Swabian Precision Trilogy
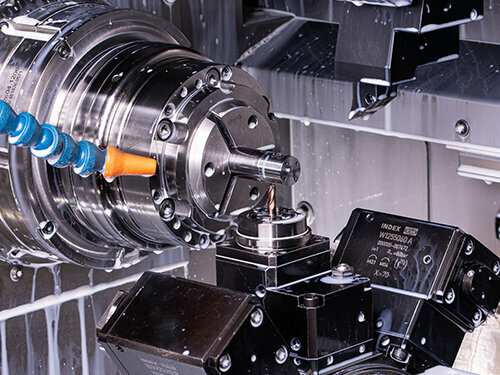
Precision tools, accurate lathes and a deep understanding of how to use the two to achieve micron precision. This describes the cooperation between Paul Horn GmbH, the machine manufacturer INDEX and the contract manufacturer of precision turned parts, RICH Praezision. "The proximity of all three companies to one another and the long partnership between us can be described as a success story," says Wolfang Rich. He and his brother Gottfried manage the company RICH Praezision as third-generation directors. RICH Praezision has relied on tool systems from HORN since the 1980s. The company is a customer of, as well as a supplier to, the Tübingen-based tool manufacturer.
It all began on 3rd March 1949 with Wilhelm Rich, the grandfather of the current managing directors. In 1986 and 1990 respectively, the current managing partners Wolfgang and Gottfried Rich joined the company. Today, RICH Praezision employs more than 40 people. The brothers have always specialised in the production of precision turned parts and complex workpieces and sub-assembly is becoming increasingly important. Under the motto "We start where others stop", the company manufactures workpieces for numerous industries. Specialities include, for example, components for gearboxes, high-quality electrical appliances, hydraulics and pneumatics as well as refrigeration technology.
Interface for precision tools
RICH Praezision has been a supplier to HORN for several years. The company produces the body of the precision interface for the HORN tool system SX, a further development of the 42X family. The cutting head is connected to the contact surface of the tool body via a stable, robust, yet highly accurate thread. This interface brings several advantages: High stability due to the generously sized mounting thread, excellent support due to the large contact surface and precise changeover accuracy to within microns, which is always in the middle of the tolerance band. Furthermore, changing the head is simple and user-friendly. The interchangeable head system is mainly used for milling tools that are brazed to the tool steel body.
"Manufacturing the tool holders was initially a great challenge. HORN's demands for precision are very high," explains RICH production manager Wolfram Stiefel. RICH manufactures several tens of thousands of parts in numerous variants for HORN every year. Stiefel also relies on HORN tools for producing the HORN component. Critical features for machining are, on one hand, the mounting thread and, on the other, several very closely toleranced fits. In addition, there is a further focus on the concentricity and axial run-out of the various contact surfaces.
High precision thread milling
The HORN circular interpolation milling system or the solid carbide DC milling system are used for milling the internal thread, depending on the diameter of the SX body. The inserts are precision ground to cut the special thread profile. The threads are milled using several infeeds. "The thread is checked using a plug gauge, which HORN provided us with," says Stiefel. Another tool type, a 306 circular milling cutter, is used to mill an internal recess. Stiefel chose milling for this because the process is more stable than turning in view of the unfavourable length/diameter ratio in the product series. "The circular interpolation milling system with interchangeable head, or as a monobloc version, can be adapted precisely for such milling tasks," says HORN field service representative, Frank Blocher.
The circular interpolation milling system from HORN offers the user a number of advantages: It is fast, reliable and achieves good surface finish. The tool, which is guided on a helical path, plunges into the material at an angle that may be either steep or very shallow. This makes it possible, for example, to produce threads in reproducibly high quality. Compared to machining with indexable inserts for larger diameters, or with solid carbide cutters for smaller diameters, circular milling is generally more economical. Circular milling cutters have a wide range of applications. They machine steel, special steels, titanium, aluminium and special alloys. The precision tools are particularly suitable for groove milling, helical milling, thread milling, T-slot milling, profile milling and gear milling. However, they are also ideal for special applications such as the milling of sealing grooves or in connecting rod machining.
HORN turning tools
Other HORN systems are used for turning operations on the component. For boring small diameter holes, RICH always uses the Mini and Supermini systems. In addition to the precision thread, a taper and a further fit are used for centring the interface with micron precision. Turning of the taper and the fit is done by a Supermini type 105. "The turning of the very close-tolerance fit is a stable process. However, due to the series production, the fit is finished with a reamer," explains Wolfgang Rich.
The component comes off the INDEX C100 automatic lathe finish machined. "The versatility, stability and adaptability of the machines from INDEX impressed us. The proximity of INDEX to Esslingen is also important. If we have a problem, someone from the service department is on site immediately, or we simply pick up the spare parts ourselves," says Gottfried Rich. For programming, RICH uses the virtual machine from INDEX. The machine operators create the programs themselves at several programming stations.