High-polish milling instead of polishing

An application from Germering in Bavaria shows that special machines are not required for milling high-polish plastic surfaces. The Enggruber company, in collaboration with Paul Horn GmbH, is crystal clear that this even works with conventional machines. The tools are monocrystalline diamond, which ensure surface quality to within nanometres during ultra-precision machining. "The quality of the tool cutting edge is the decisive factor for the surface finish that can be achieved," says HORN tool specialist and product manager for high-hardness cutting materials, Aribert Schroth.
In Germering, to the west of Munich, in an industrial building that looks inconspicuous from the outside, you would never guess that high-quality acrylic glass displays are produced here for the elite in various industry sectors. In the display industry, Thomas Enggruber is known as the "Red Adair" - the famous firefighter. With his many years of expertise, he puts out fires and solves problems before they become a problem. Enggruber's portfolio includes cosmetics displays, awards and trophies, furniture and other products made of acrylic and Plexiglass. He also manufactures his own products in his workshop. For example, he produces picture frames with a 3D effect and elegant chopping boards made from crystal-clear plastic.
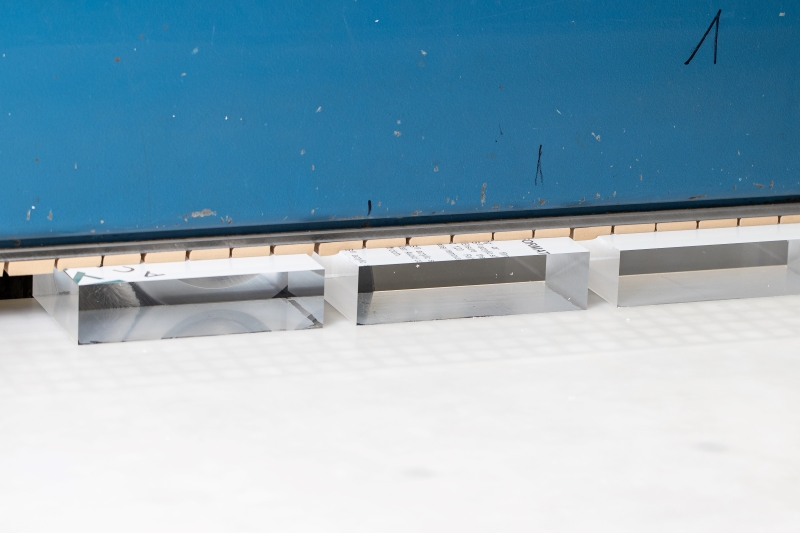
Fire and flame
"We look closely at the processes in our factory and are constantly looking for potential to further optimise them," says Enggruber. One major goal was to process the edges of acrylic glass blocks or panels. "We receive the raw material in the form of sawn pieces. In the production process for large panels, the two sides are already crystal clear and are covered with protective film. However, when the panels are cut to size, the four edges are rough when they are delivered," explains Enggruber. There are various ways of making these rough edges crystal clear. On the one hand, acrylic glass can be flame polished. This involves carefully passing a flame from an acetylene torch over the edges. This creates a clear surface, but it is not perfectly flat. In addition, hairline cracks may also appear on the edges. On the other hand, the edges can be polished by hand using a polishing machine, also known as a buffing machine. Buffing provides a shiny finish, but requires a lot of time, especially for large quantities.
Another process for machining the edges is milling with monocrystalline diamond (MCD) tipped tools. Enggruber had been using this process for some time, but the surface results were not completely satisfactory for him. He was also bothered by the time-consuming handling and adjustment of the previously used tool systems. "To change the inserts, we had to remove the entire tool and then readjust it again. This was always time consuming," says Enggruber. In order to optimise this effort and the result, Enggruber set out to find a new tool solution.
