High-end connections for extreme requirements
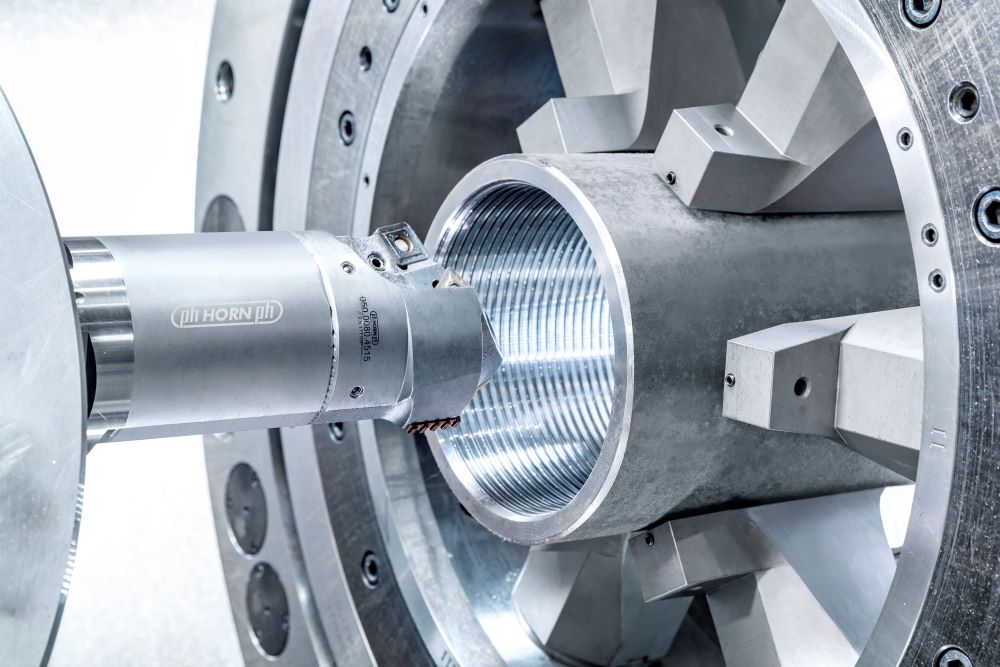
Sweat, steel and tough guys: working in the oil drilling industry is not for the faint-hearted. Handling the drill head with lashing chains, casing pipes weighing tonnes and the deafening noise all demand a lot from the workers. At the same time, the strenuous work makes it difficult for onlookers to imagine that the drill pipes and couplings are made using precision technology to µ-accuracy. The economical production of gas-tight threads requires a great deal of expertise and precise interaction between machine and tool. SMS group offers this combination using stable RMG coupling threading machines and tool systems from Paul Horn GmbH.
In tough conditions, oil riggers do not wear kid gloves when screwing together drill pipes. Consequently, the threads have an average service life of five tightening cycles. During these cycles, a gas-tight connection between the pipes and couplings must be ensured. Only with premium threads meeting the highest ISO-13679 standard can the diverse and complex requirements be met and the oil deposits safely tapped. In addition to premium threads, API and GOST threads are used. "The API and GOST thread types are for less demanding tasks. However, the production of these threads is also subject to strict quality requirements," explains Horn product manager Matthias Götze.
Extreme conditions
So-called sour service pipes with premium threads can withstand aggressive and corrosive substances such as hydrogen sulphide or sulphuric acid. The large deposits near the Arctic Circle can only be tapped using premium threads developed especially for the harsh conditions and special high-strength, high-alloy pipe materials able to withstand the large temperature fluctuations. In the offshore sector on production platforms, the premium threads help to ensure that the production strings can withstand high intensity movement over the long term. Drilling does not always take place vertically, but has to change direction for geological reasons. OCTG drill pipes with premium threads also have to withstand these enormous challenges.
Productive and economical thread production requires a stable machine and a rigid tool system, as the materials to be machined are high-strength and difficult-to-cut steels. "The materials to be processed always depend on the required pipe grade. There are steels that are easier to machine, but we always talk about heavy-duty machining when it comes to thread production," explains Benjamin Henkel, Sales Manager Cold Finishing Long Products at SMS group.
