An icon of tool technology
"This will revolutionise boring," Paul Horn thought to himself as he closely examined the first prototype of the Supermini. The Supermini system was then launched in 1989 and remains one of Paul Horn GmbH's most successful products to this day. Over the last 35 years, the tool system has undergone numerous development stages and has solved the challenges of a wide variety of machining applications worldwide. Horn is now presenting another milestone in the history of the Supermini with a sintered chip breaking geometry for the Supermini type 105. "With a lot of hard work, we have managed to solve economically the problems of long swarf when internally machining small bore diameters," says Managing Director Markus Horn.
Boring, profile turning, internal grooving, threading, chamfering, face grooving, drilling and slot broaching: The Supermini tool system can be adapted for numerous machining operations. The solid carbide inserts are used for boring from a diameter of 0.2 mm to around 10 mm. Horn developed the carbide blanks for the tool as a teardrop shape. This enables large, precise contact surfaces in the tool holder, which results in greater rigidity of the overall system. Furthermore, the teardrop shape prevents the insert from twisting, which leads to consistently precise positioning of the centre height of the tool. With long tool overhangs, it reduces deflection and minimises vibration during turning. Depending on the application and the diameter to be machined, Horn offers the inserts in three different sizes (types 105, 109 and 110) and different blank types. All types allow internal coolant supply directly to the cutting zone. The Horn tool portfolio contains around 2,500 different standard variants of the Supermini. In addition, Horn solves users' machining problems with countless customised solutions.
Chipping problems solved
One of the biggest challenges in internal machining is the generation of long swarf. Depending on the material, boring often leads to ribbons that wrap around the tool, clog holes or, in the worst case, lead to tool breakage. This is where chip breaking geometry can help. It guides and shapes the chip and causes it to break. Previously, specially lasered or ground chip breaking geometries were used for this purpose. However, this increased the cost of the inserts. With the new Supermini type 105, Horn has succeeded in developing a universal boring tool with sintered chip breaking geometry. The tool offers high process reliability due to its good chip control. The cutting edge geometry extends far into the corner radius of the insert. This ensures chip control even with small infeed settings. The geometry can be used universally for different material groups and is suitable for internal, face, copy and back turning.
In addition to the geometry, Horn optimised the carbide blanks of the inserts to have greater rigidity and an even more stable cutting edge area. The coolant supply has also been revised. The new insert is compatible with numerous types of 105 tool holders. Horn offers the inserts as standard in three lengths (15.0 mm, 20.0 mm and 25.0 mm) and in carbide grades TH35 and IG35. The corner radius is 0.2 mm. The tool is suitable for use from a bore diameter of 6 mm. The wide range of applications for the inserts goes hand in hand with their cost-effectiveness, as the price of the new Supermini is similar to that of the standard insert without geometry. The new Supermini will be available from stock from 12/06/2024.
Users can choose the appropriate solution for their application from a wide range of different types of tool holder. These include round shank, square shank, interface and adjustable tool holders for different machine manufacturers. Horn offers four different solutions for clamping the inserts: a classic ball pressure screw, a face clamping element and a lifting element. For confined spaces, Horn also offers a compact system with clamping via a union nut.
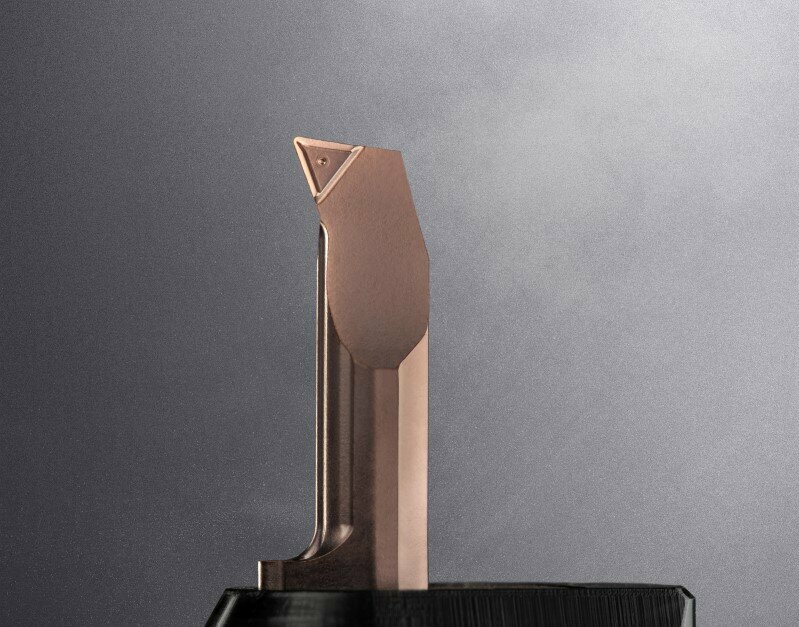
An icon of tool technology
"This will revolutionise boring," Paul Horn thought to himself as he closely examined the first prototype of the Supermini. The Supermini system was then launched in 1989 and remains one of Paul Horn GmbH's most successful products to this day. Over the last 35 years, the tool system has undergone numerous development stages and has solved the challenges of a wide variety of machining applications worldwide. Horn is now presenting another milestone in the history of the Supermini with a sintered chip breaking geometry for the Supermini type 105. "With a lot of hard work, we have managed to solve economically the problems of long swarf when internally machining small bore diameters," says Managing Director Markus Horn.
