Down to the smallest detail
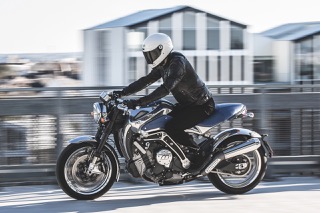
"Why don't we actually build motorbikes in France?" That's what Olivier Midy thought when he started the development of his own motorbike 30 years ago. Since the start, around 300,000 hours have gone into the development of his Midual Type 1. The inventor has built numerous technical specialities into the bike, paying attention to perfection down to the smallest detail. With an eye on precisely these details, Paul Horn GmbH supports Midy and his team with precision tools that are used to build this motorbike work of art. "We rely on tools from Germany because we need solutions that can fulfil our high quality requirements," says Midy.
The hallowed halls of the Midual company are located in the western French city of Angers. This is where Midy and his small team build the first-class, high-end motorbikes. Midy already had a passion for working on motorbikes as a teenager. In 1992, the mechanical engineer began developing his own motorbike. He initially financed the project from his own company, which produced parts for the automotive industry as a contract manufacturer. When building his Midual Type 1, Midy wanted to change everything that had gone before and eclipse it with technical perfection. So he began the development of the Type 1 on a blank sheet of paper.
Sand-cast aluminium monocoque frame
One special feature is the position of the two-cylinder boxer engine. For technical reasons, well-known manufacturers only install the engine transversely. Midy, however, has managed to install the boxer engine longitudinally. In order not to lengthen the wheelbase of the motorbike, he tilted the boxer forward by 25 degrees. This tilt also made it possible to install the six-speed gearbox under the rear cylinder and the bearing for the rear swing arm. Another highlight is the frame. While most motorbike manufacturers install a tubular frame with an attached sheet metal tank, the Midual Type 1 comes with an aluminium sand-cast monocoque frame with an integrated 14-litre petrol tank. "Alongside the engine development, the development of the frame took the most time. The casting, subsequent CNC machining and finishing by hand are very time-consuming. It takes around 80 hours to finish the frame," explains Midy. The buyer should have the necessary small change ready for the complete bike. The starting price is around 165,000 euros.
"What we can do ourselves, we do ourselves," says Midy. There are two CNC milling centres in his workshop for machining. In addition to engine components and frames, the milled parts also include the brackets, footrests and other add-on parts. Most of the small parts on the Type 1 are milled from solid material. With the exception of the indicators and plugs, there are virtually no plastic parts on this motorbike. Midy has been relying on tool solutions from Tübingen for numerous milling operations for three years.
High surface quality
Midy was looking for an appropriate tool solution for face milling the motor housing. It is made of an aluminium alloy and consists of two halves. The demands on the milled finish are high. The surfaces must lie within a narrow tolerance range after the milling process. Furthermore, the surfaces also serve as sealing surfaces later on. "In addition to flatness, high surface quality is an important criterion," says Midy. Midy came across HORN's tool systems through one of his employees, who had used them alreadyat his previous employer.
After the initial contact with HORN France, the first tests followed shortly afterwards. The HORN engineers used the DTM milling system with a diameter of 80 mm. The number of teeth is z = 7. Polycrystalline diamond (PCD) is used as the grade for machining the aluminium alloy. The PCD grade consists of a mixture of different sizes of diamond grains. As the volume percentage of diamond increases, so do the effective hardness, toughness and cutting edge quality. Strict quality standards and their control are a matter of course and ensure high performance. The anti-friction properties of the diamond surface in combination with the internal coolant supply prevent the formation of built-up edges. The tool mills across the workpiece at a cutting speed of vc = 600 m/min, an infeed of ap = 0.1 mm and a feed per tooth of fz = 0.01 mm. An almost mirror finish is achieved on the surface. "Monocrystalline diamond is normally used for milling high-gloss surfaces. However, with the high quality of PCD cutting edges, very good surface finishes can also be achieved. The surface is always a reflection of the cutting edge quality," explains HORN technician Roger Kasper.
Holder system with aluminium body
In addition to the quality of the cutting inserts, the holder system plays a decisive role. The insert seats in the tool holder are equipped with an adjustment system. The axial run-out can therefore be set with µ-precision using a presetter. The adjustment system of the inserts is designed to be user friendly. The aluminium body of the tool holders is lightweight for low energy consumption during acceleration and deceleration. The reduced mass compared to a steel milling cutter body also ensures faster acceleration and deceleration times. This enables highly dynamic milling processes. To prevent wear on the body due to chip impact, it is provided with a hardened protective coating.
