Brake pioneer
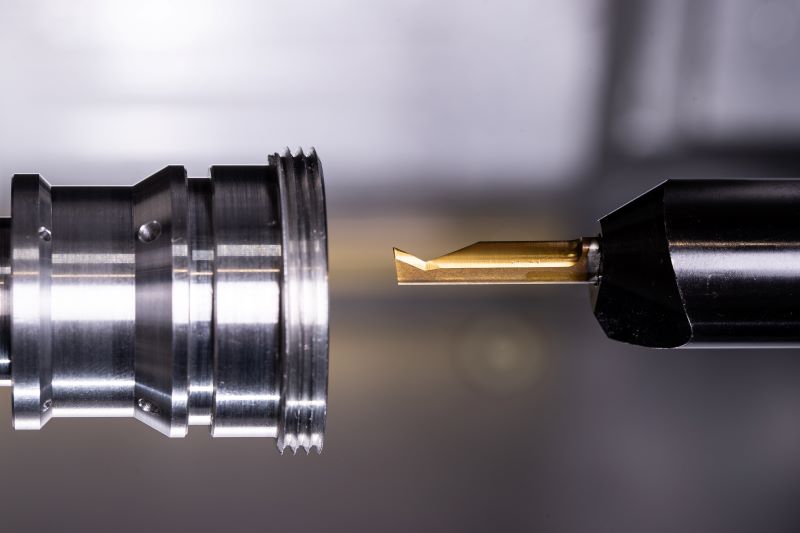
When Georg Knorr founded Knorr-Bremse GmbH in 1905, he had no idea that his pioneering spirit and ideas would lead the company to worldwide success. With over 33,000 employees worldwide, today Knorr-Bremse is the global market and technology leader for braking systems and a leading supplier of other systems for rail and commercial vehicles. In addition to research and development, the Group operates its own prototype production centre at its headquarters in Munich. Employees led by team leader Thomas Himmelsbach turn the engineers' ideas into reality. For many years, the specialists have relied on precision tools from Paul Horn GmbH to manufacture the components.
"We turn designers' ideas into functional parts and prototypes in steel and other materials. Each part has never been manufactured before. Sophisticated geometries and functions always require new solutions," explains Himmelsbach. The team not only produces prototypes in the workshop with its state-of-the-art machinery, but also focuses on the subsequent series production of components and assemblies. For example, the employees test new machining processes, develop manufacturing strategies and CNC programs and build fixtures developed in-house. The departments in Munich are close together: Research and Development is located next door. "The proximity enables us to quickly coordinate with each other. This means that problems and challenges can be discussed directly at the machine," says Himmelsbach.
From brake to windscreen wiper
In the Rail Vehicles division, Knorr-Bremse supplies systems for local and long-distance rail transport. In addition to advanced braking systems, these include intelligent boarding systems, air conditioning systems, power supply systems, control components, windscreen wipers, platform screen doors, friction materials, driver assistance systems and control technology. In 2022, the company generated a turnover of 3.4 billion euros manufacturing systems for rail vehicles and employs over 16,000 people worldwide.
Train brakes are basically a combination of several individual systems. At low speeds, conventional disc brakes with callipers decelerate the train. At higher speeds, magnetic rail braking is also used, whereby a magnetic field decelerates the train. "This brake is wear-free and is mainly used as a forced or emergency brake, as the maximum force is always applied," says Himmelsbach.
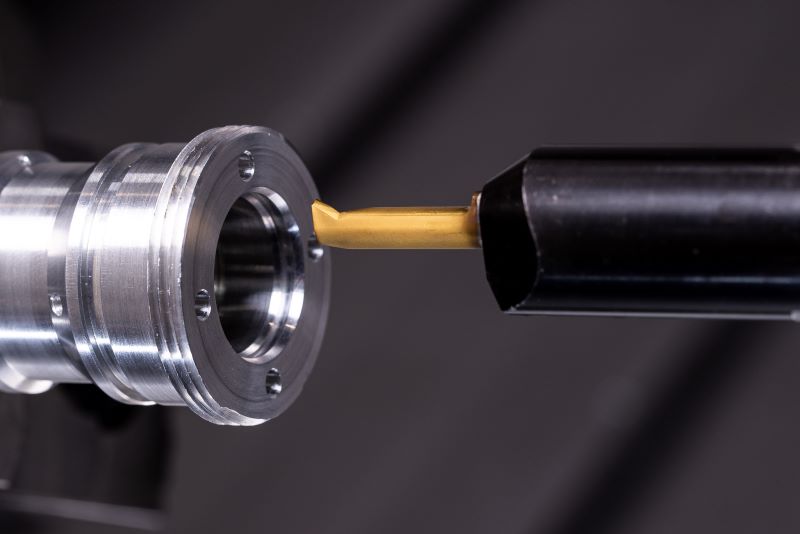
Horn Supermini in action
To minimise weight, numerous components of the brake systems are made of aluminium alloys. In one application for producing the prototype of a valve component, the team relied on System Supermini from Horn for turning. "The challenge when turning was the internal geometry. The tight tolerances and the surface quality called for a suitable production strategy," says Himmelsbach, who continues: "When turning this component, you need an insert that is precisely ground and cuts with low vibration." A special turned feature was a radiused groove on which a rubber ring sits that later acts as a seal. The 0.5 mm radius has a tolerance of +/- 0.05 mm and the required surface quality is Rmax 4. This feature is critical to the functioning of the valve component.
