Dynamic HPC milling with the Horn DS system
Paul Horn GmbH is expanding its portfolio of DS-type solid carbide end mills with a new high-performance geometry. This system has been specially designed for use in HPC (high-performance cutting) milling of high-strength steels at high material removal rates. It particularly excels in dynamic roughing applications as well as in standard roughing cycles. The different helix angles create an irregular tooth pitch, making operation exceptionally smooth. The tools’ optimised face geometry reduces the cutting pressure when linear or circular ramping. Improved chip spaces ensure optimal process reliability during chip formation and removal. The system also demonstrates its strengths during finishing. Extremely smooth operation means that high surface quality can be achieved during side milling, for example.
HPC milling of high-strength steels at high material removal rates places significant demands on the tools. New carbide substrates and new tool coating technologies make this process feasible. Horn relies on the ES3P grade with a HiPIMS coating for its milling cutters. High power impulse magnetron sputtering technology offers several advantages and new possibilities when it comes to coating precision tools: it enables the formation of coatings that are very dense and compact, as well as extremely hard and tough. The coatings have a very homogeneous structure and exhibit an even coating thickness, even with complex tool geometries. The coating demonstrates very high layer adhesion, thus ensuring good cutting edge stability. Thanks to its high temperature resistance, the coating serves as a heat shield and reduces the amount of heat transferred to the carbide.
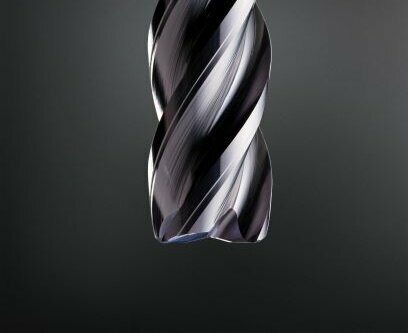
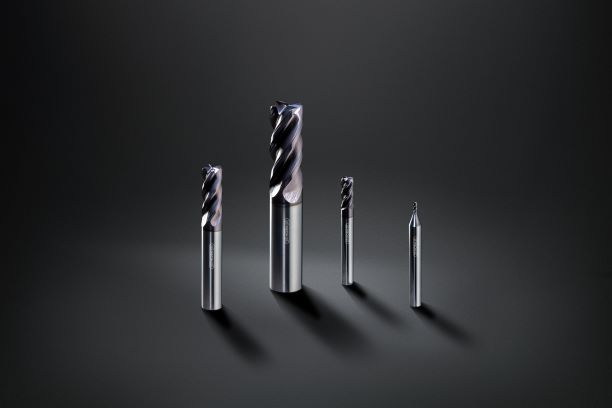