Emotionen und Handwerkskunst
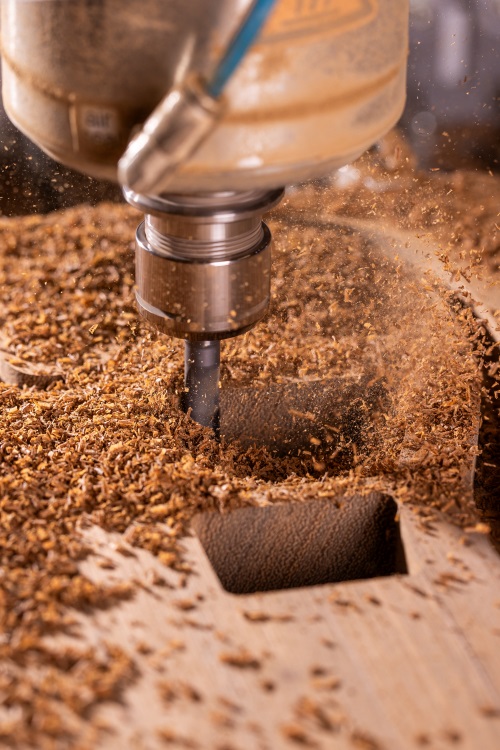
Rock 'n' Roll, Blues und Heavy Metal. Kein anderes Instrument weckt in der breiten Masse so viele Emotionen wie eine E-Gitarre. Das Instrument spielt eine zentrale Rolle in den meisten Musikgenres und prägt seit den 1930er Jahren Generationen von Musikern. Neben der Massenware gibt es für den Gitarrenbau kleine Handwerksbetriebe, die den Bau einer E-Gitarre bis ins kleinste Detail perfektionieren. Einen davon führt Marc Locher. Mit seinem Unternehmen EBG-Instruments geht er neue Wege, hält aber auch an alten Traditionen fest. Für ein aktuelles Projekt, eine Telecaster, kommen 3D-Druckteile aus Titan sowie CVD-Diamantfräser zum Einsatz. Hierzu bekam Locher die Unterstützung der Paul Horn GmbH.
Böse Zungen behaupten, eine E-Gitarre kann jeder mit einer Säge, einem Schraubenzieher und einem Lötkolben bauen. In der Theorie stimmt das, aber hören möchte dies sicher keiner. Denn im Gegensatz zu einer Akustikgitarre haben die meisten klassischen E-Gitarren keinen hohlen Resonanzkörper, um den Ton der Saiten zu verstärken. Teilweise gibt es auch E-Gitarren, die einen hohlen Körper (Body) besitzen. Der Ton wird jedoch bei einer klassischen E-Gitarre in der Regel durch die Bauform, die Holzauswahl, die Hardware, die Pickups sowie die Verarbeitungsqualität beeinflusst. Pickups sind magnetische Spulen, die die Schwingung der einzelnen Saiten in elektrische Signale umwandeln. Diese Signale durchlaufen beim Spielen die Effektgeräte und werden dann im Gitarrenverstärker verstärkt und als Ton über den Lautsprecher ausgegeben. Die Spieltechnik, die Verstärker und die Effektgeräte erzeugen dann den gewünschten und bekannten E-Gitarren-Sound.
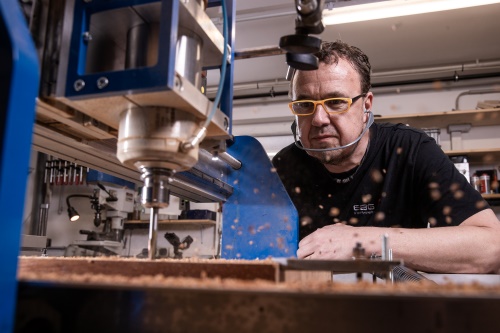
Handwerkskunst
Locher zeigt mit seinen Instrumenten eindrucksvoll, wie man die traditionelle Handwerkskunst des Gitarrenbaus mit neuen Ideen und Technologien verbindet. Hierzu kombiniert er beispielsweise CNC-gefräste Aluminium-Bodys mit edlen Hölzern und Carbon-Gitarrenhälsen. Er baut rund sechs E-Gitarren oder E-Bässe pro Jahr. Alle Instrumente entstehen nach Wünschen und Anforderungen der Kunden. Im Alltag arbeitet Locher als Berufsschullehrer für den Bereich CNC-Technik. In seiner Freizeit steht er in seinem Keller und arbeitet an seinen Instrumenten. Sein Gitarrenbau-Reich hat er im heimischen Keller geschaffen mit allem, was das Technik-Herz begehrt. In zwei Räumen ist die Gitarrenwerkstatt inklusive CNC-Fräsmaschine, zahlreichen Holzbearbeitungsmaschinen, Lackierkabine sowie einen Arbeitsplatz für die Endmontage untergebracht. Des Weiteren beherbergt sein Keller mit dem Tonholzlager auch eine kleine Schatzkammer. Hier lagern schöne und seltene Tonhölzer wie beispielsweise zertifiziertes Ebenholz, Riegelahorn und Mahagonihölzer.
