Micro screws for the watch industry
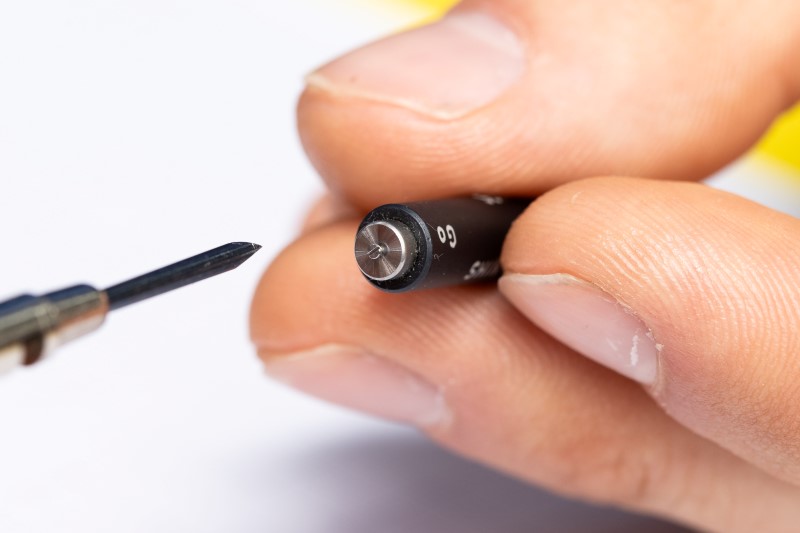
To ensure that the famous "Swiss movement" of a watch runs smoothly, in addition to numerous precision components and gears, the precision mechanical masterpiece must ultimately be held together by screws. Their production requires a great deal of know-how, so it is no wonder that well-known Swiss watch manufacturers rely on micro-precision screws from their own country. One manufacturer of such screws is Aeschlimann AG Décolletages from Lüsslingen in the canton of Solothurn. For micromachining, the specialists led by trained micromechanic Mattia Knecht rely on the µ-Finish system from Paul Horn GmbH. Knecht receives technical advice on tooling issues from Dominik Läng, an engineer at Dihawag, Horn’s sales agent in Switzerland.
From micro watch components to parts for the medical industry to excavator hydraulic components, Aeschlimann AG Décolletages is considered a specialist in the manufacture of precise, rotationally symmetrical workpieces. Founded as a screwmaker's workshop in 1937, the company has evolved into a manufacturer of complex CNC components and offers its customers special finishing processes such as honing, cylindrical and centreless grinding, and options for super-finishing. With 165 employees, the Swiss company primarily produces turned parts up to a diameter of 120 mm. However, Aeschlimann also demonstrates expertise in milling parts up to 300 mm long. Its customers include companies from the watchmaking, automotive, hydraulics, machinery and electronics industries. In addition, Aeschlimann supplies precision Swiss components to the medical, metrology and bicycle industries.
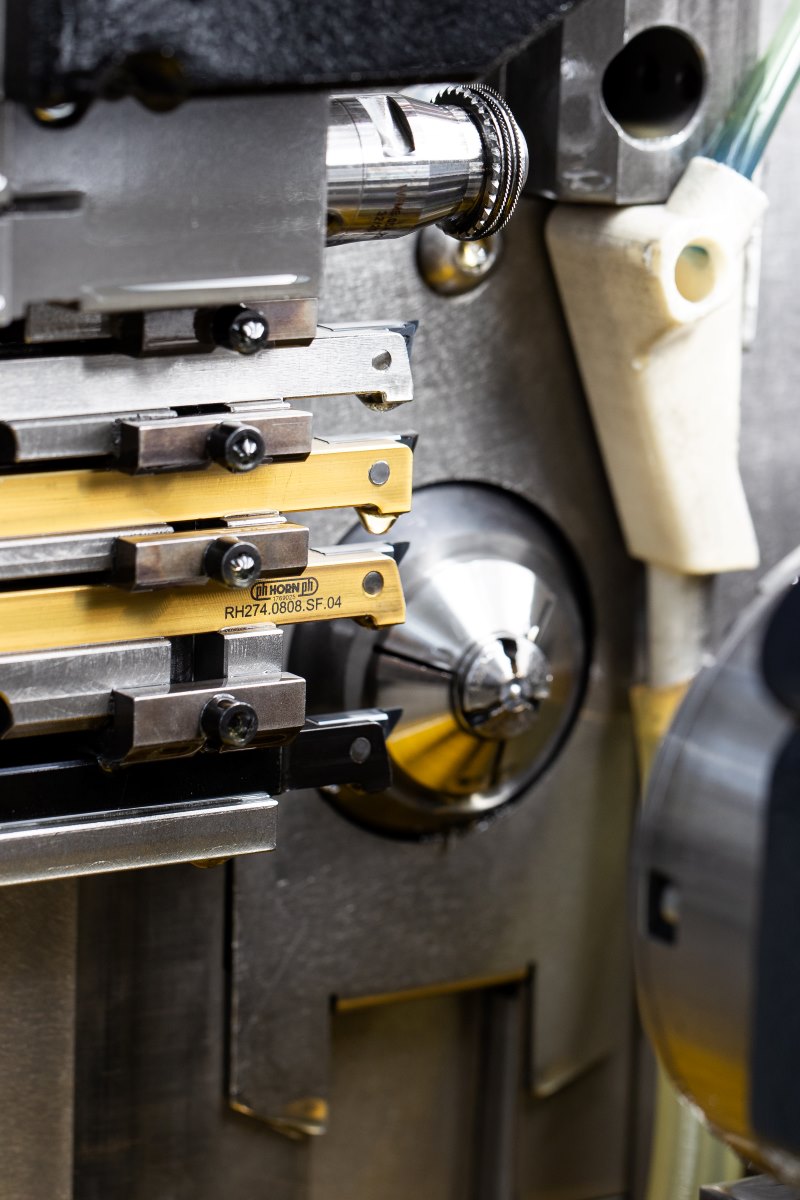
Delicate components
