High surface quality at high speed
Nickel-based alloys, titanium, cobalt-chrome: Reliable machining of these problematic materials requires a high level of expertise on the part of the user. If the workpieces also require high surface quality, the use of specialised tools is essential. HORN addresses this need with a CBN tool system that is unique on the market. Geometries specially developed for finishing ensure high surface quality, tight tolerances and high process reliability when machining the material groups P, K and S. Moreover, HORN is pushing the boundaries of machining speed with this system.
In operation, the tools achieve speeds of 350 m/min (1,148 ft/min) when cutting Inconel and 300 m/min (984 ft/min) when cutting titanium alloys, for example. The tools produce surfaces with an almost mirror-like finish. The combination of cutting material, quality of the tool edge grinding, coating and coolant supply enables the high performance. The reliable process is enhanced by the linear wear behaviour of the CBN cutting material. Wear rate is therefore predictable. The finishing system is available as standard in numerous HORN tool systems. In addition to various ISO inserts, HORN offers CBN inserts for the Supermini, Mini, 229 and 315 systems, as well as for the DTS milling system.
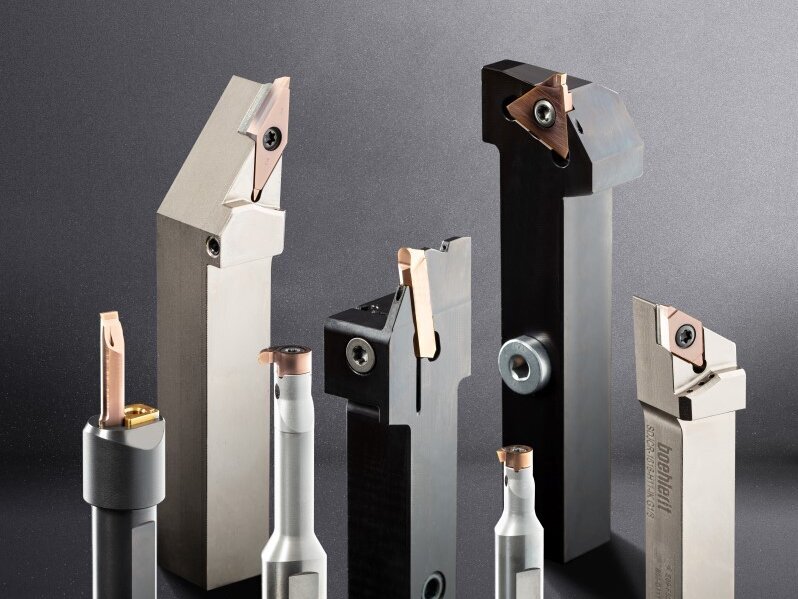