Émotions et artisanat
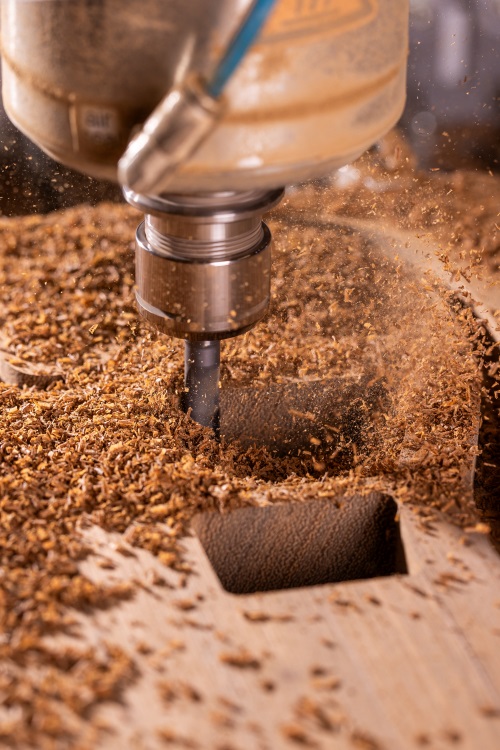
Rock “n” roll, blues et heavy metal. Aucun autre instrument ne suscite autant d'émotions parmi le public que la guitare électrique. Cet instrument joue un rôle central dans la plupart des genres musicaux et a caractérisé des générations de musiciens depuis les années 1930. À côté des guitares produites en série, il existe également de petites entreprises artisanales qui perfectionnent la fabrication des guitares électriques dans les moindres détails. Marc Locher est à la tête de l'une d'entre elles. Avec son entreprise EBG-Instruments, il innove tout en respectant les anciennes traditions. Pour un projet en cours, une Telecaster, il utilise des pièces imprimées en 3D en titane et des fraises diamantées CVD. Locher a reçu le soutien de Paul Horn GmbH pour ce projet.
Les critiques affirment que n'importe qui peut fabriquer une guitare électrique avec une scie, un tournevis et un fer à souder. En théorie, c'est vrai, mais personne ne veut l'entendre. Contrairement aux guitares acoustiques, la plupart des guitares électriques classiques n'ont pas de résonateur creux pour amplifier le son des cordes. Certaines guitares électriques ont un corps creux, mais la sonorité est généralement influencée par la conception, le choix du bois, l'accastillage, les micros et la qualité de fabrication. Les micros sont des bobines magnétiques qui convertissent les vibrations des cordes en signaux électriques. Lorsque la guitare est jouée, ces signaux passent par un processeur d'effets, puis sont amplifiés dans un amplificateur et restitués sous forme de son par un haut-parleur. La technique de jeu, le processeur d'effets et l'amplificateur produisent le son désiré et familier de la guitare électrique.
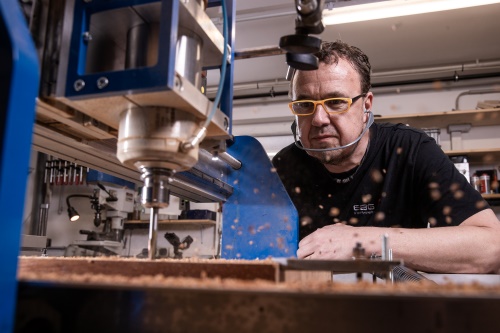
Avec ses instruments, Locher démontre de manière impressionnante comment combiner l'artisanat traditionnel de la fabrication de guitares avec de nouvelles idées et technologies. Par exemple, il combine des corps en aluminium fraisés par CNC avec des bois nobles et des manches en fibre de carbone. Il fabrique environ six guitares électriques ou basses par an. Tous les instruments sont personnalisés en fonction des souhaits et des exigences du client. Dans la vie de tous les jours, Locher travaille comme enseignant dans une école professionnelle dans le domaine de la technologie CNC. Pendant son temps libre, il travaille sur ses instruments dans sa cave. Dans son sous-sol, il a aménagé un espace de fabrication de guitares avec tout ce que le cœur d'un technicien peut désirer. Installé dans deux pièces, l'atelier dispose d'une fraiseuse CNC, de nombreuses machines à bois, d'une cabine de peinture et d'un poste de travail pour l'assemblage final. Sa cave abrite également un petit trésor sous la forme d'un magasin de bois de timbre. De beaux bois rares tels que l'ébène certifié, l'érable ondé et l'acajou y sont entreposés.
