Efficient boring of stainless steels
Horn has added a new variant to the Supermini system especially for boring stainless steels. The optimised cutting geometry combined with the IG35 coating ensure high productivity and process reliability. With a coating thickness of just 0.003 mm (0.0001") and a maximum operating temperature of around 1,100 degrees Celsius (2012 degrees Fahrenheit), the tool achieves on average twice the life of a conventionally coated tool. Horn coats the tools in-house in its own HiPIMS coating systems. This enables not only high cutting performance but also fast delivery of the tools.
Boring, profile turning, internal grooving, threading, chamfering, face grooving, drilling and slot broaching: The Supermini tool system can be adapted and used for numerous machining operations. The solid carbide inserts are used for machining bores with diameters from 0.2 mm (0.008") to around 10 mm (0.394"). Horn developed the carbide blanks of the tool as a teardrop shape. This enables precise and large contact surfaces in the tool holder, which results in greater rigidity of the overall system. Furthermore, the teardrop shape prevents the insert from twisting, which leads to consistently precise positioning of the centre height of the tool. For long tool overhangs, it reduces deflection and minimises vibration during the turning process. Depending on the application and the diameter to be machined, Horn offers the inserts in three different sizes (types 105, 109 and 110) and various blank types. All variants allow for internal coolant supply directly to the cutting zone. The Horn tool portfolio contains around 2,500 different standard variants of the Supermini. In addition, Horn has solved users' problems with countless customised solutions.
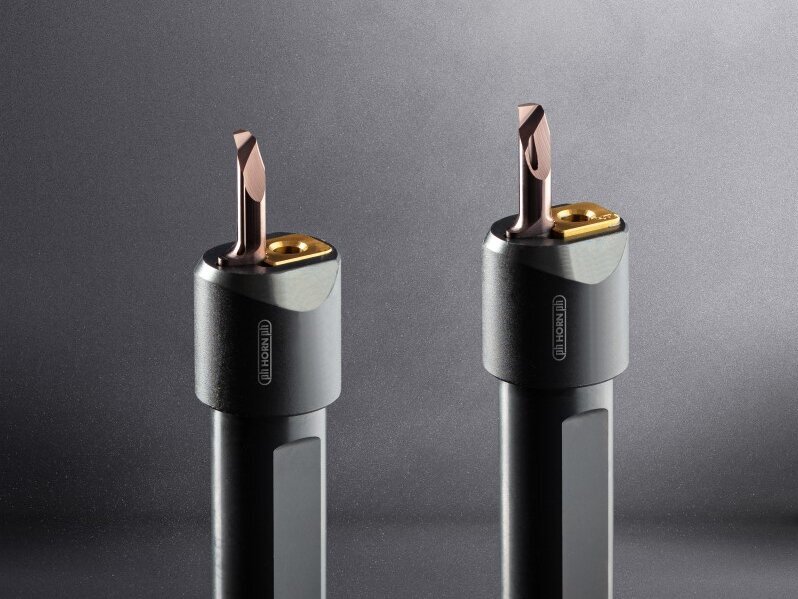
Efficient boring of stainless steels
Horn has added a new variant to the Supermini system especially for boring stainless steels. The optimised cutting geometry combined with the IG35 coating ensure high productivity and process reliability. With a coating thickness of just 0.003 mm (0.0001") and a maximum operating temperature of around 1,100 degrees Celsius (2012 degrees Fahrenheit), the tool achieves on average twice the life of a conventionally coated tool. Horn coats the tools in-house in its own HiPIMS coating systems. This enables not only high cutting performance but also fast delivery of the tools.
Boring, profile turning, internal grooving, threading, chamfering, face grooving, drilling and slot broaching: The Supermini tool system can be adapted and used for numerous machining operations. The solid carbide inserts are used for machining bores with diameters from 0.2 mm (0.008") to around 10 mm (0.394"). Horn developed the carbide blanks of the tool as a teardrop shape. This enables precise and large contact surfaces in the tool holder, which results in greater rigidity of the overall system. Furthermore, the teardrop shape prevents the insert from twisting, which leads to consistently precise positioning of the centre height of the tool. For long tool overhangs, it reduces deflection and minimises vibration during the turning process. Depending on the application and the diameter to be machined, Horn offers the inserts in three different sizes (types 105, 109 and 110) and various blank types. All variants allow for internal coolant supply directly to the cutting zone. The Horn tool portfolio contains around 2,500 different standard variants of the Supermini. In addition, Horn has solved users' problems with countless customised solutions.
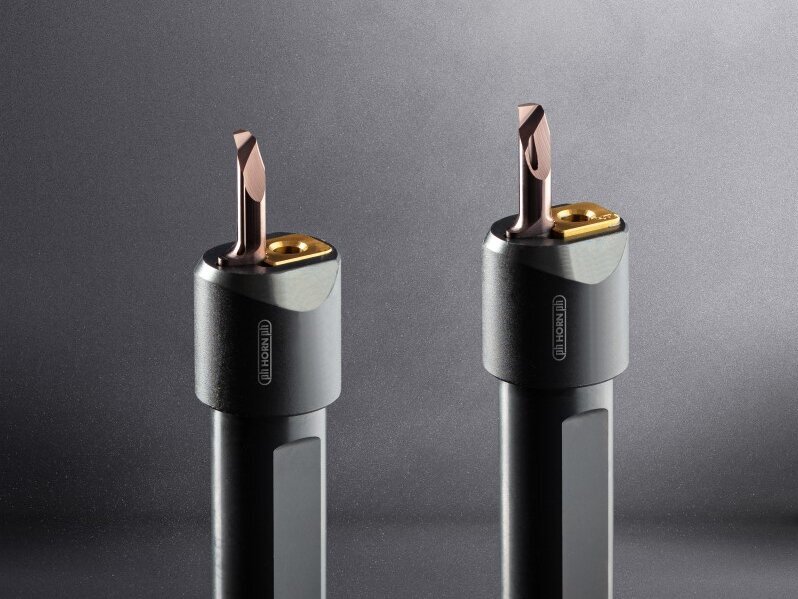