Boring, profile turning, internal grooving, threading, chamfering, face grooving, drilling and slot broaching: The Supermini tool system can be adapted for numerous machining operations. The solid carbide inserts are used for boring from a diameter of 0.2 mm to around 10 mm. Horn developed the carbide blanks for the tool as a teardrop shape. This enables large, precise contact surfaces in the tool holder, which results in greater rigidity of the overall system. Furthermore, the teardrop shape prevents the insert from twisting, which leads to consistently precise positioning of the centre height of the tool. With long tool overhangs, it reduces deflection and minimises vibration during turning. Depending on the application and the diameter to be machined, Horn offers the inserts in three different sizes (types 105, 109 and 110) and different blank types. All types allow internal coolant supply directly to the cutting zone. The Horn tool portfolio contains around 2,500 different standard variants of the Supermini. In addition, Horn solves users' machining problems with countless customised solutions.
Chipping problems solved
One of the biggest challenges in internal machining is the generation of long swarf. Depending on the material, boring often leads to ribbons that wrap around the tool, clog holes or, in the worst case, lead to tool breakage. This is where chip breaking geometry can help. It guides and shapes the chip and causes it to break. Previously, specially lasered or ground chip breaking geometries were used for this purpose. However, this increased the cost of the inserts. With the new Supermini type 105, Horn has succeeded in developing a universal boring tool with sintered chip breaking geometry. The tool offers high process reliability due to its good chip control. The cutting edge geometry extends far into the corner radius of the insert. This ensures chip control even with small infeed settings. The geometry can be used universally for different material groups and is suitable for internal, face, copy and back turning.
In addition to the geometry, Horn optimised the carbide blanks of the inserts to have greater rigidity and an even more stable cutting edge area. The coolant supply has also been revised. The new insert is compatible with numerous types of 105 tool holders. Horn offers the inserts as standard in three lengths (15.0 mm, 20.0 mm and 25.0 mm) and in carbide grades TH35 and IG35. The corner radius is 0.2 mm. The tool is suitable for use from a bore diameter of 6 mm. The wide range of applications for the inserts goes hand in hand with their cost-effectiveness, as the price of the new Supermini is similar to that of the standard insert without geometry. The new Supermini will be available from stock from 12/06/2024.
Users can choose the appropriate solution for their application from a wide range of different types of tool holder. These include round shank, square shank, interface and adjustable tool holders for different machine manufacturers. Horn offers four different solutions for clamping the inserts: a classic ball pressure screw, a face clamping element and a lifting element. For confined spaces, Horn also offers a compact system with clamping via a union nut.
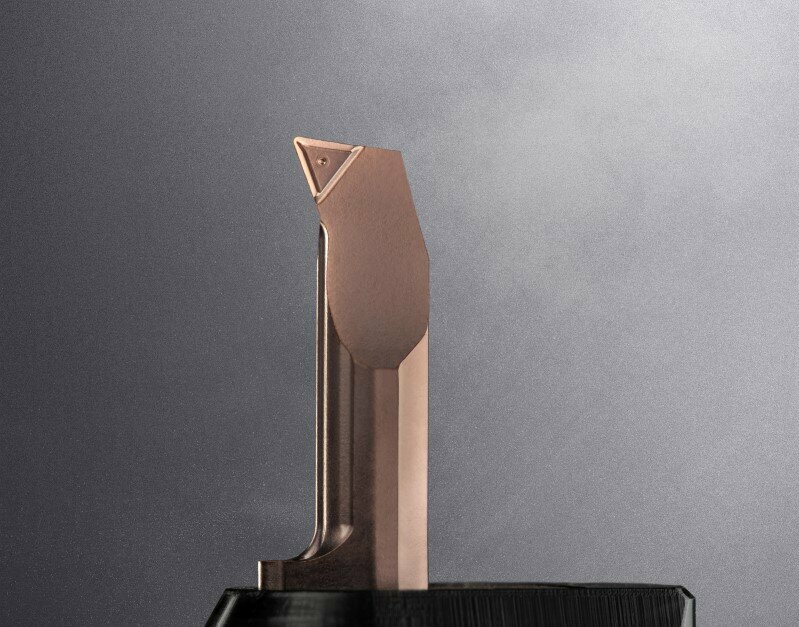