Depending on its quality, a Swiss movement consists of many individual components, for example the gear train, the winding mechanism, the drive, the balance and the hand movement. In a complicated, high-quality watch, many components are assembled into a movement within a very small space. Screws are used to assemble the individual components. To produce these screws, an average machinist would probably find it very difficult.With the naked eye, the workpieces can hardly be distinguished from a piece of fine swarf. "Handling and measuring the screws is a considerable challenge that requires a lot of practice. The dimensions are not checked with a micrometer, but under a microscope with 50-fold magnification," Knecht explains. The dexterity required to handle the screws is also evident when checking the threads with a thread ring gauge. "You need a lot of experience to turn screws with diameters far below one millimetre into a thread gauge by hand," says Knecht.
Aeschlimann relies on the Horn µ-Finish tool system and Tornos Swiss Nano machines for sliding-head turning of watch screws. Micromachinists are the main target market for this range of tools, which is based on the S274 system. The inserts are ground with great care. Each tool undergoes a 100 percent inspection during production to ensure high cutting edge quality. The insert seat of the tool carrier, in conjunction with the central clamping screw and the precision-ground periphery of the indexable insert, enables a changeover accuracy within microns. This allows the insert to be rotated in the machine without having to remeasure the centre height and other dimensions. "Horn offers high-end tools for many applications. From watch screws to medical industry components and hydraulic parts, there are solutions. We use Horn tools on a range of our machines," says Knecht. In addition to numerous standard profiles, inserts with special shapes are also available to meet customer requirements.
