Precision from Allgäu
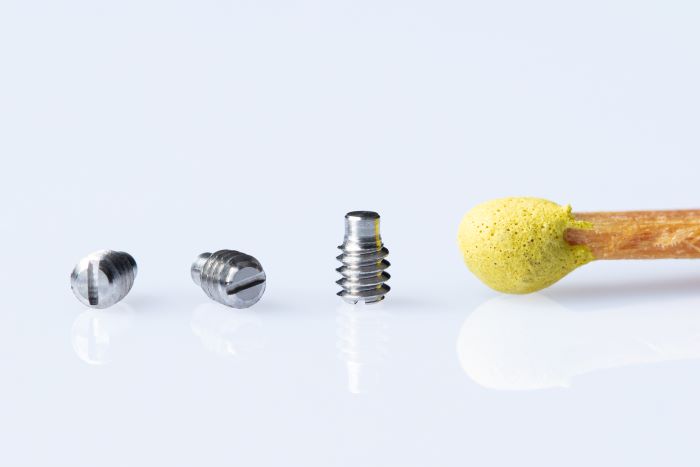
Reinhard Buck’s company motto “Gscheid gmacht” not only appears on his company logo. The entrepreneur lives the motto together with his employees in his company zmtec. In Leutkirch in the Allgäu, the company produces everything from microcomponents to complex assemblies. Reinhard Buck's specialities include micro-turned parts from a diameter of 0.5 mm (0.020"). For productive machining, he relies on tool systems from Paul Horn GmbH. “We see the large variety of tools and the good price in relation to tool life as a great advantage of HORN,” he says. For machining a rotary slide with a diameter of 1.6 mm (0.063"), Buck relies, among other things, on the S274 tool system and the 606 circular milling tool with a cutting width of 0.3 mm (0.012").
Absolutely no burrs essential
Buck saw the potential to optimise the machining process for the rotary slide, which is used in a hydropneumatic valve. The company produces around 20,000 of the X8CrNiS18-9 (1.4305) components per year. The component has a length of 2.6 mm (0.102"), a thread size of M 1.6 and a fit with a diameter of 1 h8. To set the rotary slide in use, a slot with a width of 0.3 mm (0.012") and a depth of 0.5 mm (0.020") has to be milled on the threaded portion of the turned part. "The difficulty in machining is, among other things, the need for a total absence of burrs on the component. When you mill a slot in a thread, freedom from burrs is not easy to achieve. You cannot simply deburr such a small component with a file. The thread would immediately be unusable," Buck explains.
For the Swiss-type machining of the outer contour, Buck relies on the HORN S274 tool system. "For machining stainless steel, we chose the IG35 tool coating. This offers high performance when machining stainless steels, titanium and superalloys," explains HORN sales representative Gisbert Voß. In combination with the HORN chipbreaking geometries, the aluminium-titanium silicon nitride coating inhibits the formation of built-up edges due to the low friction. As a result of the HiPIMS coating technology, the layer has very smooth properties and high heat resistance. Furthermore, the tool coating is free from coating defects such as droplets on the cutting edge. The user can run higher cutting values, which enable a shorter cycle time and has a positive effect on unit production costs. In addition, the use of the coating allows higher quality surfaces to be achieved.
Slot milling with the System 606
After turning the outer contour, a cutting insert from the S274 system takes over the production of the thread. The M 1.6 thread has a length of 2.2 mm (0.087") and a pitch of P = 0.35 mm (0.014"). After thread turning, the next machining step is milling the slot. "We used to cut the slot with a fine HSS saw blade. There was potential for improvement here," says Buck. Voß suggested milling the slot with the Type 606 six-flute circular milling system. The first trials were immediately successful and Buck replaced the HSS tool with the HORN milling system. To ensure that the part is burr-free after slot milling, the thread turning and slot milling process is repeated three times. "After that, the component is burr-free," says Buck.