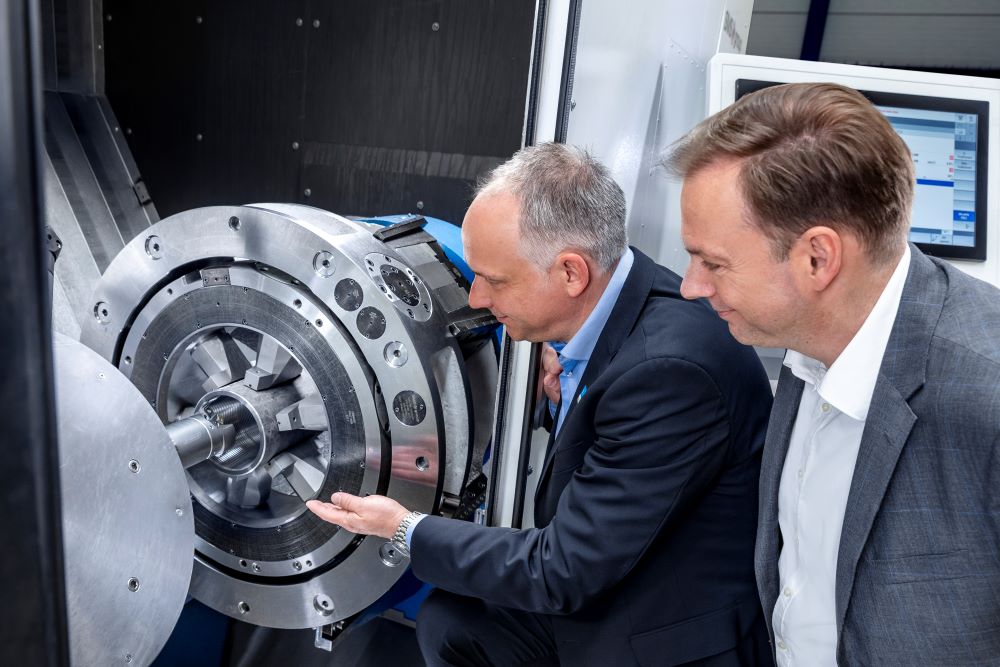
Coupling threading machine
SMS group developed the RMG threading machine for manufacturing pipe couplings. The machine was designed together with international customers and tool manufacturers right from the start. This has resulted in a solution that is completely in line with the market and its requirements. The pipe and tool manufacturers contributed their priorities and ideas for the machine. On this basis, engineers at SMS group developed various concepts and analysed them in a benefit analysis. The result: a horizontal coupling threading machine with a turret head and a rotary indexing chuck for premium socket production. This concept combines the most important advantages: Productivity, precision and flexibility.
The RMG internal thread cutting machine for couplings is based on the field-proven, successfully established TCG pipe threading machine. From this machine for cutting premium external threads, the RMG adopts its core components to provide a rigid machine tool that ensures high precision. Both machines deliver high-quality end products in accordance with international standards, such as API or GOST. In this way, the SMS group is defining new standards as a holistic supplier in the field of OCTG production technology and strengthening its market-leading position. The RMG has six tool holder positions that can be equipped with combination tools. Thanks to intelligent use of three cutting inserts on the combination tools, three work steps can be carried out without having to index the turret, which minimises cycle times. In addition, the horizontal design facilitates chip evacuation and offers significant advantages when feeding workpieces and changing tools.
Avoiding costly mistakes
A highlight of the operation is the integrated machining cycle simulation. This allows the user to simulate the entire process before coupling threading starts and use the visualisation to check whether the programming meets all requirements and target values. "Visual simulation of the workpiece on the HMI before the first chip is even cut avoids expensive errors and creates a high level of process reliability," says Henkel.
"The tools must deliver top performance during the turning process, as the load on the cutting edges is very high," says Götze. Horn provides combination tools for coupling machining to avoid unnecessary tool changes. The System 315 is used to machine the internal threads. A triple, highly accurate, reversible insert with two or three teeth roughs and finishes the threads. The inserts, having a maximum width of 15.5 mm, machine the threads economically thanks to their long life and low cost. Integrated chip breakers ensure good chip control. Coolant is supplied from below and above the insert. A stable clamping screw ensures excellent ergonomics when changing inserts. To minimise machine downtime, the tool holder can be removed in a few simple steps using a precise polygon shank interface (size 80) and replaced with a sister tool, allowing the inserts to be exchanged outside the machine.