"The quality of the milling result has impressed us. The better the production quality, the better the quality of our motorbikes. In addition to the sealing surfaces, we also mill decorative surfaces with the tool," says Midy. He developed the Midual Type 1 engine entirely by himself and also manufactures most of the engine parts himself. The unit has a displacement of 1,036 cm3 and an output of 107 HP at a speed of 7,800 rpm. The maximum torque of 98 Nm is available at 6,000 rpm. When developing the engine, Midy was not looking for maximum performance and brute power. He developed a comfortable and durable drive for the country road. "I ride my Midual almost every day and already have over 200,000 kilometres on the clock," says Midy. The six-speed gearbox was also designed by the Frenchman. He does not yet have the necessary machines in his factory to manufacture the gearbox. He has it manufactured by a supplier in Spain.
Small details
No matter where one looks: Every single component of the Type 1 is well thought out, of high quality and, where possible, milled from solid material. Midy even manufactures the screws for holding the leather parts himself. As he does not yet have a CNC lathe, the screws are milled and engraved with the Midual logo. For cut-off milling, he uses the circular milling system from HORN. In addition to groove and circular milling, the system also exhibits high performance during cut-off milling. Like every part of a Type 1, the screw heads receive appropriate post-treatment by hand polishing after milling.
Midy relies on HORN's Supermini N105 tool system for broaching splines. The splines are required, for example, on the foot lever for shifting gears. The precision-ground tool cutting edge matches the profile of the teeth. During the shaping process, the infeed of the individual strokes is 0.1 mm. Once a tooth has been completed, the spindle continues to rotate to move on to the next tooth.
Looking to the future
Midy has already built around 40 of his Midual Type 1s. The motorbike virtuoso is already developing his Type 2, for which he also needs the support of his partners. "We are really looking forward to the next projects. We are happy to have strong partners like HORN at our side supporting us with their solutions and expertise," summarises Midy.
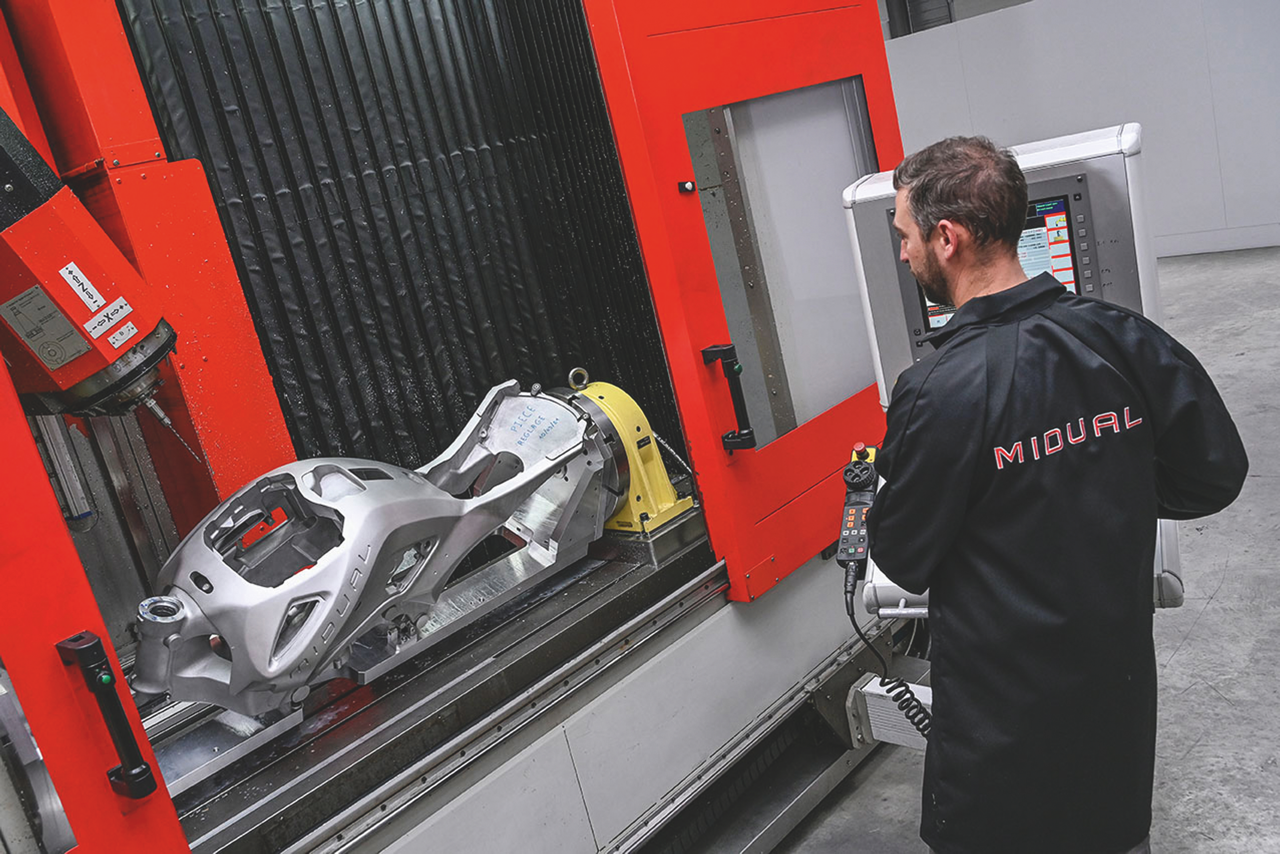
Source: Horn/Sauermann
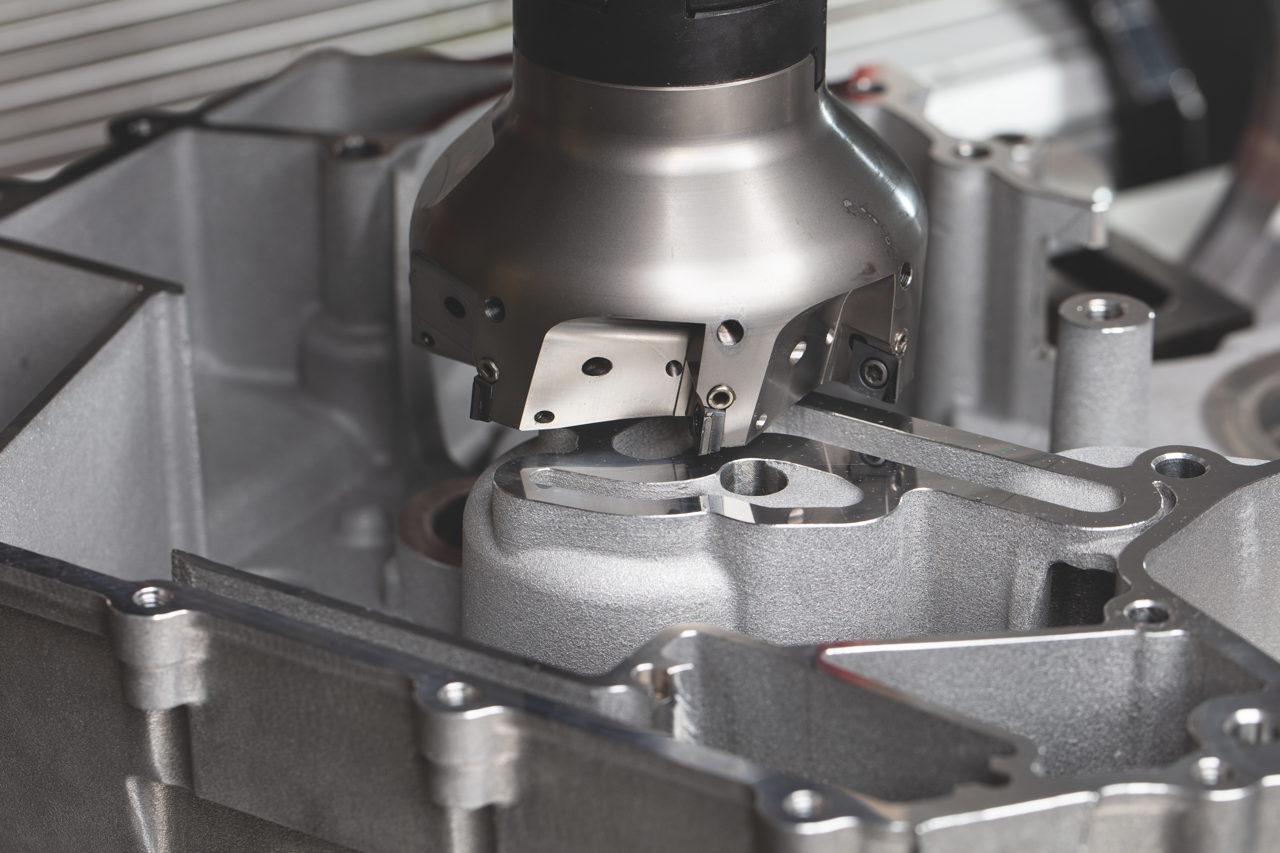
Source: Horn/Sauermann