High quality diamonds for a brilliant result
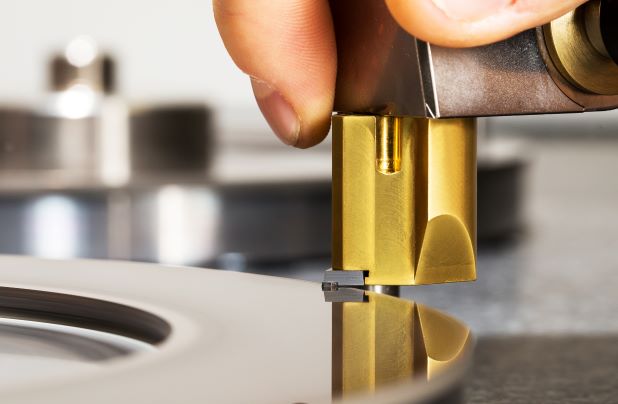
“We branched out into the sectors that others had avoided”, says company founder Walter Schumacher. Together with his son, Stefan, he runs the company Walter Schumacher Impuls Technik GmbH, (SIT). The company specialises in the development and production of special valves and stand-alone valve solutions, which are used in numerous industries. The product range includes valves for all types of media, ranging from high-vacuum valves to high-pressure valves rated up to 800 bar. One of these special solutions made from aluminium consists of several helium valves, various sensors, pressure relief valves and throttles, which control and regulate various pressures. The emphasis is on the surface quality of the mating surfaces, which ensures functionality in high-technology analysis. SIT achieves a surface quality of Ra 0.012 µm (4.724409e-7") using a diamond tool from Paul Horn GmbH and by having invested in a new turning/milling centre from the machine manufacturer Mazak.
“After initial contact was made and the machining task had been outlined, it quickly became clear to me that the finishing processing should be performed using our DTM milling system”, says Horn product manager Jürgen Schmid. The tool is tipped with a monocrystalline diamond (MCD) cutting edge. The second cutting edge is tipped with PCD and is used as a pre-cutter to achieve the defined allowance of 0.02 mm (0.001") for the MCD. “As well as Horn, an alternative tool manufacturer was also in the running. However, Horn solved the task on the first attempt, while the other manufacturer needed three attempts. This made our choice clear, not only because we were immediately satisfied with the result, but also because of how impressed we were by the company’s expertise. We also use other tool systems from Tübingen and are very satisfied with them”, says Walter Schumacher.
Delicate surfaces
“One difficulty was the large number of holes drilled into the surface to be machined. Necessarily, brilliant-finish milling must be the final machining operation, as otherwise very fine chips from drilling, reaming and thread milling would damage the reflective mirror surface”, explains Schmid. “Even fingerprints can render the sealing surface unusable later on”, adds Stefan Schumacher. The interrupted cut across the drilled holes posed no problem for the Horn tool. During processing, the milling cutter moves once longitudinally over the workpiece at a speed n = 5,000 rpm and with a feed rate of vf = 500 mm/min (19.685"/min). The cutting speed is vc = 1,960 m/min (6430.446 ft/min). To reduce re-cutting of the chips, the tool is set at a minimum lead angle of 0.008 degree. A commercially available emulsion is used for the coolant. “We are very satisfied with the performance of the tool. In series production, we now achieve surface qualities between Ra 0.012 (4.724409e-7") and Ra 0.014 µm (5.511811e-7")”, summarises Stefan Schumacher.