The inventor who pulls the strings
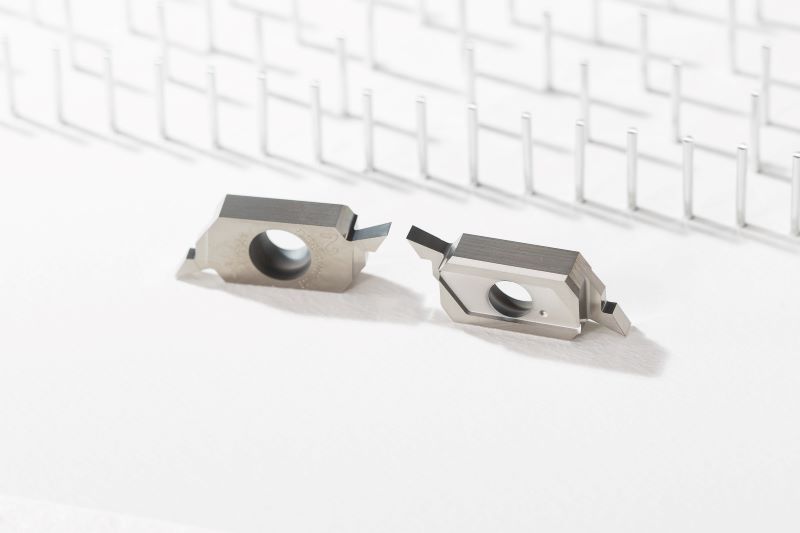
"We pull all the strings," jokes André Gall. The founder of WireStyle creates works of art with his team from thousands of nails and a kilometre-long thread using machines developed in-house. A photo or graphic serves as a template. The rest is done by his software and the machines - at breathtaking speed. Gall relies on precision tools from Tübingen-based Paul Horn GmbH to cut millions of nails before insertion. With the help of the S274 system, the nailing machine hammers up to 12 nails per second into a plastic sheet.
Almost everyone has a framed photo hanging on a wall in their home. A few years ago, if you wanted to convert a photo to a thread picture, you would turn to an artist. However, the process was so time-consuming and complicated that such pictures were hardly affordable. In addition, the delivery time for such works of art was long. "My neighbour at the time approached me and said that he wanted to give his girlfriend a thread painting. However, the effort was too great for him. So he wrote the software with which such pictures can be produced automatically," says Gall. André Gall studied physics at the University of Karlsruhe (KIT). In addition to physics, Gall has always had a great interest in mechanical engineering and production engineering. He personally built the first prototypes of the nail and thread machines and the Wirestyle company was born. In 2022, Gall presented his pictures on the well-known TV start-up show "Die Höhle der Löwen".
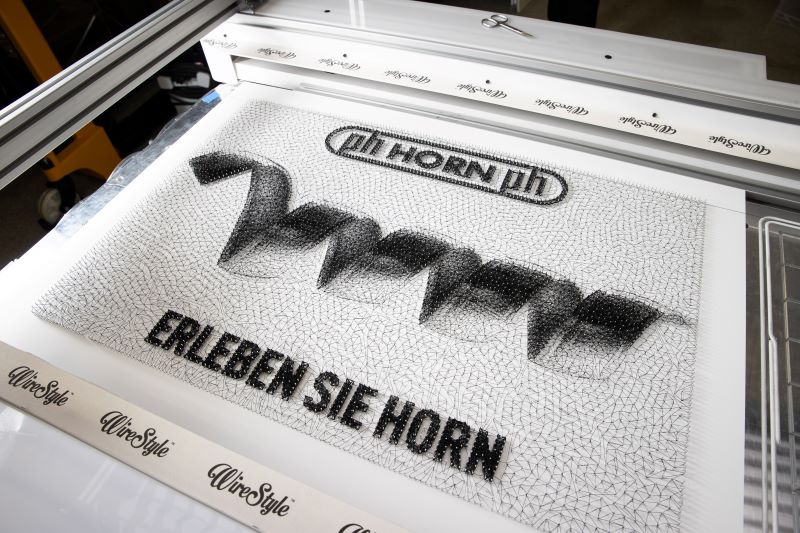
Fine details
Conventional images are printed with coloured pigments. In a thread picture, a long single thread creates the contrast in the picture. "Funnily enough, people who see a thread picture for the first time stop and look for the beginning of the thread, or the printed colour hidden behind the thread, which of course doesn't exist. This is understandable, because you could hardly reproduce such detail with a thread by hand as accurately as we do," explains Gall.
To determine the exact path of the thread, the Wirestyle team developed complex computer algorithms. The software identifies the contrasting edges in the original photo and enhances the contours. This means that the desired thread image can be reproduced better than could ever be achieved by hand. More thread is used in darker areas of the image than in lighter areas. The software calculates the individual nail pattern and the exact course of the thread path. On average, the nailing machine hammers around 8,000 nails into the polystyrene base plate per picture. The threading machine then stretches an average of around 1,200 metres of thread between the nails. Gall and his team built the machines themselves from scratch - they are the only ones of their kind worldwide.
