Wirbeln für den guten Ton
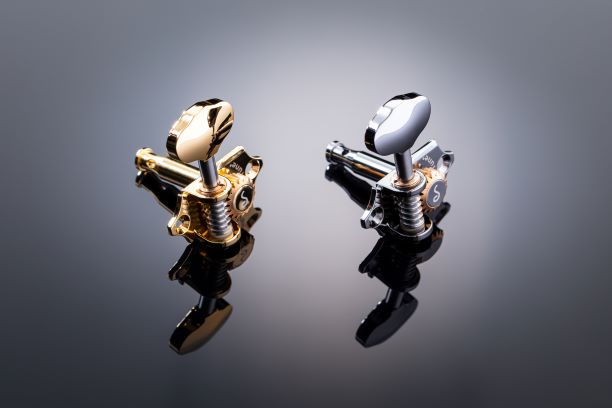
Musik macht Menschen glücklich und kann sie im nächsten Moment zum Weinen bringen. Sie kann Menschen beim Sport zu Höchstleistungen treiben, oder auch ängstlich machen. Eins tut die Musik nicht: Sie lässt einen niemals kalt. Kaum ein Instrument ruft so viele Emotionen hervor wie eine Gitarre. Egal ob am Lagerfeuer oder bei einem Rockkonzert in einem Stadion, die Funktionsweise der Gitarre ist gleich. Mit der Funktion des Zupfinstruments beschäftigt sich die Schaller GmbH aus der Nähe von Nürnberg schon seit über 75 Jahren. In dieser Zeit hat sich das Unternehmen zum Weltmarktführer von Gitarrenbauteilen entwickelt. Mit einem modernen Maschinenpark dreht und fräst das Team von Betriebsleiter Dominik Weininger die präzisen Bauteile, welche für den guten Ton sorgen. Dabei setzt er auch auf das innengekühlte Wirbelsystem der Tübinger Paul Horn GmbH.
Ein zentrales Teil der Mechanik ist das Schneckengewinde. Dieses Gewinde gab der Abteilungsleiterin der CNC- Dreh- & Frästechnik Nicole Gawatsch Potential zur Verbesserung. „Das Schneckengewinde haben wir mit einem Scheibenfräser gefräst. Die Bearbeitungszeit war uns hier zu lang. Wir mussten das Teil zu oft in die Hand nehmen und umspannen“, erzählt Gawatsch. „Wir sind auf der AMB 2018 auf das innengekühlte Jet-Wirbeln von Horn aufmerksam geworden und haben darauf gleich den für uns zuständigen Horn-Außendienstmitarbeiter kontaktiert“, führt der Betriebsleiter Weininger fort. Darauf folgten die ersten Gespräche mit Horn über das neue Wirbelsystem und der Start in die Projektphase.
„Die Wirbeleinheit läuft seit über einem Jahr 24/7 in der Maschine. Wir sind sehr zufrieden mit dem Werkzeugsystem“, so der Betriebsleiter Weininger. Die erfolgreiche Umstellung des Prozesses zeigt sich auch in der Bearbeitungszeit. Für das Fräsen des Schneckengewindes benötigte Gawatsch rund eine Minute. Das konventionelle Wirbeln dauerte 40 Sekunden. „Mit dem innengekühlten Wirbeln haben wir die Bearbeitungszeit nochmal auf nur noch 20 Sekunden pro Bauteil halbiert. Bei der sehr hohen Anzahl von Bauteilen im Jahr ist dies eine enorme Einsparung“, erzählt Gawatsch. Neben der reduzierten Bearbeitungszeit verbesserte sich die Oberflächengüte der gefertigten Bauteile nochmals deutlich. Darüber hinaus erhöhte sich die Standzeit der Wendeschneidplatten um ein Vielfaches.