Mikroschrauben für die Uhrenindustrie
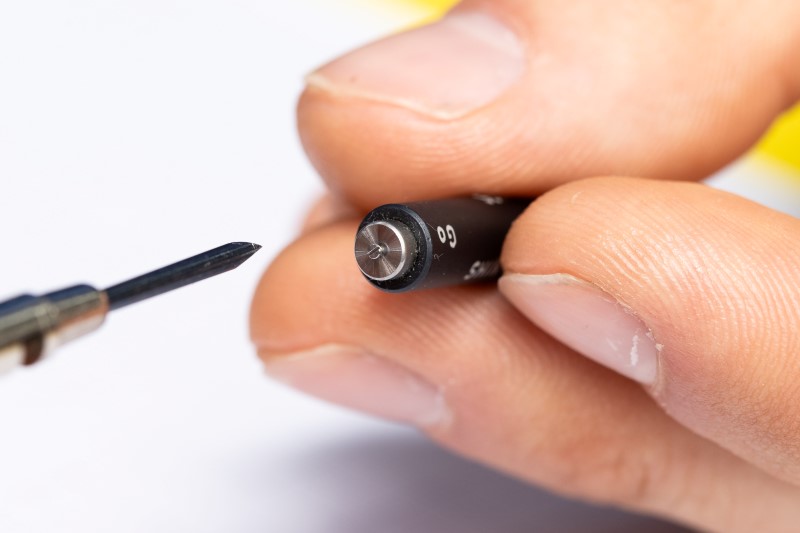
Damit das berühmte „Schweizer Uhrwerk“ rund läuft sind neben zahlreichen Präzisionsbauteilen und Zahnrädern, die eingesetzten Schrauben die Elemente, welche das feinmechanische Meisterwerk am Schluss zusammenhalten. Für die Produktion dieser Schrauben ist einiges an Knowhow gefragt. Kein Wunder, dass die bekannten schweizer Uhrenmanufakturen auch auf die Mikropräzisionsschrauben aus dem eigenen Land setzen. Ein Hersteller solcher Schrauben ist die Aeschlimann AG Décolletages aus Lüsslingen im Kanton Solothurn. Für die Mikrozerspanung setzen die Spezialisten um den ausgebildeten Mikromechaniker Mattia Knecht auf das µ-Finish System der Paul Horn GmbH. Die technische Beratung in Werkzeugfragen bekommt Knecht von der Schweizer Horn-Vertretung DIHAWAG, mit dem zuständigen Außendienstmitarbeiter Dominik Läng.
Von Mikro-Uhrenbauteilen über Bauteile der Medizintechnik bis hin zu Bagger-Hydraulikbauteilen. Die Aeschlimann AG Décolletages gilt als Spezialist für die Fertigung von präzisen rotationssymetrischen Werkstücken. Gegründet als Schraubenmacher-Atelier im Jahr 1937 entwickelte sich das Unternehmen zu einem Hersteller von komplexen CNC-Bauteilen und bietet seinen Kunden spezielle Nachbearbeitungsverfahren wie Honen, Spitzen- und Centerless-Schleifen sowie Optionen für das Super-Finishing. Mit 165 Mitarbeitern fertigen die Schweizer vornehmlich Drehteile bis zu einem Durchmesser von 120 mm. Aber auch bei Frästeilen bis zu einer Kantenlänge von 300 mm zeigt Aeschlimann sein Knowhow in der Zerspanung. Zu den Kunden zählen Unternehmen aus der Uhren-, Automobil-, Hydraulik-, Maschinen- und Elektronikindustrie. Darüber hinaus liefert Aeschlimann die schweizerische Präzision auch an die Medizinal-, Messtechnik- und Fahrradbranche.