„Ich bin immer auf der Suche nach alten Holztreppen aus den 50er und 60er Jahren. In dieser Zeit baute man Treppen oft aus massivem Mahagoni“, erzählt Locher. Aus den alten Treppenstufen fertigt Locher die Bodys sowie Gitarrenhälse. „Das Holz ist für den Bau einer Gitarre sehr gut geeignet, da es durch das Alter und die trockenen Gegebenheiten in den Häusern auch relativ spannungsfrei ist“, erklärt Locher. Auch für sein aktuelles Projekt, eine Telecaster, nutzt er dieses wertvolle Holz. Die Telecaster-Form ist eine der beliebtesten E-Gitarren-Formen überhaupt. Entwickelt wurde diese von dem weltweit bekannten Gitarrenbauer Leo Fender. Die Telecaster von Locher ist jedoch keine einfache Kopie der Gitarre von Fender. Mit besonderen Werkstoffen und Bauteilen sowie einem „cleanen Look“ mit vielen versteckten Verschraubungen auf der Gitarrenvorderseite ist sie ein Unikat, in dem viel Zeit, Arbeit und Handwerkskunst sowie besondere Fertigungstechnologien stecken.
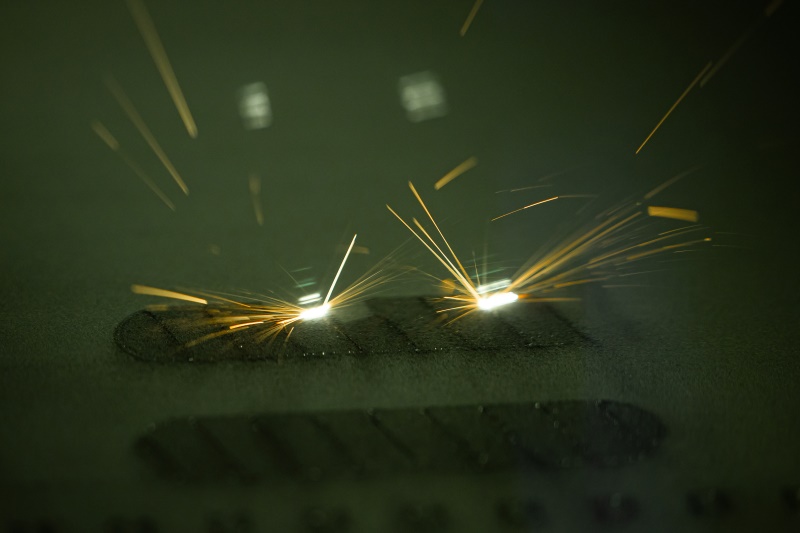
3D-Metalldruck
„Zum Bau außergewöhnlicher Instrumente gehört auch die Verwendung besonderer Werkstoffe“, so Locher. Deshalb entschied er sich für den Einsatz von Titanbauteilen. Dazu zählt auch der Steg, mitunter Brücke genannt. Das Bauteil ist auf den Body der Gitarre montiert und hält die Saiten an ihrem unteren Ende fest. Zudem ist die Brücke ein sehr wichtiges Bauteil an der Gitarre, da sie großen Einfluss auf das Attack (Geschwindigkeit der Tonentfaltung) und das Sustain (Dauer des Tones) hat. Mit dem selbst konstruierten 3D-Modell ging Locher dann auf die 3D-Druck Spezialisten von Horn zu, um diese Teile aus Titan drucken zu lassen. Aufgrund der Bauteilgeometrie und den dünnen Wandungen kam die Fräsbearbeitung der Teile aus Zeit- und Kostengründen nicht infrage.