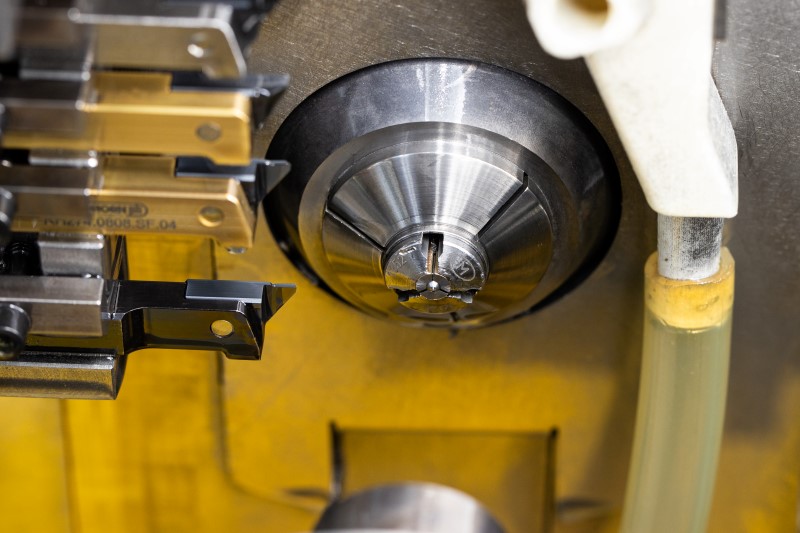
Feed rates in the µ range
"The quality of the cutting edge plays an important role in micromachining. You can only run feeds in the micrometre range if the insert is similarly sharp," says Dominik Läng. Three different tools are used for turning a screw. First, the face of the screw head is axially turned. "We turn the head first because we cannot pick up and clamp the screw on the fine thread," says Knecht. The smallest screw variant produced at Aeschlimann has a thread diameter of 0.2 mm. After machining the flat surface, the screw head is slotted. Then the thread diameter is turned by reversing the direction of spindle rotation, after which the thread is milled up to the screw head without a undercut. Tapping of the screw is again done by a Horn tool from the µ-Finish programme.
The service life of an insert during reverse turning is around 17,000 screws. When parting off, the cutting edge achieves a tool life of 40,000 screws. "With the new Horn coating ES15, we are able to increase productivity even more," says Knecht. The new coating is a HiPIMS layer (high-performance impulse coating magnetron sputtering). HiPIMS produces an even more homogeneous and significantly more durable coating whose hardness and toughness are especially suitable for steel machining and for machining small and very small parts. Horn also uses PVD (physical vapour deposition) technology for its tool coatings. PVD is a process in which the coating material is vapourised by electrons, laser beams or arc discharges. The vapourised material is deposited as a layer on the workpieces, forming a layer. By varying the supply of reactive process gases, the coating composition can be influenced. In this way, nitrides or carbides or mixtures of the two layers are formed during the coating process. PVD coatings increase the service life of cutting tools many times over.
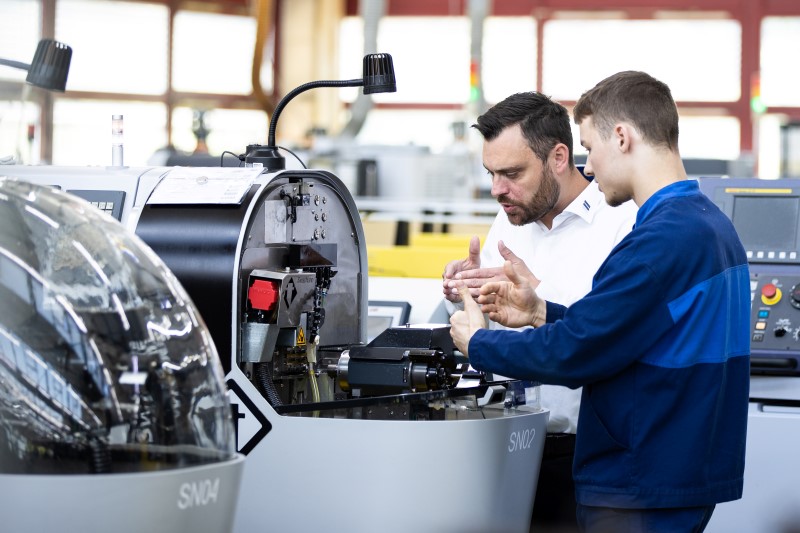
Partnership
In Switzerland, the company Dihawag represents the German tool manufacturer, Horn. The partnership between Aeschlimann, Horn and Dihawag has existed for over 20 years. During this time, Horn has been able to successfully solve a number of machining applications with its tools. "The cooperation is paramount. The technical advisors from Dihawag and Horn take care of our machining applications quickly and reliably. There is a real partnership and delivery of the tools is very quick," says Knecht.