"Je suis toujours à la recherche de vieux escaliers en bois des années 50 et 60. À l'époque, les escaliers étaient souvent fabriqués en acajou massif", explique Locher. Il utilise les vieux escaliers pour fabriquer les corps et les manches des guitares. « Le bois convient parfaitement à la fabrication d'une guitare, car il est relativement peu sollicité en raison de son âge et des conditions sèches qui règnent dans les maisons », explique M. Locher. Il utilise également ce bois précieux pour son projet actuel, une Telecaster. Cette forme est l'un des modèles de guitare électrique les plus populaires de tous les temps. Elle a été développée par le célèbre fabricant de guitares Leo Fender. Cependant, la Telecaster de Locher n'est pas une simple copie de la guitare de Fender. Avec des matériaux et des composants spéciaux, un look épuré et de nombreux raccords vissés cachés sur le devant de la guitare, il s'agit d'une pièce unique qui nécessite beaucoup de temps, de travail et de savoir-faire, ainsi que des techniques de fabrication spéciales.
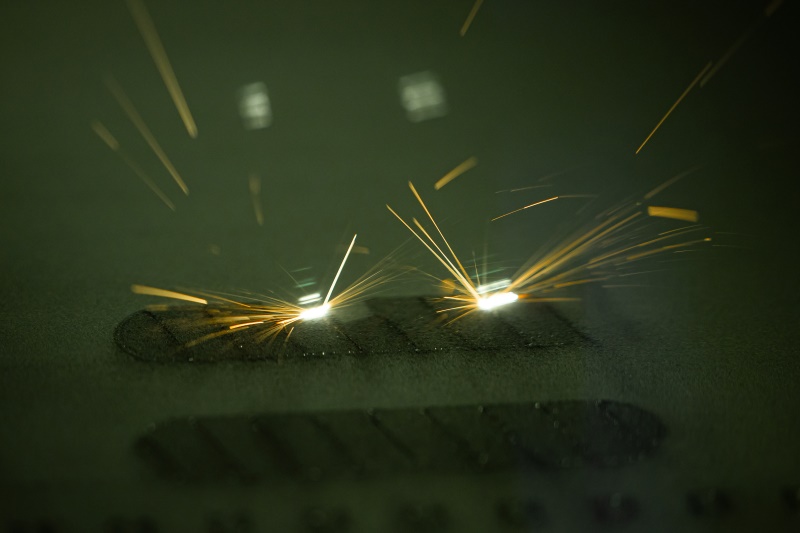
« La construction d'instruments exceptionnels nécessite également l'utilisation de matériaux spéciaux », explique M. Locher. C'est pourquoi il a décidé d'utiliser des composants en titane, notamment le chevalet, qui est monté sur le corps de la guitare et soutient les cordes. Le chevalet est un élément très important de la guitare, car il a une influence majeure sur l'attaque (vitesse de développement du son) et le sustain (durée du son). Locher s'est adressé aux spécialistes de l'impression 3D de HORN avec le modèle 3D qu'il avait lui-même conçu pour faire imprimer ces pièces en titane. En raison de la géométrie des composants et de la finesse des parois, il était hors de question de fraiser les pièces, car cela aurait pris trop de temps et aurait été trop coûteux.