Locher hatte Glück: Horn hatte schon im Frühjahr 2018 mit dem Projekt additive Fertigung losgelegt. Heute ist daraus ein eigener Fertigungsbereich entstanden. Horn nutzt die additive Fertigung bei der eigenen Werkzeugherstellung, insbesondere bei der Herstellung von Prototypen, Sonder- und Trägerwerkzeugen sowie beim Optimieren von Kühlmittelaufsätzen. Die erweiterten Möglichkeiten, welche sich durch die additive Fertigung ergeben, stellt Horn Kunden und Partnern wie Locher zur Verfügung. Die additive Fertigung ist sinnvoll, wenn sich dadurch ein technologischer Vorteil ergibt. Ein bisher konventionell gefertigtes Bauteil additiv zu fertigen, ergibt allerdings wirtschaftlich in vielen Fällen keinen Vorteil. Das gilt beispielsweise für Drehteile, die auf Langdrehautomaten schnell herzustellen sind. Die additive Fertigung wäre auch im Hinblick auf eine spanende Nacharbeit zu teuer.
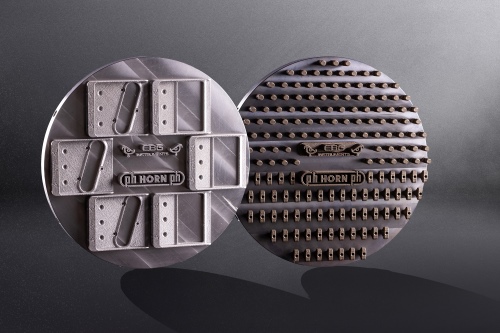
SLM-Verfahren
Bei Projekten wie Lochers E-Gitarren kommt bei Horn das Selective-Laser-Melting-Verfahren zum Einsatz, auch Pulverbettverfahren genannt. Bei diesem Verfahren wird das Metallpulver in Schichten auf eine absenkbare Plattform aufgetragen und danach im relevanten Bereich durch den Laser belichtet und aufgeschmolzen. Dies wird so lange wiederholt, bis die Bauteilhöhe erreicht ist. Horn setzt auf die Werkstoffe Aluminium (AlSi10Mg), Edelstahl (1.4404), Werkzeugstahl (1.2709) und Titan. Weitere Werkstoffe befinden sich in der Erprobung. Die Bauraumgröße beträgt im Durchmesser 300 mm und in der Höhe 400 mm. Da Horn alle Fertigungsschritte im Haus hat, können die Spezialisten des Fertigungsbereiches direkt auf die Kundenanforderungen eingehen. Die Herstellung der Teile erfolgt je nach Kundenwunsch in verschiedenen Ausführungsformen. Horn unterstützt dabei den Kunden auch bei der Konstruktion und der Auswahl geeigneter pulverbasierter Parameter. Die Herstellung erfolgt nach Kundenanforderung als Rohteile oder bis hin zum fertig bearbeiteten Bauteil. Weitere Vorteile sind bei Horns Inhouse-Produktion der vorhandene Maschinenpark und die entsprechenden Messmittel. Dies erspart Zeit und hat direkten Einfluss auf alle Fertigungsprozesse.
Das Trennen der gedruckten Gitarrenbauteile von der Trägerplatte geschieht durch das Drahterodieren. Aufgrund der hohen Spannungen der dünnwandigen Bauteile verlangen diese jedoch vor dem Erodieren eine Wärmebehandlung, da sie sich nach dem Trennen sonst verziehen würden. Die Wärmebehandlung geschieht bei einer Temperatur von 650 Grad Celsius und einer Zeit von rund zwei Stunden. Für das optische Finish der Bauteile entschied sich Locher für das Glasperlenstrahlen. Neben der Brücke druckte Horn für Locher auch noch weitere Bauteile für die Telecaster.