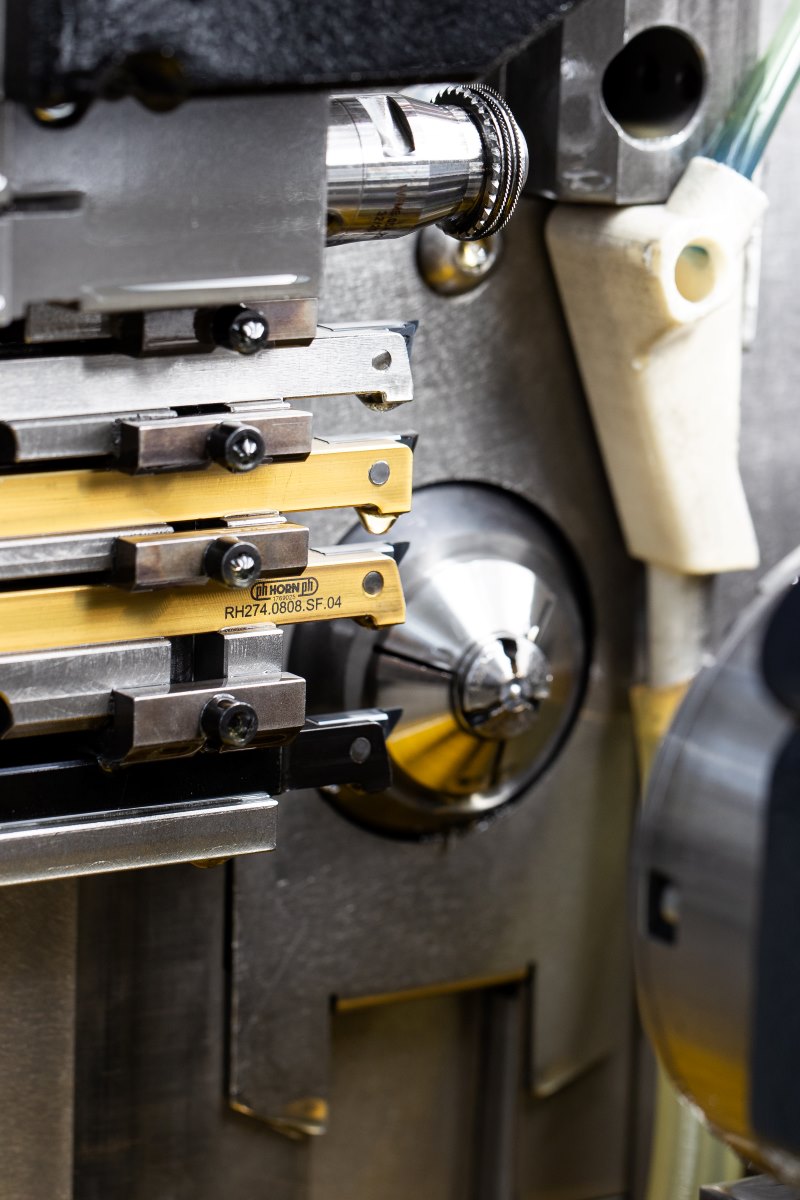
Filigrane Bauteile
Ein schweizer Uhrwerk besteht je nach Kaliber aus vielen einzelnen Baugruppen: Beispielsweise Räderwerk, Aufzug, Antrieb, Unruh oder das Zeigerwerk. Bei einem Uhrenkaliber mit vielen Komplikationen sind auf kleinstem Raum viele Bauteile zu einem Uhrwerk montiert. Für den Zusammenbau der einzelnen Bauteile kommen Schrauben zum Einsatz. Für die Herstellung dieser Schrauben würde sich der „normale“ Zerspaner wohl die Zähne ausbeißen. Die Werkstücke sind mit bloßem Auge kaum von einem Span zu unterscheiden. „Das Handling und Messen der Schrauben ist eine große Herausforderung, welche einiges an Übung bedarf. Die Maßkontrolle erfolgt nicht mit einer Bügelmessschraube, sondern unter einem Mikroskop mit 50-facher Vergrößerung“, erzählt Knecht. Die Fingerfertigkeit beim Hantieren der Schrauben zeigt sich auch beim Prüfen der Gewinde mit einem Gewindelehrring. „Hierzu benötigt man viel Erfahrung, um Schrauben mit Durchmessern weit unter einem Millimeter von Hand in die Gewindelehre zu drehen“, so Knecht.