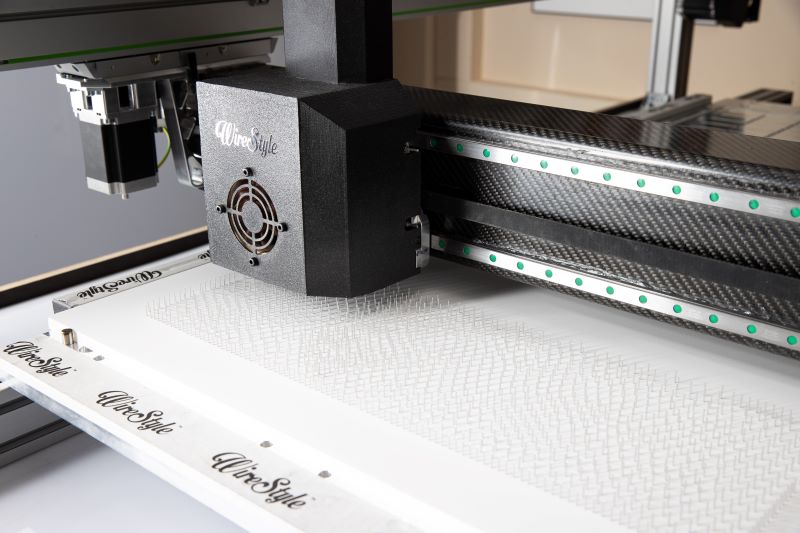
Breathtaking speeds
In order to make the thread painting affordable for customers, the machines have to produce the images at high speed and precision. Due to the high acceleration rates, Gall favoured lightweight construction from the outset and used a lot of carbon fibre. The threading machine stretches around 50 centimetres of thread per second between the nails. To achieve this, the machine accelerates at 5 g, as the individual thread segments from nail to nail are only a few millimetres to centimetres long. During the process, it is barely possible to follow the thread puller with your eyes. Before the threads are pulled, however, the nail machine has to hammer the nails into the plastic plate.
This also takes place at a high speed of around 12 nails per second. The precision tools from Horn come into play in the nailing process. Two opposing S274 inserts are clamped in the machine's nailing head. The inserts are not used for turning or milling, as is usually the case, but as a kind of pinching pliers. To ensure a sharp and precise cut, the inserts are sharpened and ground with a small wedge angle. "The machine feeds aluminium wire from a roll. In the process, the nailing head hammers the wire into the calculated position and cuts it to precisely 20 mm long using the inserts," explains Gall. Precision and reliability are very important when nailing. If one of around 8,000 nails doesn't fit properly or falls out, the whole process stops working. "The first enquiry from Mr Gall was somewhat unusual for us, as our tools are normally used in machining. But we also develop appropriate tool solutions for such special applications," says Horn sales representative Jürgen Schmid.
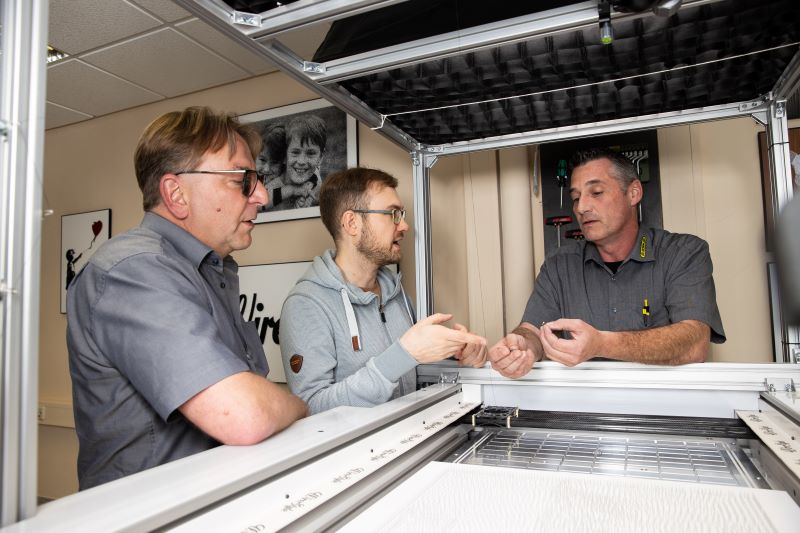
High precision
The indexable insert is mainly used for turning accurate components. Thanks to the precision insert seat, changeover accuracy is less than 0.003 mm. When machining turned parts of small diameter, the centre height of the tool must be measured precisely. Even the smallest deviation in the centre height has a negative effect on the quality of the workpiece during machining. Ideally, the machine operator should be able to turn the indexable insert without having to readjust the centre height. This is made possible by precise grinding of the insert periphery in conjunction with the stable insert seat.
Precision and sharpness are very important when cutting the nails. If the inserts are too far apart or twisted at an angle to each other, the aluminium wire will not be cut precisely. Furthermore, the inserts must not touch each other when cutting, otherwise the sharp edges will break off. "We are pleased that we have found an appropriate tool solution together with Horn that meets our requirements exactly," says Gall.