14 times faster – and even more potential
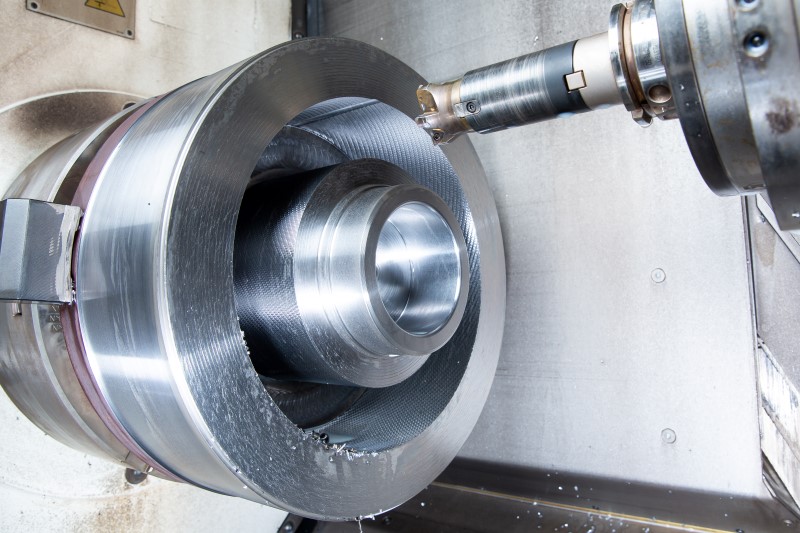
“There is still more potential for improvement,” says Jörg Bamann. By optimising a roughing process, the managing director has been able to save just under 100 minutes per component thanks to the use of the DAH high-feed milling system from Paul Horn GmbH. Bamann has been using tools from the Tübingen-based tool manufacturer in his production facility for 20 years. “As well as reducing the production time, cutting pressure and vibration are significantly lower since we made the switch,” says Bamann.
Horn launched its high-feed milling system ten years ago. The DAH cutters are designed for face milling. As the load is in the axial direction, the spindle is mainly under pressure and the lateral forces are relatively low. Due to the low tendency towards vibration, the tools can reliably absorb the high loads at the usual feed per tooth of fz =1 mm at cutting depths of up to 1.2 mm. The large radius on the main cutting edge of the triple-edged indexable insert results in a soft cut, ensures even distribution of the cutting forces and, in turn, extends the tool life. On the inside, a smaller cutting edge radius makes for quick and easy ramping, whilst a primary and secondary angle result in a stable wedge angle and excellent cutter stability.
“Before switching to high-feed milling, we produced the axial recess in the component with a conventional toroidal milling cutter,” says Bamann. For the machining specialist from Geretsried in Bavaria, axial turning was no longer a viable option: “We tried it with tool solutions from various manufacturers, but none of them had the technical capabilities we needed for producing this recess. Turning it resulted in long chips and, due to the high groove depth, produced vibrations which negatively affected the life of the inserts,” explains the managing director. The chip volume was high. The axial recess has an outer diameter of around 240 mm, is 40 mm wide and has a depth of just under 90 mm without a finishing allowance.
300 workpieces per year required process optimisation
It was a conversation at EMO in Hanover that led the company to switch to Horn's DAH high-feed system. Horn application engineer Korbinian Niedermeier recommended this system for roughing. Every year, Bamann produces around 300 of the components from 42CrMo4 (1.7225), hardened to 1,000 N/mm2. With the previous toroidal milling cutter with indexable inserts, it took Bamann over 100 minutes to rough the recess. Tool life equated to 30 recesses per cutting edge of the five-insert tool. The roughing process was faster than axial turning but resulted in vibration and a high level of noise. Furthermore, the machining time was still too long for Bamann.
“The first tests with the DAH milling cutter were immediately successful. There were just a few parameters that we had to adjust in the test phase,” explains Niedermeier. The application engineer opted for a five-insert mill with a diameter of 40 mm. A CTX 800 TC turning/milling centre from DMG MORI is used to machine the workpiece. The cutting speed is programmed to vc = 150 m/min. The tool is helically interpolated into the workpiece with a continuous infeed depth of ap = 1 mm. The radial feed rate (rotational speed of the component) is vf = 4,777 mm/min and the feed per tooth is fz = 0.8 mm. The new machining time for the recess is now just seven minutes per component and the tool life of the indexable inserts has increased to 90 components per edge. “We are very happy with the result. Using the high-feed milling cutter has reduced the cycle time considerably. The load on the machine has also decreased, as the cutting pressure and vibration have been reduced significantly along with the machining time. And there is still more potential for improvement with regard to machining,” says Bamann.
Hydraulic rotator
The component is one of the core parts of a hydraulic rotator. “It is mainly used in excavator attachments,” explains Bamann. For many applications in construction and forestry, it is essential to be able to rotate attachments. This allows the operator of a demolition excavator, for example, to rotate the demolition shears or concrete crushers in order to position them precisely.
Jörg Bamann's mechanical workshop for CNC milled and turned parts, now in its second generation of ownership, has been producing components for the industrial and trade sectors since 1964. From individual parts to series production, 3D moulded parts or 5-axis machining, Bamann is an expert partner when it comes to the range of components required by his customers. Modern machinery and motivated employees ensure high quality products. The company's many years of experience in processing standard steels, stainless materials, aluminium alloys, non-ferrous metals, titanium and plastics are testament to its expertise and versatility. The use of modern CAD/CAM systems enables components to be machined quickly and cost-effectively to meet customer requirements.