Für das Langdrehen der Uhrenschrauben setzt man bei Aeschlimann auf das Horn-Werkzeug µ-Finish und Maschinen von Tornos des Typs Swiss Nano. Das Werkzeugsystem hat als Hauptzielgruppe Anwender in der Mikrobearbeitung. Die Basis für das Werkzeugsystem baut auf dem System S274 auf. Die Schneiden sind mit hoher Sorgfalt geschliffen. Jedes Werkzeug durchläuft in der Fertigung eine 100 Prozent Kontrolle, um die hohe Schneidkantenqualität sicherzustellen. Der Plattensitz des Werkzeugträgers ermöglicht in Verbindung mit der zentralen Klemmschraube und dem präzisionsgeschliffenen Umfang der Wendeschneidplatte eine Wechselgenauigkeit im µm-Bereich. Dies ermöglicht das Drehen der Schneidplatte in der Maschine, ohne die Spitzenhöhe und die anderen Maße neu ausmessen zu müssen. „Horn bietet Highend-Werkzeuge für viele Anwendungen. Von der Uhrenschraube, vom Medizintechnik-Bauteil bis hin zum Hydraulikteil gibt es Lösungen. Wir setzen Horn-Werkzeuge auf einigen unserer Maschinen ein“, sagt Knecht. Neben zahlreichen Standardprofilen sind auch Schneidplatten mit Sonderformen, gemäß Kundenwunsch, erhältlich.
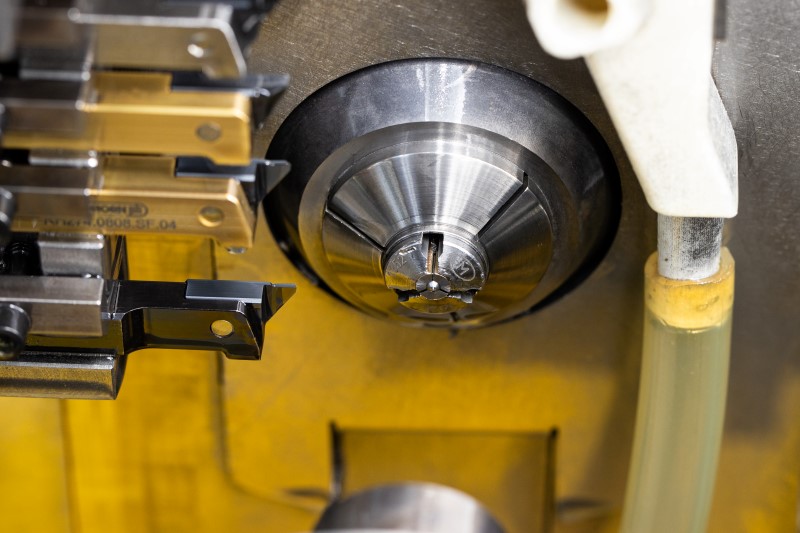
Vorschübe im µ-Bereich
„Die Qualität der Schneidkante spielt die entscheidende Rolle bei der Mikrobearbeitung. Man kann Vorschübe nur im µ-Bereich fahren, wenn die Schneide auch im µ-Bereich scharf ist“, sagt Dominik Läng. Für den Drehprozess einer Schraube kommen drei unterschiedliche Werkzeuge zum Einsatz. Zuerst wird die Planfläche des Schraubenkopfes gedreht. „Wir drehen den Kopf zuerst, da wir die Schraube nicht auf dem feinen Gewinde abgreifen und spannen können“, so Knecht. Die kleinste Schraubenvariante, die man bei Aeschlimann fertigt, hat einen Gewindedurchmesser von 0,2 mm. Nach der Bearbeitung der Planfläche wird der Schraubenkopf geschlitzt. Anschließend wird über das Rückwärtsdrehen der Durchmesser des späteren Gewindes gefertigt. Über eine Fräsbearbeitung geschieht die Herstellung des Gewindes. Dies bietet die Möglichkeit das Gewinde, ohne einen Freistich bis zum Schraubenkopf zu fräsen. Den Abstich der Schraube übernimmt wieder ein Horn-Werkzeug aus dem µ-Finish-Programm.