Locher a eu de la chance : HORN avait déjà lancé son projet de fabrication additive au printemps 2018. Aujourd'hui, elle est devenue une zone de production à part entière. HORN utilise la fabrication additive dans sa propre production d'outils, notamment pour la fabrication de prototypes, de pièces spéciales et de porte-outils, ainsi que pour l'optimisation des attachements avec liquide de refroidissement. HORN met les possibilités étendues offertes par la fabrication additive à la disposition de clients et de partenaires tels que Locher. La fabrication additive n'a de sens que si elle apporte un avantage technologique. Cependant, dans de nombreux cas, il n'y a pas d'avantage économique à fabriquer de manière additive un composant qui était auparavant produit de manière conventionnelle. C'est le cas, par exemple, des pièces tournées qui peuvent être produites rapidement sur des tours automatiques à poupée mobile. La fabrication additive serait également trop coûteuse en termes de reprise pour la finition.
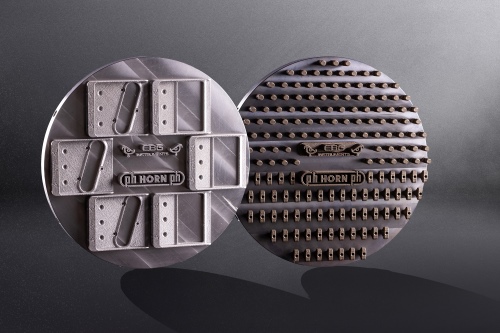
Pour des projets tels que les guitares électriques de Locher, HORN utilise la fusion sélective au laser, également connue sous le nom de processus de lit de poudre. La poudre de métal est appliquée en couche sur une plate-forme de fabrication et exposée à un laser dans les zones où elle doit être fondue. La plate-forme est progressivement abaissée et le processus est répété jusqu'à ce que la hauteur de la pièce requise soit atteinte. HORN utilise l'aluminium (AlSi10Mg), l'acier inoxydable (1.4404), l'acier à outils (1.2709) et le titane pour l'impression 3D. D'autres matériaux sont actuellement à l'essai. Le volume de construction est de 300 mm (11.811" ) de diamètre par 400 mm (15.748 ") de hauteur. Comme HORN dispose de tous les processus de fabrication additive en interne, les spécialistes de la zone de production peuvent répondre directement aux besoins des clients. Les pièces sont fabriquées dans différents modèles en fonction de l'utilisation prévue. HORN assiste également le client dans la conception et la sélection des paramètres appropriés pour la fusion de la poudre. La production s'effectue en fonction des exigences du client, qu'il s'agisse de composants bruts ou de composants finis. Un autre avantage de la production interne de HORN est le large éventail de machines et d'équipements de métrologie installés. Cela permet de gagner du temps et a une influence directe sur tous les processus de production.
Les composants imprimés de la guitare sont séparés de la plate-forme de construction par érosion du fil. Cependant, en raison de la forte contrainte exercée sur les composants à parois minces, il est nécessaire de les soumettre à un traitement thermique avant de les éroder, faute de quoi ils se déformeraient après la séparation. Le traitement thermique s'effectue à une température de 650 degrés celsius et dure environ deux heures. Locher a opté pour le microbillage pour la finition optique des composants. En plus du pont, HORN a également imprimé d'autres composants pour la Telecaster de Locher.