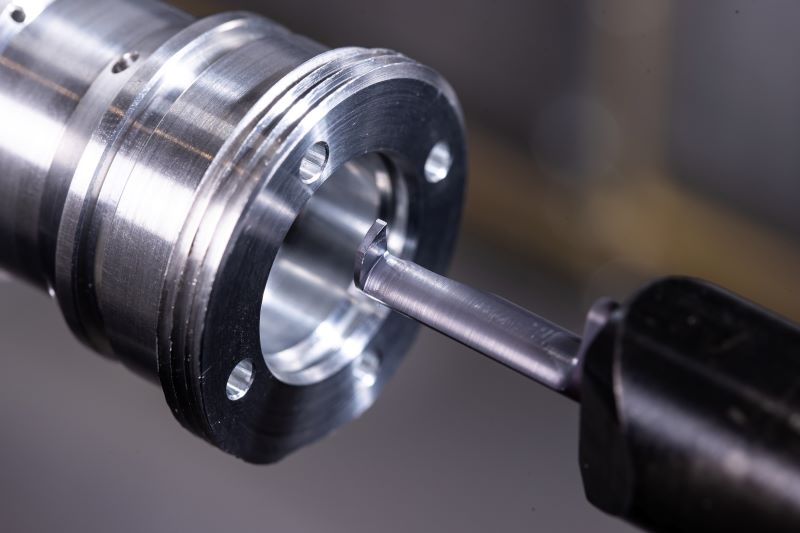
Impressive performance during turning
The Supermini tool was able to fulfil the required performance. "We really don't have any other tool that can turn such profiles so reliably. Even if we turn a single geometrical feature using several tools, they are so precise that there are no transitions," says Himmelsbach. To achieve the geometry, two different standard tools with a corner radius of 0.2 mm were used to turn the inner contour. A Supermini is also used for machining an internal, 2 mm wide groove for a retaining ring.
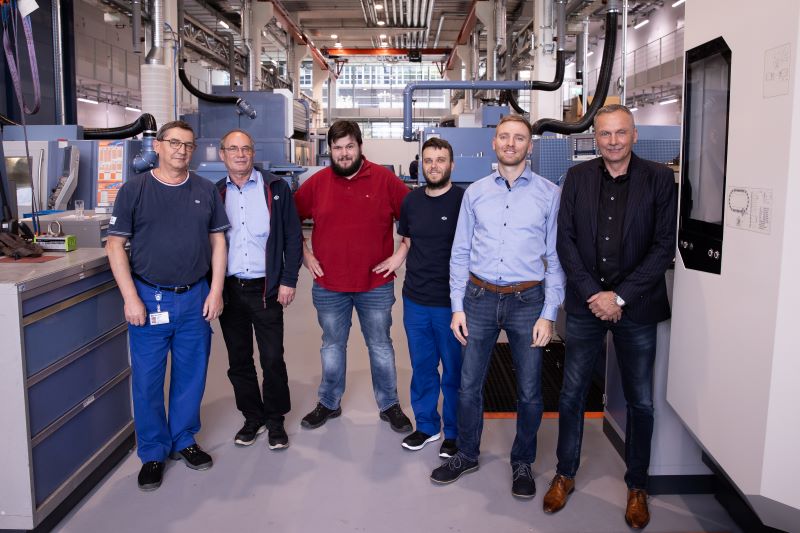
In addition to components for rail transport, Commercial Vehicle Systems is the second pillar of the Knorr-Bremse group. This division offers braking systems for trucks, buses, trailers and agricultural machinery. The company is recognised as a leader in the development and production of electronic brake control systems, driver assistance systems and air treatment systems. Thomas Himmelsbach's team also contributes to the development of new components in this area.
Across the entire workpiece programme, Horn tools are used in the development and test workshop for turning, milling and broaching. The full range offered in the Horn catalogue is used, from the Supermini to the 229 grooving system. "Horn offers us the complete range of tools for our requirements during testing, turning and milling. And since everything we design falls under the term "special" and most of it has to be produced for the first time, the most important thing is how experienced the technical advisor of our tool partner is," says Himmelsbach. For over 30 years, the Knorr-Bremse team has been supported by Horn's technical consultant, Michael Götze, who has in-depth tooling expertise.