Die Standzeit einer Schneide beim Rückwärtsdrehen liegt bei rund 17.000 gefertigten Schrauben. Beim Abstechen erreicht die Schneidkante eine Standmenge von 40.000 Schrauben. „Durch die neue Horn-Beschichtung ES15, konnten wir die Produktivität nochmal steigern“, sagt Knecht. Die neue Beschichtung ist eine HiPIMS-Schicht (Hochleistungsimpuls-Magnetronsputtern). HiPIMS erzeugt eine noch homogenere und deutlich haltbarere Schicht, deren Härte und Zähigkeit besonders bei der Stahlzerspanung und beim Bearbeiten von Klein- und Kleinstteilen ihre Stärken zeigt. HORN setzt bei seinen Werkzeugschichten auf die PVD-Technik (physical vapor deposition). PVD ist ein Verfahren, bei dem das Beschichtungsmaterial durch Elektronen, Laserstrahlen oder Lichtbogenentladungen verdampft wird. Das verdampfte Material legt sich auf den zu beschichtenden Werkstücken ab, wo es zur Schichtbildung kommt. Unter der Zufuhr von Prozess-Reaktivgasen kann die Schichtzusammensetzung beeinflusst werden. So entstehen beim Beschichtungsprozess Nitride oder Karbide beziehungsweise Mischungen der beiden Schichten. PVD-Schichten erhöhen die Standzeiten von Zerspanungswerkzeugen sehr deutlich um ein Vielfaches.
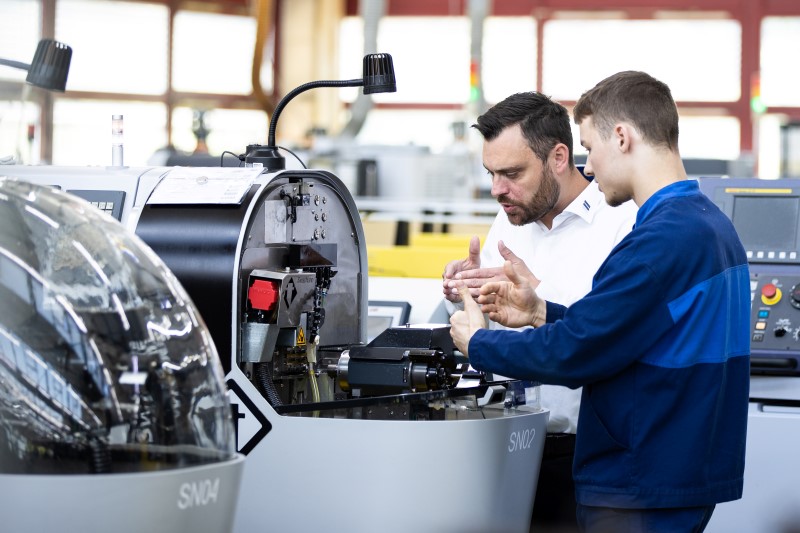
Partnerschaft
In der Schweiz vertritt das Unternehmen Dihawag den deutschen Werkzeughersteller Horn. Die Partnerschaft zwischen Aeschlimann – Horn – Dihawag besteht schon seit über 20 Jahren. In dieser Zeit konnte Horn mit seinen Werkzeugen schon einige Zerspanaufgaben erfolgreich lösen. „Die Zusammenarbeit ist top. Die technischen Berater von Dihawag und Horn kümmern sich schnell und zuverlässig um unsere Zerspanaufgaben. Es besteht eine echte Partnerschaft und die Lieferzeiten der Werkzeuge sind sehr kurz“, so Knecht.