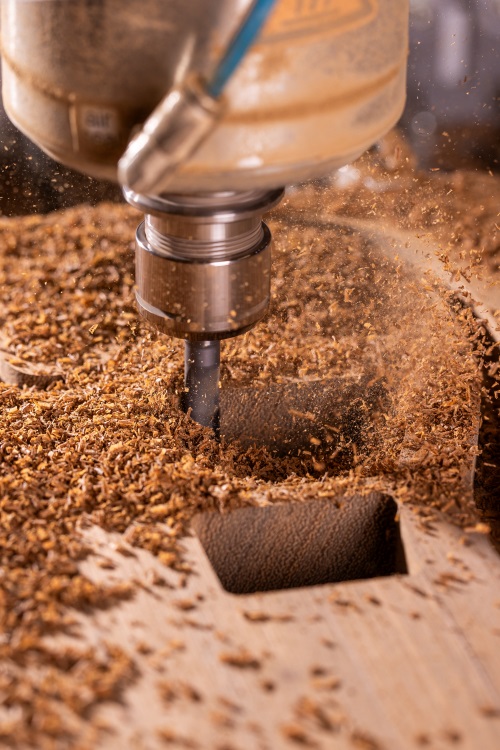
Locher usine le corps de la guitare à partir d'un matériau solide. La pièce brute provient d'une marche d'escalier en acajou. Locher la coupe dans le sens de la longueur et colle les deux parties en miroir. « En plus d'offrir une plus grande stabilité, le collage en miroir de certains bois est également un facteur esthétique dans la fabrication des guitares », explique Locher. On utilise une colle spéciale pour instruments, qui durcit presque autant que le verre. C'est très important, car des joints de colle mous absorberaient les vibrations et affecteraient le son de l'instrument. Pour l'usinage du corps, Locher utilise une fraiseuse CNC à trois axes dotée d'une broche à grande vitesse et d'une fraise diamantée à quatre arêtes de HORN.
La longueur de coupe de l'outil est d'environ 45 mm (1.772“). Cela suffit pour réaliser la plupart des opérations de fraisage sur la carrosserie. Grâce à la netteté des arêtes de coupe, Locher gagne du temps lors du ponçage ultérieur. "J'ai été très impressionné par les surfaces fraisées. Les flancs de la fraise sont comme finement affûtés et il n'y a pas de bavure sur les arêtes. Cela permet de gagner du temps lors du ponçage ultérieur des surfaces en bois", explique Locher. L'outil fraise également des poches sans aucun problème en s'enfonçant dans le solide. Par exemple, Locher fraise de nombreuses poches hexagonales ainsi que le compartiment électrique dans la carrosserie afin d'en réduire le poids. Locher colle ensuite un plateau en acajou de 5 mm (0.197“) d'épaisseur sur les poches et les passages de câbles fraisés.
La fabrication d'une guitare de ce niveau combine de nombreuses compétences. Outre une expertise mécanique dans le domaine de la technologie CNC, des compétences de menuisier, d'artisan et de laqueur sont requises. Une fois que les différents éléments de la guitare ont été fabriqués et que le travail de ponçage fin a été effectué, les pièces sont peintes. Locher a opté pour un blanc nacré métallisé pour le corps de la guitare. Le manche en érable ondé et en ébène n'a reçu qu'une teinture brun foncé et une couche de laque transparente afin que les belles veines du bois restent visibles. « À l'aide d'un apprêt, d'une laque colorée et d'une laque transparente, nous appliquons neuf couches très fines », explique M. Locher. Chaque couche est poncée après séchage pour préparer la couche suivante. La peinture produit toujours un effet peau d'orange. Celui-ci se caractérise par une surface légèrement ondulée. Les dernières couches de laque transparente font donc l'objet d'un traitement spécial. Après séchage, elles sont poncées avec des grains de plus en plus fins et polies jusqu'à l'obtention d'une grande brillance à l'aide de différents produits. « Après ces opérations fastidieuses, la couche de vernis réfléchit la lumière comme une couche de verre », explique M. Locher. L'assemblage final et l'accordage des cordes constituent toujours un moment particulier pour lui. "La première note de l'instrument terminé marque aussi le début des adieux. C'est difficile pour moi, car j'ai passé deux à quatre mois à le construire", explique Locher. Souvent, il livre personnellement ses guitares à leurs nouveaux propriétaires dans toute l'Europe.
Locher porte un jugement positif sur la collaboration avec HORN : "Depuis l'idée initiale d'imprimer les composants en titane jusqu'à la conception technique, en passant par les conseils axés sur les objectifs et la mise en œuvre, la collaboration a été très professionnelle et s'est déroulée sans heurts. Je me réjouis déjà des prochains projets. Merci beaucoup pour cela."