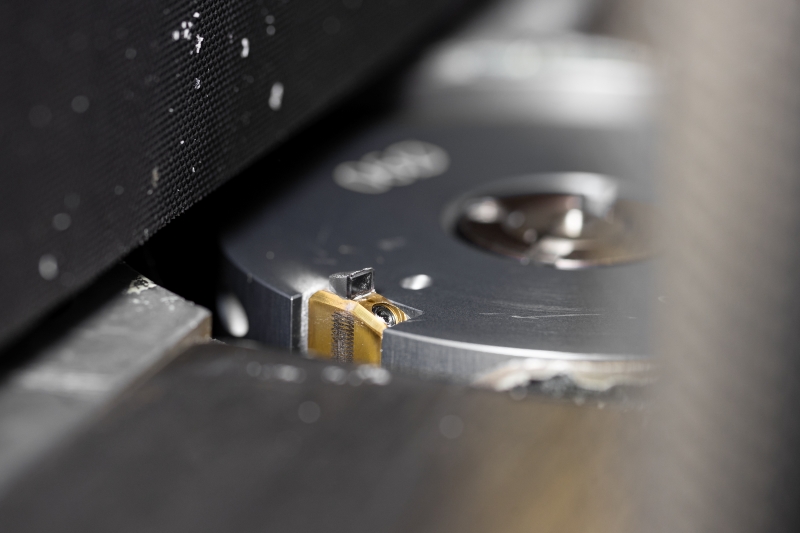
Supermini in action
A high-polish machining video uploaded by HORN to a well-known online video platform aroused Enggruber's curiosity, who then contacted the HORN sales representative Helmut Hoffmann. Together with Aribert Schroth, Hoffmann analysed Enggruber's problems and developed a new and more user-friendly solution. "With our expertise in interchangeable inserts, the solution was quickly obvious," says Hoffmann. The existing milling cutter body is equipped with Posalux interfaces to accommodate the inserts. HORN technicians therefore designed a Posalux cassette in which the seat for the HORN insert is milled. The insert chosen was a special shape from the HORN Supermini tool system , which can be easily and precisely clamped from the front using a clamping screw in the cassette. This eliminated the need to completely remove the milling cutter body.
The milling tools have multiple cutting edges with up to five teeth and a diameter of 120 mm (4.724"). However, only one MCD insert is fitted per tool. The other inserts serve as pre-cutters and are set back by around 0.1 mm (0.004"). "Only one MCD insert is used to produce the high-polish surface so that it is not damaged by recutting," explains Schroth.
Enggruber uses two different machines for high-polish milling the edges, which originally came from the woodworking industry. "In our industry, this machine concept of polishing milling machines has been used for a long time," says Enggruber. The machines only have one axis that carries out the milling operation. The acrylic glass blocks or panels are clamped by a foam-padded hold-down device. The other machine concept is similar to a planing machine. Here, the workpiece is clamped between two wide belts and guided over the milling cutter.
Craftsmanship
The quality of the tool cutting edge plays an important role in producing surfaces with a mirror finish. The quality of the cutting edge is reflected in the surface to be machined. The final grinding or polishing of the MCD inserts is akin to craftsmanship. Similar to the cutting of diamond jewellery, the finishing of a tool cutting edge for high-polish machining is done by hand using grinding pliers. Air-bearing grinding tables with a solid granite top provide optimum conditions for grinding the inserts. A microscope with 200x magnification is used for visual inspection. Under this magnification, the cutting edge must be absolutely free of nicks. The resulting insert has a maximum radius of 0.0002 mm (0.000008").
Synthetic diamonds are mainly used for high-polish machining. Two different processes are used to produce the synthetic stones. In the HPHT process (High Pressure, High Temperature), the diamonds are created under high pressure and heat. In other words in an almost natural way, not over millions of years but within a few hours or days, depending on the desired size. In this process, pure graphite powder is transformed into a diamond at a pressure of 60,000 bar and a temperature of 1,500 degrees Celsius (2,732 degrees Fahrenheit). Diamonds from this process are characterised by a light yellowish colour, which is caused by the refraction of light from embedded nitrogen atoms. The maximum edge length of synthetic stones is 10 mm (0.394"). Dimensions beyond this are theoretically possible, but would not be economical.
HORN relies on the even purer MCC diamonds for equipping MCD tools. These monocrystalline stones are created using the CVD process. Various gases, mainly methane, are used as a source of carbon, which is deposited during the process to allow the diamond to grow. The diamonds are characterised by their crystal clear to light brownish colour, depending on their thickness. A major advantage of this process is the edge length of the stones that is possible. This means even long tools with cutting edge lengths of 30 mm (1.181"), for example, can be realised. Previously, natural diamonds had to be used for such tools, which are impractical due to their high price, scarcity and natural inclusions.