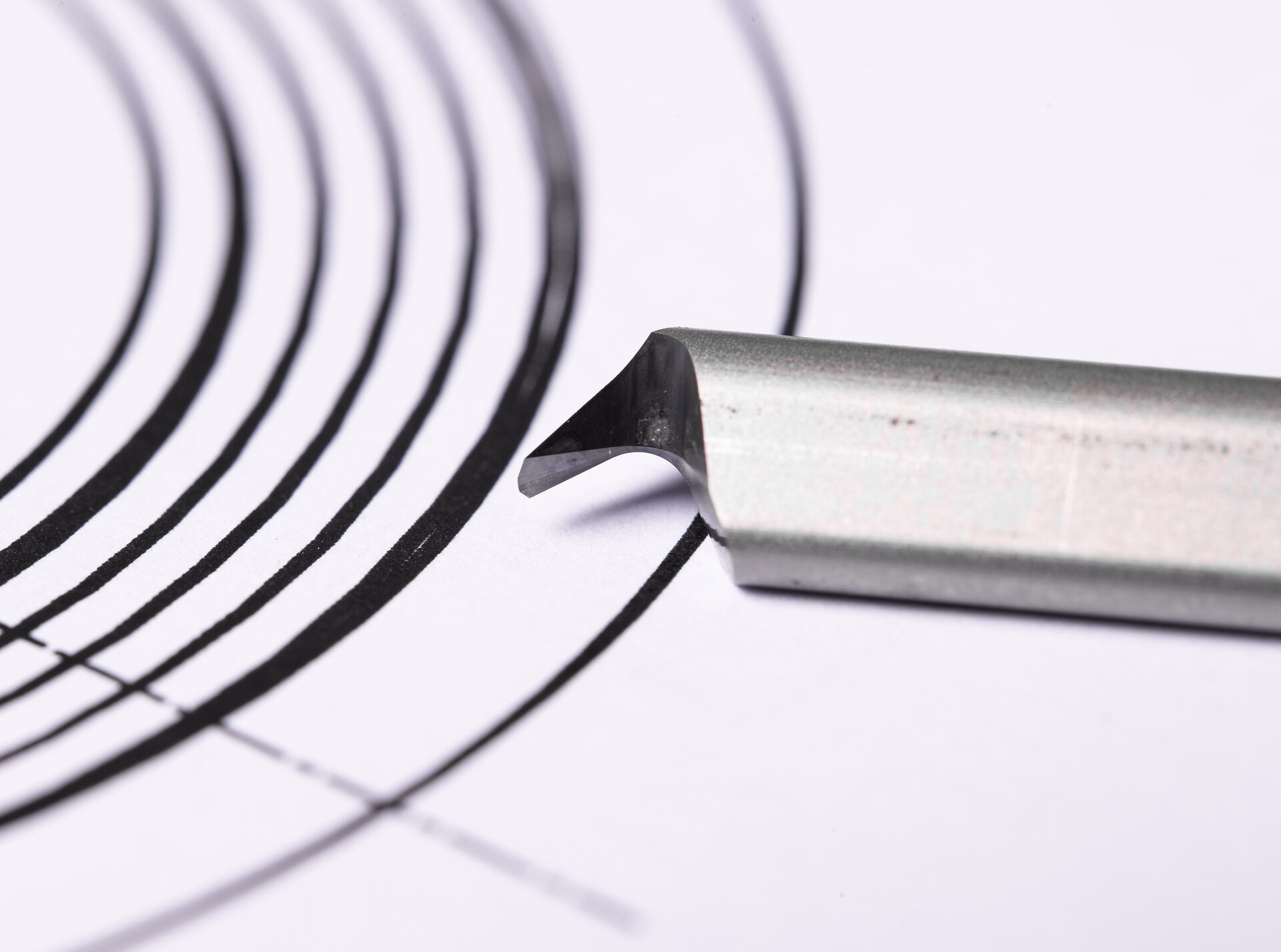
Razor-sharp blade
The first tests were carried out and orders fulfilled with tools that were ground in-house. “We grind prototypes and small quantities of tools ourselves. Then when volumes increase, we look for an appropriate tool solution,“ says Willems. In this case, HORN supplied a Supermini with a ground blade for axial machining. The thread to be produced has a depth of 0.2 mm (0.008“). The tool machines the thread at a high feed rate. “At first glance, the machining process looks very easy. But the required absence of burrs demands a very sharp cutting edge,“ says Schockaert. No chips flow during machining. The Supermini insert cuts or scores the thread into the surface.
Micromachining
The Supermini system is also used for producing another plastic seal having a diameter of just under 4 mm (0.157“). In addition to having a face groove, a hole of 1 mm (0.039“) diameter must be bored. “The sharpness of the tools is also very important in this application, as the walls are very thin and could warp if the cutting pressure is too high,“ says Willems. After axial grooving with a Supermini type 105, another Supermini of the same type is used to bore the pre-drilled hole to the tightly toleranced final dimension.
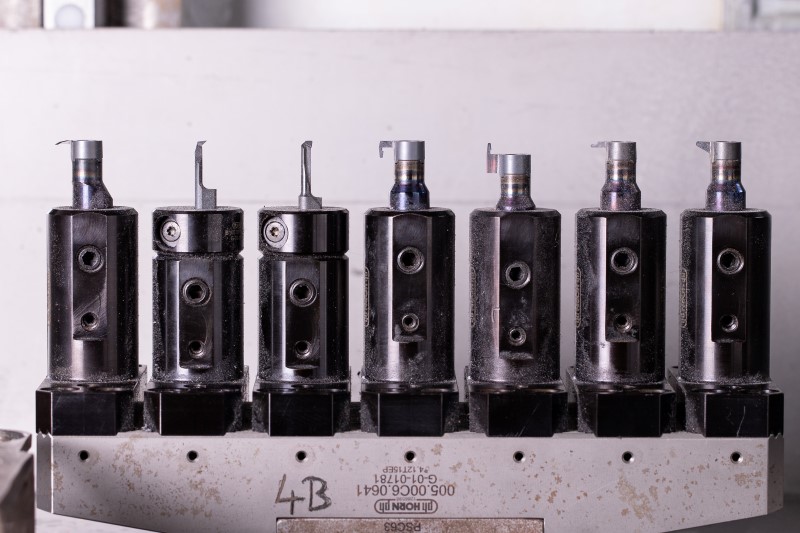
Mini system in use
Schockaert and Willems rely on special twin-spindle lathes that process two seals simultaneously to achieve high throughput. The spindles are mounted above the tools and the bar feeder for the raw material, which is loaded from above, is in line with a tool carrier. The turning process does not require any tool changes. The tools are permanently mounted in line under the spindles. During the process, the spindles move to each tool in turn until all machining operations have been completed.
The Mini system is used alongside Supermini tools. “The Mini system can be adapted very well to the respective machining operations,“ says HORN technician Kees van Bers. A tool is mounted on the platen for each operation. “With the large quantities involved, a very short cycle time was important to us. The tools allow us to carry out external copy turning, external grooving, face grooving on both sides, boring and parting off,“ explains Willems.
Parker has been working with tool solutions from HORN for about 10 years. Around 90 per cent of the tools used are special solutions designed specifically for the respective processes. “We are pleased to have HORN as a tool partner that fulfils our wishes and requirements precisely in terms of cutting-edge design,“ says Willems.