The System 315 is suitable for producing API buttress threads, API round threads, premium threads and other thread forms. Thanks to the repeatability achieved, machine operators can cut high-quality threads with an elevated level of process reliability. Rework is minimised thanks to the precision tool holder interface. The long tool life ensures few interruptions to the production process.
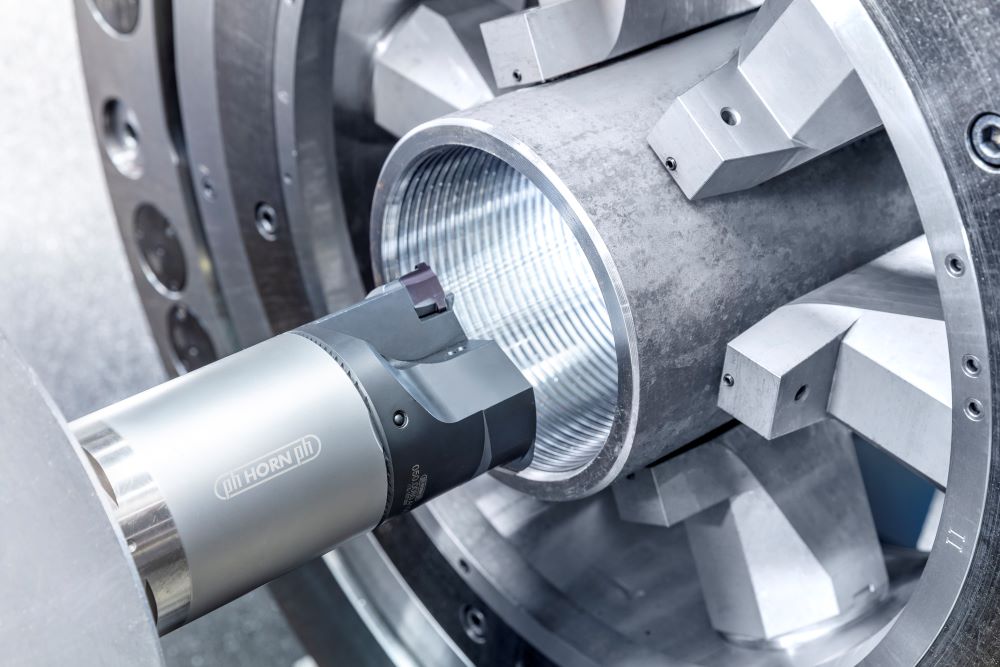
Combination tools in use
The combination tool allows an API buttress thread to be machined without a tool change. In the first operation, ISO inserts are used for facing and turning an external chamfer. Another ISO insert then produces an internal taper and chamfer. The Horn indexable ISO insert then performs the threading in three passes. Two combination tools are needed to produce a premium thread. The internal taper is pre-turned and finished and the sealing seat is pre-turned. After tool change or turret indexing, the type 315 insert carries out thread cutting in ten successive partial cuts. An ISO insert then performs finishing of the internal chamfer and the sealing seat.
"Compared to other tool systems, premium threads can be produced with just two Horn tools instead of the usual five. We achieve high productivity and quality by harmonising the tool holder with S117 and 315 inserts," says Götze. Thanks to the high level of vertical integration in Horn's factory, which ranges from blank production in the company's own carbide production department to grinding and tool holder production through to in-house PVD coating, short delivery times are ensured. In addition, as a process consultant and solution provider, the tool manufacturer supports the user with its own production management. Horn's expertise in the machining of different materials ranges from free-cutting J55-K55, L80 and P110 to Q125 to high-alloy X13Cr and X27Cr.
The SMS group has been working with Horn for several years. Henkel rates the cooperation positively: "Thanks to the commitment of Mr Götze and Horn's design engineers, we have made significant progress with their tool systems to an extent that was previously unforeseeable. I regard the tools as the perfect addition to our RMG coupling threading machine."