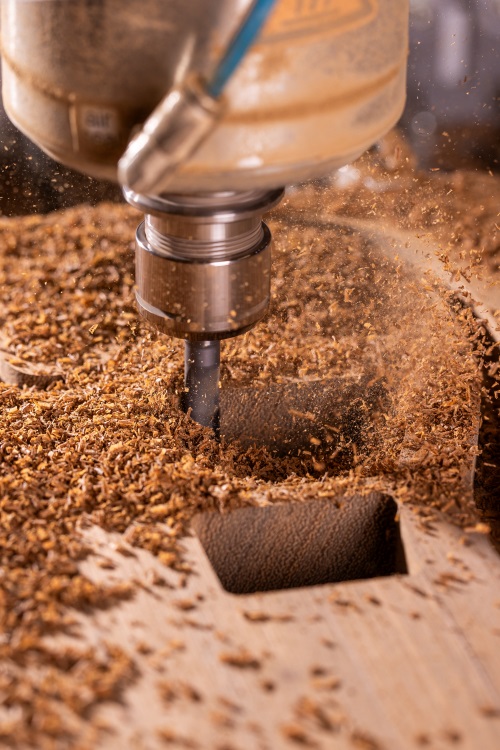
CVD-Diamantfräser
Den Gitarrenbody fräst Locher aus dem Vollen. Das Rohteil stammt aus einer Mahagoni-Treppenstufe. Diese trennt Locher längs auf und verleimt die beiden Teile spiegelbildlich. „Neben der höheren Stabilität ist das spiegelbildliche Verleimen bei manchen Hölzern auch ein optischer Faktor im Gitarrenbau“, sagt Locher. Beim Verleimen kommt spezieller Instrumentenleim zum Einsatz, der nahezu glashart aushärtet. Dies ist sehr wichtig, da „weiche“ Leimverbindungen den Ton schlucken und somit den späteren Klang des Instrumentes beeinflussen. Beim Fräsen des Bodys setzt Locher auf eine dreiachsige CNC-Fräsmaschine mit Hochgeschwindigkeitsspindel und einen vierschneidigen diamantbestückten Fräser von Horn.
Die Schneidenlänge des Werkzeugs beträgt rund 45 mm. Dies ist genug, um die meisten Fräsoperationen des Bodys zu übernehmen. Durch die hohe Schneidenschärfe des Fräsers spart Locher bei den späteren Schleifarbeiten Zeit. „Die gefrästen Oberflächen haben mich extrem beeindruckt. Die Flanken sind wie feinstgeschliffen und an den Kanten entsteht kein Grat. Das spart Zeit beim späteren Schleifen der Oberflächen“, erklärt Locher. Auch das Fräsen von Taschen ins Volle übernimmt das Werkzeug problemlos durch das Eintauchen in eine Rampe. So fräst Locher in den Body zahlreiche sechseckige Taschen sowie das E-Fach in den Body, um das Gewicht zu reduzieren. Die Taschen und alle gefrästen Kabelkanäle und Funktionstaschen überleimt Locher später mit einer 5 mm starken Decke aus Mahagoni.
Lack wie Glas
Der Gitarrenbau auf diesem hohen Niveau vereint zahlreiche Berufe. Neben den mechanischen Tätigkeiten in der CNC-Technik benötigt man die Fähigkeiten eines Schreiners, Kunsthandwerkers und Lackierers. Nach der Fertigung der einzelnen Gitarrenkomponenten sowie den feinen Schleifarbeiten geht es an das Lackieren der Teile. Für den Body der Gitarre hat sich Locher für ein Perlmuttweiß-Metallic entschieden. Der Gitarrenhals aus Riegelahorn und Ebenholz bekommt nur eine dunkelbraune Beize und Klarlack, damit die schöne Holzmaserung sichtbar bleibt. „Mit der Grundierung, dem Farblack sowie dem Klarlack kommen wir auf neun hauchdünne Lackschichten“, so Locher. Jede einzelne Schicht wird nach dem Trocknen geschliffen und für die nächste Schicht vorbereitet. Beim Lackieren entsteht immer eine sogenannte Orangenhaut. Diese zeigt sich durch ein leicht welliges Oberflächenbild. Die letzten Schichten Klarlack bekommen deshalb eine besondere Behandlung. Sie werden nach dem Trocknen mit immer feineren Körnungen geschliffen und anschließend mit unterschiedlichen Compounds auf Hochglanz poliert. „Nach diesen zeitaufwändigen Arbeitsschritten spiegelt der Klarlack wie eine Glasschicht“, sagt Locher. Die Endmontage und das Einziehen und Stimmen der Saiten ist immer ein besonderer Moment für Locher. „Mit dem ersten Ton des fertigen Instruments beginnt auch schon der Abschied. Das fällt mir oft schwer, da ich zwei bis vier Monate daran gebaut habe“, erzählt Locher. So liefert er seine Gitarren europaweit oft auch persönlich an die neuen Besitzer aus.
Die Zusammenarbeit mit Horn bewertet Locher positiv: „Von der ersten Idee, die Bauteile aus Titan zu drucken, über die technische konstruktive und zielorientierte Beratung sowie die Umsetzung verlief die Zusammenarbeit sehr professionell und reibungslos. Ich freue mich schon auf die nächsten Projekte. Vielen Dank dafür.“