Excellent Industry 4.0 strategy
Paul Horn GmbH in Tübingen is continuously driving forward the further development and digitalisation of its entire value chain. In order to accelerate digitalisation in the production environment, Horn has developed a scalable standard solution for connecting existing and new systems. Thanks to the optimised networking of the systems, Horn customers benefit in many areas including even better delivery performance.
In 2018, Horn launched a project to digitalise and network existing systems (retrofit). The objectives include the introduction of a service-oriented architecture (SOA) in production and the standardisation of data in terms of the asset administration shell. The concept developed is also intended to form the basis for connecting future systems. In the preliminary study of the project, it quickly became clear that the entire IT architecture of production must be considered for sustainable digitalisation. The concept of so-called production capsules describes both the methodical approach for replacing the automation pyramid and a generic Industry 4.0 architecture consisting of infrastructure (hardware, networks, locations), applications, interfaces, technologies and processes.
The production capsule is a functional unit of components that is required to fulfil a specific purpose. For example, a production capsule in the field of grinding consists of at least one CNC machine and is supplemented by automation, a computer for edge computing or more if required. The concept deliberately does not limit the scope of a capsule, which means it can be applied generically. This ranges from individual smart sensors to entire production areas.
In addition to logical demarcation, the Industry 4.0 concept also addresses the encapsulation of the resulting data. This primarily involves the targeted concealment of information from unauthorised access and the definition of standard interfaces (black box model). It is not possible for outsiders to communicate with individual components of a capsule. They only see the data and functions that it deliberately provides. Together with a semantic data model, this creates the basis for the standardisation and service orientation of production. With the use of OPC UA, an appropriate standard is available to realise the concept while taking IT security into account.
Technically, encapsulation already takes place at network level through the use of physical or virtual routers with local firewalls. The central communication partner of a capsule that can be reached from the outside is called an integrator. The task of an integrator is to support the connection of the components - for example by translating proprietary protocols into OPC UA and by harmonising and aggregating the data. The (M2M) communication of the other components within a capsule remains unaffected. The integrator also provides local services for pre-processing the collected data or for web visualisation.
Horn has already equipped the majority of its machinery with production capsules. The flexibility and scalability of the concept allow a wide variety of systems to be connected quickly. The precision tool manufacturer has around 600 machines and systems in production worldwide. There are also devices from other areas, such as building management systems. The added value is evident in the diverse challenges faced by the various business units. Administration costs are reduced for IT, as remote maintenance is automated and the system operator can activate it using a key switch. IT security is increased by isolating the systems on the network side - a single defective machine has no effect on the rest of production. In-house mechanical engineering and maintenance benefit from manageable warehousing and the long-term availability of the installed and standardised hardware. The recorded data can be automatically recorded and evaluated thanks to the standardisation and semantic description. The power and machine data, such as spindle speed or temperatures, are recorded centrally via the integrator and made available in a standardised manner via OPC UA. The solution enables visualisation based on the data models. This enables, for example, an overview of the status of all machines on a production line. André Hoettgen, Industry 4.0 architect at HORN: "Networking the systems makes it possible to optimise existing processes and rethink future production technologies. Collective intelligence improves delivery performance and paves the way for even more versatile tools."
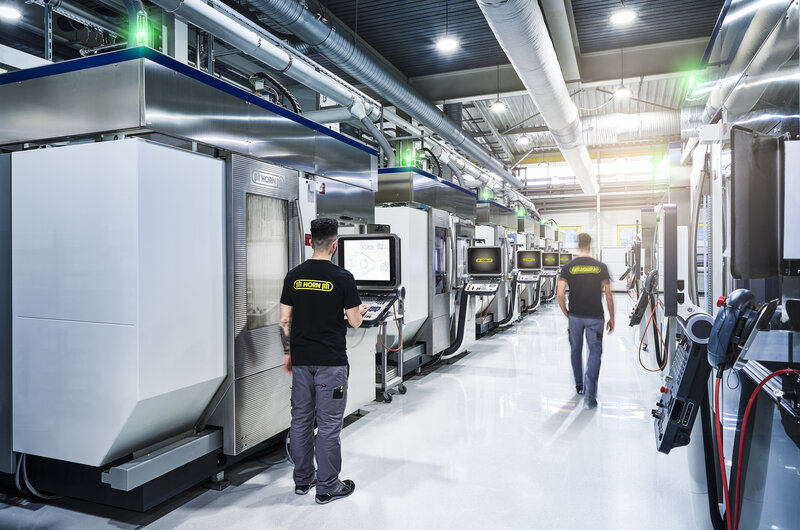